Laser Sensors
A rich lineup of remote setup and received light intensity differentiation laser sensors. This page introduces compact digital CMOS laser sensors that have a built-in amplifier and boast high durability and stability, reflective/thrubeam model laser displacement sensors that are easy to use and have the versatility to support diverse applications, and image-based laser sensors.
Recommended Items
Product Lineup : Distance Detection Based Sensors
The LR-X Series is a remarkably small laser sensor capable of detecting targets based on position and is unaffected by color, surface finish, or shape. Impressive durability is achieved with its food-grade stainles steel housing (SUS316L), high IP ratings, and guarded cable. Position changes as small as 0.5 mm (0.02 inch) are possible, along with automatic and real-time intensity adjustment to ensure stable detection on any target.
Features
Compact & Robust Design for Use Anywhere
Whether building a new machine or retrofitting an older one, the ultra-compact size of the LR-X Series makes it easy to integrate into any space. The metal housing and rugged design also ensure it will last in any environment.
Stable Detection of Any Target
Minimum Detectable Position Change: 0.5 mm 0.02"
The LR-X Series detects targets based on position, not light intensity. This allows for stable detection of targets regardless of color, surface finish, or shape. This allows the LR-X Series to be used in a wide variety of applications, including those with small position changes.
Shiny Metals
Rounded Surfaces
Black/Dark Targets
Varied Colors
Angled Targets
The LR-Z Series is capable of detecting objects based on position or contrast, allowing it to reliably detect metal targets, dark targets, transparent targets, contrast changes, etc. The series is housed in a rugged metal body and offers a simple one button teach. It has a range of up to 500mm (19.69") and offers hard wired, M8 connector, and M12 connector cable options.
Features
Best Detection Ability in its Class
The LR-Z's unique U.C.D. Function allows for stable detection of clear, metallic, or dark targets. This series can also detect purely based on distance, regardless of shape, color, or surface finish.
Durable & Long Life
The IP68/69K rating means the LR-Z is ready for the roughest of factory environments. Wash-down, oil spray, and many corrosives are no match for the stainless steel body. Additionally, physical impact or even overtightening are not a concern because of the highly durable design.
Simplified Operation
Simple setup and easy operation are at the core of the LR-Z's design. With a simple 1-touch teach, calibrating this sensor is straightforward and quick. A highly visible indicator and a 7-segment display make this sensor very easy to use.
New feature U.C.D. Function Distinguishing a Target From a Background Using the Distance and Received Light
The sensor first registers the distance to the background and the received light, which are used as reference, and then detects the target by sensing that the distance or received light differs from the registered reference when a target comes into the detection area. With the background, stable detection of target is ensured even if the target is a complex shaped object, has changes in color and surface condition, or is a thin object with a small height difference.
Without Target
With Target
-
1Difference in distance
-
2Difference in received light
The LR-T Series detects objects based on position and offers extended range to allow for flexible mounting. It is housed in a rugged metal housing, has a simple one button teach and is unaffected by color, surface finish or angle. This series has a range of up to 5m (16.4') and offers hard wired and M12 connector cable options.
Features
Superior Detection Capabilities
The LR-T is designed to detect at long ranges while remaining highly stable. This is achieved due to the HS2 technology used, a combination of Time of Flight detection and a custom integrated circuit. Additionally, the interference prevention and Datum Function allow users to maximize this sensors capability in any situation.
Easy to Use
The LR-T Series is simple to install and calibrate. Flexible mounting options, a visible beam spot, push button teach, and an easy to read display allow for quick setup. Even at long distances, constant feedback is provided with the LR-T's highly visible status indicator.
Features
Stable Detection
CMOS technology allows for stable detection and a high speed response. Now, targets that vary in color, surface finish, or angle are detected without issues.
World's First Datum Algorithm
With this Datum Algorithm, the GV Series can differentiate anything other than the referenced surface.
Product Lineup : Received Light Based Laser Sensors
The LV-N Series features long range with a visible beam spot. The laser head lineup includes both spot and area types along with reflective, retro-reflective, and thrubeam models. The amplifier offers simple setup, straightforward operation, and easy to understand display. Network compatibility is also available with the LV-N Series.
Features
Long Range and Visible Beam Spot
LV-N models feature a visible beam spot and sensor options powerful enough to blast up to 26ft. These features offer increased mounting and detection flexibility all while being as safe as a photoeye.
Simplified 1-Touch Teach
Complete set up with just one click. This feature sets the bar when it comes to quick set up.
The LV-S Series features compact sensor heads and low profile amplifier.
The LV Series offers a selection of thrubeam, retro-reflective, and reflective laser sensors.
Discontinued Series
Product Lineup : Laser Displacement Sensors
IX Series image-based laser sensors can measure height anywhere within the area. Camera-based image recognition allows the laser to detect the height of the target point even when workpieces are not perfectly aligned on the production line. The height of where the laser hits the target will vary if the target is tilted or if the target itself is different, but the IX Series can identify the difference in height against the reference. For example, in a parts assembly line, a single IX Series unit can not only check for the presence of parts but also perform seating checks and other height-based inspections. Thanks to its ability to detect height differences, the IX Series is also free from false detections and errors in the presence of glare from glossy surfaces of metal parts or when the detection target point has the same color as the background, offering stable automatic inline differentiation.
