Laser Marking Systems / Laser Markers
7 Ways Laser Marking Improves Part Traceability
-
Tags:
- Laser Marking , Medical , Aerospace
Laser marking is the process of using a laser light to engrave, etch, or anneal a mark on metal, ceramic, plastic, wood, or rubber. The process is used across industries for adding designs, textures, and cleaning or preparing surfaces.
As industries evolve and part tracing becomes more important, manufacturers are looking to laser markers as a reliable tool for part traceability.
Laser marking improves traceability with its automated, fast, cost-effective, precise, permanent, and no-contact marking style. In this blog, we’ll look at these improvements and how they apply to the automotive, medical, and aerospace industries in particular.
What Is Part Marking and Traceability?
Traceability, a critical aspect of quality assurance and supply chain management, involves tracking parts throughout the supply chain. The part traceability process is facilitated by part marking, which is the process of adding identifying text, logos, or 2D codes on parts.
How Laser Marking Improves Part Tracing
There are a few choices for part tracing marks, like chemical etching, dot peening, ink marking, stamping, and laser marking. Out of all the part traceability methods, laser marking for traceability is generally the most reliable, precise, automated, and environmentally friendly option for improving part tracing.
Let’s look at seven ways this process improves traceability in manufacturing.
1. Laser Marking for Traceability Is Automated
Laser marking machines are completely automated and programmed for repetitive marking. The laser marking automation streamlines the traceability process and makes it accessible for all manufacturing plants. It also means that little to no human input is required, freeing up time for operators and engineers to perform other tasks.
2. Laser Marking for Traceability Is Fast
Lasers add traceability marks in seconds and require no preparation or finishing processes for the mark. As such, using laser marking for traceability adds no time burden to the manufacturing process. It’s also faster than alternatives like dot peening, chemical etching, and ink printing. Using a very fast process such as laser marking ensures that, even if capacity needs ramp up, marking will not become the bottleneck in your manufacturing process.
3. Laser Marking for Traceability Is Cost Effective
Because of the speed of laser marking, the cost per mark is low. Additionally, the laser marking machine only requires one upfront cost and no extra consumable costs unlike most other marking methods.
4. Laser Marking for Traceability Is Precise
Laser beams are smaller than the size of a human hair, so they’re extremely precise. The precision means that laser traceability marks are clear, easy to read, and flexible for shapes with curved edges or limited marking space. It also gives peace of mind that quality concerns will not arise down the road.
5. Laser Marking for Traceability Is Permanent
Laser marks are permanent and cannot be smeared, scratched, or corroded off. Other marks, like ink, can be smudged, labels can be torn off, and chemical etching can corrode. Being that the entire premise of traceability markings is that they remain legible for reading down the road, it can be detrimental to a business if these marks are not resistant to the environment the parts will live in.
6. Laser Marking for Traceability Is Environmentally Friendly
Laser marking does not use any consumables that contribute to environmental waste. Additionally, there’s limited energy used because of the fast part traceability marking speed. Other methods like chemical etching and printing use consumables and generate waste.
7. Laser Marking for Traceability Is No Contact
For laser marking, “no contact” means sensitive parts can also have traceability marks without any functional effects. When comparing no-contact laser marking vs dot peen marking machines, lasers have a clear advantage: dot peen uses friction to add marks and cannot mark sensitive parts.
Sensitive parts usually have to rely on ink or paper labeling, but these methods smudge off. Laser marking means that sensitive parts can also benefit from a permanent mark.
Key Industries That Benefit From Laser Marking for Traceability
Automotive Part Traceability
The automotive industry is known for mass production, yearly innovation, and strict safety standards. This means vehicles and their parts move through production quickly, and new products constantly hit the market. Using laser marking for the automotive industry keeps up with these trends.
Thanks to the incredible speed of laser marking, the traceability marking process can easily handle the pace and scale of mass production of vehicles and parts. The permanency and durability of the mark are also crucial for the automotive industry. Vehicle parts withstand decades of dirt, oil, friction, wear and tear, and corrosion contamination—laser marks do, too.
