Tokai Kikai Co., Ltd.
Saved over 33 hours a month with just a single software license
Tokai Kikai Co., Ltd. has incorporated RPA (business automation) tools as part of their Digital Transformation project and within a year, they’ve been able to automate 23 different processes. We spoke with stakeholders in Sales and Operations departments that were involved in the introduction, development, and implementation of RK to understand the impact of robotic process automation on their business.
Tokai Kikai Co., Ltd.
Tokai Kikai Co., Ltd. is a well-established machinery manufacturer that has been in operation for 75 years. Apart from possessing an integrated production system covering design, metalworking, welding, machining, and assembly, the company stands out for its factories in China and Thailand, enabling the realization of quality assurance, cost reduction, and on-time delivery. This distinctive feature allows the company to cater to a wide range of fields, from large-scale machinery like tunneling shields measuring nearly 15 meters in length to the precision assembly of intricate components such as smartphone chip mounters. As a result, Tokai Kikai has earned high praise from numerous customers.
- Established: April 1952
- Capital: 50 million yen
- Number of employees: 109 people
Automated 23 tasks in about 1 year after implementation
Could you tell us about how you are using RK?
Introduced a little over a year ago, Tokai Kikai has created 23 automation programs. Here is a summary of some of the tasks that are now managed by the software.
1. Data transfer and consolidation
“We use RK to consolidate data on each of our products into Excel. This data is then provided to customers once we deliver a product to them.
First, we download data for each product from the core system. Serial numbers and other relevant items are extracted from nearly 500 data points that are registered in 8 Excel files and then compiled into one Excel file. This was performed twice a week, with up to 15 products at a time. It used to take about 90 minutes each time, but by automating it before the start of the workday, we were able to reduce this to virtually zero. We’ve also had no issues in the 10 months since this operation started.”
2. Creating a list of late delivery dates
“We have improved our workflow by using RK to visually check 20 to 30 purchase orders daily for delivery delays. By reading and consolidating data from the purchase orders into a single spreadsheet, the confirmation process that used to take around 20 minutes per day is now completed almost instantly with RK."
3. Invoice entry
“We have also automated the process of entering invoices. Previously, data had to be manually entered in two places: Excel and a database. By using RK, we can automatically transfer the contents of the invoice to the database. What used to be done twice now only needs to be done once, reducing the work from nearly 20 minutes a day to less than 10 minutes, and eliminating errors caused by manual input.
We also use RK to process Excel files that are used monthly at our manufacturing sites, and for updating production planning tables daily. We’ve been able to find a lot of use for it across several departments, including manufacturing, accounting, and general affairs.
Our group is just using one creator license, so we typically run the automations at the beginning of the day, which will then free up the license to be used by our developers later in the day if needed.”
Digital transformation (DX) directive
Please tell us how you introduced RK.
“Since 2022, our company has been working to reduce the number of tasks that only a handful of employees know how to do while also trying to digitalize as many of them as we can. A recent example is that we started using tablet devices to go paperless. One of the issues that came up during our discussions was about improving the efficiency of time-consuming, routine tasks. In particular, we used to print nearly 1,200 pages per week for the product data we would send to customers. We’ve since gone paperless for this, but the work of compiling the data into Excel is still done manually, which requires a considerable amount of time and effort. I was hoping there was an easier way and came across some info from Keyence introducing RK.
We scheduled a virtual demo and talked to them about it, and they told us that it was a relatively reasonable monthly subscription fee to get started. It also included free service and support, so we thought we’d give it a shot to see how it could help.”
Increasing product adoption within the company
You mentioned that there were four people that could create automations with RK. What were the steps you took to get more people to use the software?
“The first step is to choose people who are likely to benefit the most from these automations, and then provide them with solid support. When we originally launched the software, we rolled it out to everyone we thought could use it and ended up having seven employees attend the first introductory session. However, with everyone’s regular day-to-day workload, it made it difficult for them to also think about and create automation scenarios. In the end, only one out of the seven stayed with it.
As you can imagine, that wasn’t exactly what we were hoping for, so the second time I selected someone from a department that does a lot of computer work and who I thought would be a great member to have in this group. What I’ve found to be helpful is to run through actual automation scenarios that I’ve created with other team members to see if that helps them to visualize any situations in which they could use something similar. If so, I’ll take them through some basic workflows for creating a program to help them get started. As with anything, as they start to use it, they realize how simple it is and are able to create their own programs. Once they see how helpful the software is, they can more easily think of other processes that should be automated, even to the point of reaching out to other departments that they interact with and teaching them how to create scenarios as well.”
Saving time and increasing value
Please tell us about the effects of introducing RK.
“Since we started using RK, I’d say we’re saving around 33 hours per month. However, the benefit is not just with the work that’s been reduced. The extra time we have can now be spent focusing on other tasks, effectively doubling the impact we’re seeing. We’re only scratching the surface of what we’re able to automate at the moment, so I’m sure we’ll see a bigger ROI once we’re able to develop additional automation scenarios.”
How else has RK improved your business?
Besides saving time, RK has helped Tokai Kikai realize other benefits, including:
● Elimination of human errors
“When it comes to numbers and data, if you have to enter them manually, there are bound to be some mistakes. By automating the work using RK, these potential input errors have been completely eliminated.”
● Streamlining of business processes
“For example, the confirmation of delivery dates was originally done using handwritten purchase orders. However, in order to automate it with RK, we needed these in a digital format, so all purchase orders were converted to Excel. In this way, some operations were forced to change, and we are now able to work more efficiently.”
● Support during staff shortages
“When employees are unavailable or out on vacation, this used to cause delays in our operations. Now, we can create automations that can handle some of the work and processes when people are out of the office, allowing us to continue uninterrupted.”
Recommendations
What kind of companies and departments would you recommend RK to?
“I would definitely suggest RK to departments that input, transfer, or compile data. In fact, we’ve recommended RK to some of the manufacturers we have relationships with and have even shown them a few of the scenarios we’ve created. Maybe Keyence can expect to get an order from some of them in the future…”
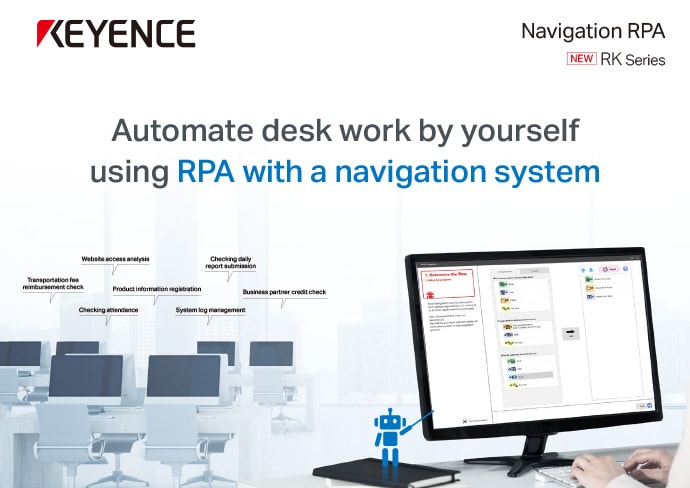
Navigation RPA RK Series
View Catalog