Optical Comparator (Profile Projector)
What is the Extrusion Process? Types & Advantages
Curious about extrusion or how the extrusion process works? In this article, we’ll explain exactly what extrusion is, describe the extruding process, and discuss the advantages and disadvantages of extruding.
What is Extrusion?
Extrusion is a metal-forming technique that shapes a material by pushing it through a die. The extruding process mimics toothpaste pushed out of its tube and forming into the shape of the tube’s opening.
Extrusion Terms
When discussing this process, many common terms arise. Here are a few:
Billet
A billet is a cylindrical metal that is processed in the extruding process.
Die
A die is a manufacturing medium that shapes or cuts materials. In the extruding process, the die is the machine a billet is pushed through and comes out of with a new shape.
Extrusion Ramp
The extrusion ramp is the foundation the billet slides along when going through the extrusion machine.
Hollow
A hollow is a final extrusion shape that has one or more openings. Examples of hollows are square, rectangular, or circular tubes.
Puller
The puller is the mechanical arm that pulls the extruded shape out of the die.
Quench
Quench is the cooling process of shooting the extruded part with cold air or cold water after heating in the extruding process.
Ram
A ram is a machine that adds pressure to the billet to move through the die.
Semi-Hollow
A semi-hollow is a final extrusion shape with a partially enclosed opening—for example, a C channel.
Solid
A solid is a type of final extrusion shape with no enclosed openings—for instance, a rod, beam, or angle.
How Does the Extrusion Process Work?
There are numerous steps that are used by manufacturers. Here is a breakdown of each:
Step 1: Die and Billet Preparation
Before extrusion occurs, die and billet preparation is required for optimal results. Preparation in hot extrusion includes heating the die oven between 400 and 500 degrees Celsius (approximately 750 to 930 degrees Fahrenheit) and placing the billet inside.
In the case of another extruding process, like cold or friction extruding, this involves lubricating the extrusion ramp or metal for easier entry into the die.
Step 2: Billet Extrusion
In step two, a ram adds 100 to 15,000 tons of pressure to the billet and pushes it through the die. The method in which the ram adds pressure depends on whether the extruding process is hot, cold, or friction.
As the billet comes out of the die, a puller attached to the extrusion machine will slowly start pulling the billet along the extrusion ramp to make room for more to come out.
Step 3: First Cooling
After the billet comes out of the die, the extrusion machine quenches the new part. The quenching solidifies the shape and prevents deformities.
Step 4: Die Removal
Since the billet comes out of the die passage still attached to the original form, it needs to be cut by a hot saw to remove it from the die. After removal, the newly formed material cools to room temperature.
Step 5: Finishing
Last in the extruding process is finishing on the formed part. Finishing may be cutting the extruded shape into smaller pieces, removing oxidation, or shining.
Types of Extrusion
Hot Extrusion
Hot extrusion uses a heated die oven for the extruding process. The heat makes the billet malleable, which is particularly effective for helping shape hard metals.
Examples of metals used for hot extrusion:
- Magnesium
- Copper
- Steel
- Advantages
-
The malleability from heat is a massive advantage to heat extrusion over other methods. Since the metal is more malleable, the hot extruding process produces more metal in less time, and can make more complex shapes than alternative methods.
- Disadvantages
-
Although the heat is an advantage in some terms, it can also be a disadvantage. The heat from the die creates an oxide layer that requires different finishing processes on the extruded part. These additional finishing steps take up time, energy, and costs.
Cold Extrusion
Cold extrusion isn’t necessarily cold; it just doesn’t use heat for the extrusion process. Because of this, cold extrusion is used on softer metals and uses more lubrication.
Examples of metals used for cold extrusion:
- Aluminum (and alloys)
- Lead
- Tin
- Advantages
-
An obvious advantage to cold extrusion is the absence of heat surfacing issues like oxidation layers. That’s not the only advantage, though. The cold extrusion also doesn’t use as much energy or time as the hot extrusion because it doesn’t require heating the die.
- Disadvantages
-
Although cold extrusion avoids the detrimental effects of heat, it is a limiting extruding process. Because of the lack of heat, the metal isn’t as malleable. In turn, there is a higher cost for lubrication and limited shapes that cold extrusion can achieve.
Friction Extrusion
Friction extrusion uses frictional heating to move the material through the die and into an extruded part. The metal is forcibly and quickly rotated against the die hole to create heat for increasing malleability. Once the metal generates enough heat to be malleable, it moves through the die.
- Advantages
-
Friction extrusion is the best of both worlds of cold and hot extrusion. Similarly to hot extrusion, it uses heat to make metals malleable for complex shapes and a seamless process. However, it doesn’t use the heating-up energy that hot extrusion requires.
- Disadvantages
-
Although friction extrusion avoids using machine energy for heat, it still uses a lot of energy to make friction between the billet and the die. Also, friction extrusion requires extra finishing because of the formation of heat oxidation.
Extrusion in Manufacturing Process
The extruding process is vital for shaping metals to make beams, tubes, angles, rods, and C channels. From forming the pipes under our sinks, picture frames holding precious family photos, and the bleachers we sit on, the extruding process is limitless.
In aerospace, interior design, medical devices, food, automotive, and more, there’s no industry that doesn’t benefit from the extruding process. The versatility in processes, from cold, to hot, to friction, there is always an extrusion process that fits a forming project.
KEYENCE’s IM Series provides accurate and instant measurement solutions to extrusion manufacturers. Give us a call at 1-888-539-3623 to discuss your needs or questions.
Related Downloads
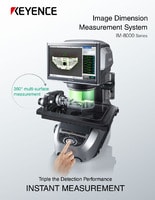
Brochure for the IM-8000 Series Image Dimension Measurement System. Accurately measure parts in seconds at the push of a button.