Features
Unreliable Detection with Conventional Image-Sensors, but Stable Detection with the IX-H
Conventional Image-Sensors
Low contrast targets result in difficult detection
For targets with similar colors or materials, the difference between light and dark is not always clear, which can result in unstable detection.
IX-H
Target contrast does not matter
Height-based detection ensures stable results even when there is low contrast between the target and background.
Unreliable Detection with Conventional Laser-Sensors, but Stable Detection with the IX-H
Conventional Laser-Sensors
Variations in position and orientation results in incorrect detection
Variations in target position and orientation can cause the spot where the laser hits the target to change, resulting in incorrect detection.
IX-H
Position Adjustment tool tracks misaligned targets
The camera follows the position, orientation, and placement of the target, making it possible to identify the target location for every target.
IL Series CMOS multi-function analog laser sensors are reflective laser displacement sensors that provide the best-in-class detection ability and stability at a reasonable cost. Stable detection is possible without tuning for workpiece types or their surface conditions, so the IL Series can be added to production lines to help make setup, changeover, and product changes easier. With a wide-ranging lineup of sensor heads, including high-accuracy models and long-range (up to 3.5 m 11.5') models, these laser sensors can be applied to diverse applications thanks to their broad dynamic range and environmental resistance. 1 μm repeatability allows for use in high-tolerance detection setups that previous sensors could not stably provide.
Rugged, Reliable, Repeatable Laser Measurement Simplified. KEYENCE brings you an economical analog laser sensor
A laser sensor uses a “laser” to emit light in a straight line. Its visible beam spot makes alignment and positioning very easy. Since the light beam is focused, the sensor can be installed without worries about stray light. The major types of laser sensors include reflective, thrubeam, and retro-reflective.
Principles and major types of laser sensors
Laser sensors are largely divided into multi-purpose types and distance-setting types. Multi-purpose types are further divided into reflective, thrubeam, and retro-reflective models. All of these models use a visible laser beam but their detection principles are different. This section describes these models and their detection principles with illustrations.
Multi-purpose laser sensor
Reflective laser sensor:
The sensor head contains both a laser light emitting element and a light receiving element, so it is also called a transmitter/receiver. To detect targets, the sensor emits a laser beam to make it reflect from the surface of the target, and receives the reflected beam to detect the target.
A: Transmitter/receiver (sensor head), B: Light emitting element, C: Target, D: Reflected light, E: Light receiving element
Thrubeam laser sensor:
The laser’s optical axis forms a signal beam between a transmitter containing a laser light emitting element and a receiver containing a light receiving element. The sensor detects targets by sensing whether the laser signal beam emitted from the transmitter is interrupted by the target or not.
A: Transmitter, B: Light emitting element, C: Signal beam, D: Target, E: Signal beam interrupted, F: Receiver, G: Light receiving element
Retro-reflective laser sensor:
A signal beam is formed between a transmitter/receiver (sensor head) and a reflector. When the signal beam is interrupted by a target, the light receiving element receives the light reflected by the surface of the target and detects the target.
A: Transmitter/receiver (sensor head), B: Light emitting element, C: Target, D: Reflector, E: Signal beam interrupted, F: Light receiving element
Distance-setting type laser sensor
This type of laser sensor contains a laser light emitting element, a receiver lens, and a light receiving element (CMOS) in the sensor head. The sensor emits a laser beam to a target and receives the reflected light. Based on the change in the position where the light is received (light entry angle), the sensor can detect the change in the distance to the target (height or position of the target). When using this principle, the path of the laser beam from the light source to the point of reflection on the target surface to the light receiving element forms a triangle. Consequently, it is called the triangulation principle (method).
Left: Target is near, Right: Target is far
A: Laser light emitting element, B: Target surface, C: Reflected light, D: Light receiving element (CMOS)
Benefits of Laser Sensors
Unlike light from LEDs or other light sources, the light beam of a laser sensor is visible and travels in a straight line, so the position of the beam spot can be found immediately. Since the mounting position can be determined easily, the time needed for integration or changeover can be reduced greatly when compared with photoelectric sensors.
Unlike light from LEDs or other light sources, the laser beam emitted from a laser light emitting element travels in a straight line. Since the light is visible, the beam spot is easily identified. With a reflective laser sensor, it is possible to visualize whether or not the beam spot is exactly in the desired position. With a thrubeam laser sensor, installation can be done quickly and accurately because it is easy to align the optical axis and determine the detection position. This brings advantages such as reduced installation work and more precise installation.
The laser beam used for laser sensors not only travels in a straight line and has high power, but also does not spread over long distances. The sensor can maintain a small beam spot even for long distance detection, which can help meet various installation conditions.
