Taiyo Wire Cloth Co., Ltd.
RK helped us to easily automate routine tasks that led to reduced work hours and decreased errors!
At Taiyo Wire Cloth Co., Ltd., they sought ways to improve operations while leveraging existing software assets, ultimately deciding to introduce the RPA (Robotic Process Automation) tool, RK. By automating multiple tasks, they were able to shorten work hours and minimize errors. To gain in-depth insights into the utilization and evaluation of RK, we spoke with three individuals involved in the introduction and operation of the software for process improvement from the Materials, Operations, and General Affairs Departments.
Taiyo Wire Cloth Co., Ltd.
Taiyo Wire Cloth Co., Ltd. is a long-established fabless manufacturer that has been in business for 78 years, with nine locations in Japan and four overseas. They develop, manufacture, and sell EMI shielding, heat resistant, and industrial wire mesh products for various industries such as automotive, medical, and communications.
- Established: November 1945
- Capital: 90 million yen
- Number of employees: 190 people
Automate various routine tasks using RK
Please tell us how you are using RK.
“In our company, we utilize RK in three departments: Materials, Operations, and Quality Assurance. Among them, the Materials department employs RK most frequently, using it primarily for generating Excel files for inventory and delivery date management.
Specifically, we access our sales management system to export data such as orders, receipts, purchases, and sales as CSV files. RK then extracts the necessary data from the CSV files, processes it, and uploads it to the groupware "Garoon" with comments.
Considering the varied approaches to management for equipment and mass-produced parts, we created approximately 20 scenarios (automation programs) for Excel generation.
Before RK was introduced, each employee spent about 1.5 hours manually creating Excel files after arriving at work. Now, by running RK at night, I can have the Excel files ready when I get to work, which saves me a lot of time.
In addition, we use RK to automate routine tasks, such as inputting shipping information into our sales management system.
Currently, we are also working on creating new scenarios based on field interviews and requests, responding to the needs and demands directly from the field.”
Improving operations while leveraging existing software assets
Why did your company explore RPA and how did you decide on Keyence’s RK?
“Until a few years ago, when considering business efficiency within our company, our focus was mainly on "system modifications." However, it was realized that even with the currently implemented software, there were aspects that we had not fully mastered and features that had not been utilized at all. It was suggested that by effectively utilizing these aspects, we could enhance operational efficiency without the need for system modifications.
As a result, we established the "Information Utilization Committee" to explore ways to improve efficiency while utilizing existing assets.
During the committee's exploration of operational improvements, one employee shared a story about automating tasks using a free RPA (Robotic Process Automation) software, introducing us to the existence of such tools.
After researching and comparing various RPA software from different manufacturers, we decided on Keyence's RK for the following reasons.”
<Reasons for Adoption>
- Anyone can easily create automation scenarios using the drag-and-drop interface.
- We can get full product support at no extra charge.
- There are no initial costs.
- The price is attractive and monthly payments make it easy to get started.
Since some employees were already using free RPA, what made you decide to use paid RK?
“The free RPA had limited functionality and in order to do what we wanted we would have to switch to the paid version. Given that, I thought it would be better to use RK, which seemed easy to use and included full support.”
Shortening work hours and reducing mistakes
How has RK impacted your business?
“We were able to significantly shorten work hours and reduce careless mistakes.”
● Reduction in work hours
“For example, the employee in charge spent nearly an hour every day creating Excel files for inventory management and delivery management reports. There are about 20 files, so just considering this scenario alone has led to a reduction of about 30 hours per month. The good thing about this is that you can use the time saved to work on other tasks, and since we can run RK overnight, you can start working as soon as you get to the office.”
● Reduction in careless mistakes
“Another major benefit is that RK accurately inputs information that was previously entered manually, eliminating possible mistakes. Because of this, we no longer have to redo things or worry about order errors, and we can spend less time checking that there are no mistakes in the files we create.
Additionally, as people are seeing how much we’ve been able to automate across departments, we’re starting to get more and more requests from the field asking about ways to automate their processes too.