Laser marking traceability ensures parts can always be traced, no matter how long it has been since production.
Medical Device Part Traceability
The medical device industry is one of the strictest with part traceability. All medical devices, besides class 1 commercial devices, require a unique device identifier (UDI). The UDI is a traceability 2D code that stores a device’s traceability history. The strict regulations are to protect patients from malfunctions and catch counterfeit devices.
The permanency, precision, and no contact characteristics of laser marking traceability marks are beneficial to the industry. Medical devices endure constant sanitation and contact with bodily fluids. Because laser-marked traceability marks are permanent, they withstand all contact with outside contaminants.
Compatibility with the human body is another key benefit of laser marking for traceability. Since laser marks are no contact, the marks are biocompatible and do not have any effect on the functionality of a device. This means laser marks can even pass the strictest stipulations such as those for implantable medical devices that end up inside the bodies of patients.
Lastly, medical devices are commonly atypical geometric shapes with limited marking space. Despite that, a precise laser marking machine can easily mark these devices.
Aerospace Part Traceability
Safety and complex supply chains with many stops are the motivation for traceability requirements in the aerospace industry. The Federal Aviation Association (FAA) states that aircraft require fireproof traceability information that will withstand normal use and accidents. Laser marking for traceability is beneficial in this case because of the permanency and precision of the mark.
Aircraft parts experience extreme environmental changes, friction, and corrosion—the laser mark withstands it all. Additionally, the aerospace industry frequently used uniquely shaped parts with minimal marking space, like turbines and gears. A laser marking machine’s precision marks easily on these hard-to-reach surfaces.
Integrating Laser Marking Into Your Part-Tracing Applications
Fiber, hybrid, and UV lasers are popular machines for part traceability applications. Choosing between the three depends on your marking material, desired speed, and type of marking.
Here is an introduction to KEYENCE’s lasers for traceability. All include autofocus, auto-positioning, and 3-axis control for flexibility around curved parts.
Fiber Laser
A fiber laser is a powerful and fast laser with a 1090 nm wavelength. It’s known for its engraving and annealing capabilities on hard metal. KEYENCE’s fiber laser is the 3-Axis MD-F Series Fiber Laser Marker.
Hybrid Laser
Hybrid lasers are a combination of a YVO₄ and a fiber laser. These lasers are notable for their long service life, high output, and depth of focus. KEYENCE’s hybrid laser is the 3-Axis MD-X Series Hybrid Laser Marker.
UV Laser
UV lasers use a 355 nm laser to perform “cold marking.” These lasers are specialized for heat-sensitive or heat-resistant materials because of the short intense wavelength that doesn’t apply any heat. They are generally the laser of choice for plastics and products where any application of heat can lead to failed environmental resistance testing. KEYENCE’s UV laser is the 3-Axis MD-U Series UV Laser Marker.
Ready to Incorporate Laser Marking Into Your Part Traceability?
Your traceability processes have an opportunity to be automated, faster, cost-effective, precise, environmentally friendly, no contact, and last forever with laser marking. So why not use a laser marking machine for part traceability?
KEYENCE is an industry leader in laser marking machines that suit manufacturing needs, and we’re here to help you pick your best fit. If you’re ready to learn more or switch from dot peening, ink printing, or chemical etching to a laser marking machine instead, contact KEYENCE today.
Related Downloads
![MARKING APPLICATIONS - Component Traceability in Automotive Manufacturing [Engine Compartment]](/img/asset/AS_46961_L.jpg)
![MARKING APPLICATIONS Component Traceability in Automotive Manufacturing [Body and Exterior Parts]](/img/asset/AS_101893_L.jpg)
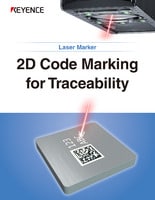
2D codes are used to store date codes, lot codes, serial numbers, and more. Users who are considering 2D code marking should read this laser marking guidebook.