Laser sensors emit powerful light that does not spread, even over long distances. This means detection is possible far from the sensor head. For example, even when the sensor needs to be mounted at a distance (robotic cells, operator interference, high temperatures, chemical splashing, etc.) the small beam spot allows for detection as desired. KEYENCE also provides a wide variety of sensor heads that can be used under various installation conditions, including types offering variable beam spot sizes and those specialized for long-distance detection.
By using a light beam from a laser light source that travels straighter than LEDs, laser sensors generate hardly any stray light. They have the advantage of fewer false detections even when installed in narrow spaces inside machines or equipment.
Sensors using LED light sources are susceptible to interference from stray light. When these sensors are installed in narrow spaces inside equipment, false detections may be caused by unexpected reflection. Laser beams do not generate stray light even in narrow spaces. They travel in straight lines to allow detection with small beam spots. It is also possible to install reflective laser sensors in spaces inside equipment to detect targets or to use thrubeam laser sensors to detect and monitor gaps themselves. KEYENCE offers a lineup that includes compact sensor heads that can be chosen based on installation conditions.
Laser Sensor Case Studies
Detecting remaining roll of transparent film
The remaining amount of film is detected with a laser beam applied to the side of the roll of film. For roll machines and automatic packaging machines, this ensures proper timing to feed the film (base material) and prevents problems. KEYENCE’s laser sensor (LR-ZH) has the U.C.D. (Universal Change Detection) function that can detect the remaining amount of transparent film. If there is no background, the roll can be detected in combination with a reflector.
Long-distance detection for web tension control
Introducing a position based laser sensor (laser displacement sensor) allows for consistent loop control during transfer of a sheet or web. KEYENCE offers a lineup of ultra-long range laser displacement sensors that can perform accurate detection even from distances up to 3500 mm (137.80"). This range offers flexible installation and ensures stable detection while staying out of harm's way.
Using an image-based laser sensor to detect the heights of parts and materials
The IX Series image-based laser sensor can simultaneously detect height at multiple points along with the presence of parts and materials, without being affected by position deviation of a target. The sensor can detect up to 16 points within the field of view of 108.5 × 81 mm (4.27" × 3.19"). In addition to presence detection of multiple bolts on automotive parts, incorrect bolt height can also be checked simultaneously thanks to height differentiation using a laser. The camera can store the characteristics of the target. Even when the target is placed differently, the position is corrected within the image and accurate points can be detected. Since the detection is based on the difference between the reference height and the height of the target point, both tilting of the target and incorrect part heights can be detected. This is even possible when the target parts have the same color, such as body frames and vibration-damping material.
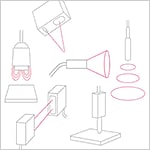
The Sensor Basics website describes a variety of sensors that are useful in factories based on their principles. It introduces everything from basic knowledge such as types and mechanisms to troubleshooting and application examples.
Frequently Asked Questions About Laser Sensors
If ambient light, such as pulse-lighting inverter light or light from a fluorescent lamp, enters the receiver of a laser sensor, the sensor may incorrectly recognize it as reflection of the light it emitted. To prevent this problem, install a shield between the sensor’s receiver and the ambient light source so that the sensor does not receive the ambient light. Alternatively, adjust the angle of the receiver so that it does not receive the ambient light. Also provide as much distance between the ambient light source and receiver as possible. In some cases, using a direct-current lighting light source may reduce the chance of sensor malfunctions.
Transparent objects have high transmission ratios. It is not uncommon to see presence detection of transparent objects fail due to insufficient difference in the received light intensity. Sometimes a slight change in the received light intensity, such as the position of the reflector, can have a negative effect on detection. To solve this problem, mount the sensor so that the optical axis is angled toward the entry direction of the transparent object instead of perpendicular to the entry direction. This makes the shaded area larger and the receiver less likely to receive specular reflection from the target. This should result in a sufficient difference in received light intensity to detect the presence of the target. When using a retro-reflective model, selecting a model with a large spot size can reduce the variation in the amount of reflected light caused by the reflector position. If the detection requires identifying a subtle difference in light intensity, using a separate amplifier model to visualize the received light intensity will make it easier to determine the best settings on site. It can also help to use an amplifier that is capable of automatic correction of setting values.
Mirrored targets tend to cause specular reflection of light. When the tilt of the target changes, the laser beam traveling in a straight line may not return properly to the receiver, resulting in insufficient received light intensity. As a countermeasure, when using a reflective or distance-setting type laser sensor, intentionally detect the target in a slightly tilted position. Alternatively, if there is some part on the target other than the mirrored surface, aim the sensor at that part to make detection easier. If detection fails with a reflective or distance-setting model, use a thrubeam or retro-reflective laser sensor which is less affected by surface conditions. Selecting a model with a light beam that "spreads," such as a fiberoptic sensor, can reduce the variation in the received light intensity when a mirrored target is tilted.
![LASER SOLUTIONS [AUTOMOTIVE EDITION]](/img/asset/AS_65632_L.jpg)
This guide introduces applications using reflective and thrubeam laser sensors in various processes in the automotive industry. It also has easy-to-understand description of the characteristics, technologies, and advantages of various laser sensors.