When we first introduced RK, there were some employees who didn’t really welcome the idea of improving work efficiency, so this is also a big change.”
The term “work efficiency improvement” may be viewed negatively by people in the field.
What were the reasons for not welcoming improvements in business efficiency?
“The term “efficiency improvement” has connotations that can be perceived negatively. Some people may feel worried that they could lose their job, or that they are being told that their work is a waste of time.”
What measures did you take to alleviate this perception?
“I paid particular attention to the way I communicated the message. Instead of repeating the words “improving work efficiency” too often, we had a dialogue about their automation needs and asked questions such as “If this aspect of the workflow is eliminated, would your work become more efficient?”. That’s what I did. Additionally, once automation was implemented, the company repeatedly communicated that there are tasks that require human thought and input, and that the company wants to focus time on these tasks.
We also used a large monitor to show RK in action as a “demo.” When people actually see it in operation, they seem to think it’s not a bad thing. Thanks to this initiative, the impression of RK has improved considerably.”
Creating automations with ease
Now that you’ve used RK, what do you like most about it?
“The best thing about it is how easy it is to use. I especially like the fact that everything on the screen is written very clearly and straightforward. The menu categories, such as “Excel” → “Cell operation”, are well-organized, so you can create scenarios without any confusion. Even when using image recognition to select the appropriate button, the results are very accurate and give us confidence there will be no issues. Our sales management system has some quirks, and the accuracy of image recognition was really helpful, especially since on-screen coordinates couldn't be used to determine positions of where to click.”
How was the initial implementation of the software? Were you able to use it pretty quickly?
“Yes. After the first few training and support sessions, I was able to use it without any problems, and I haven’t had many questions since then.”
When asked about any difficulties, “it was actually quite simple, so much so that I’m a little at a loss for an answer. If you have even just a little programming experience, you should be able to use it within the same day.”
Do you have any tips for using the software effectively?
“The trick is to create an environment that makes it easy for RK developers to do their work. Instead of just loosely discussing ideas for automation, there needs to be a concrete workflow and a breakdown of the tasks and details that need to be automated. It’s much easier to produce good results if you explain the process step-by-step.
If you run into any issues with the automation not working properly, you need to also consider your own systems as a potential source of the problem. For example, with our sales management system, the login screen did not appear immediately upon startup, so there were times when RK operations were too fast and we were unable to log in successfully. In that case, I solved the problem by creating a scenario where I intentionally caused the login to fail and then tried logging in again. One trick is to create a scenario that can effectively absorb problems like this, even if they occur in areas other than RK.”
Outlook on future automation
Please tell us about your future business automation plans.
“RK has been a great tool for helping us to accomplish improvements in business efficiency. However, there is still a lot of room for improvement, and we are continuously getting new ideas from everyone on what they would like to automate. We also only have a limited number of people that can use the software currently, so the plan is to get a few others trained on it. Since our company has several other locations, the eventual goal would be to have them adopt this platform as well.”
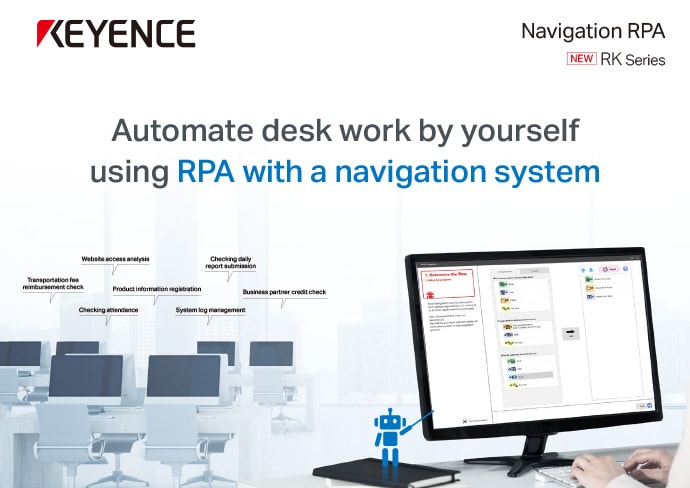
Navigation RPA RK Series
View Catalog