Making Work Efficient
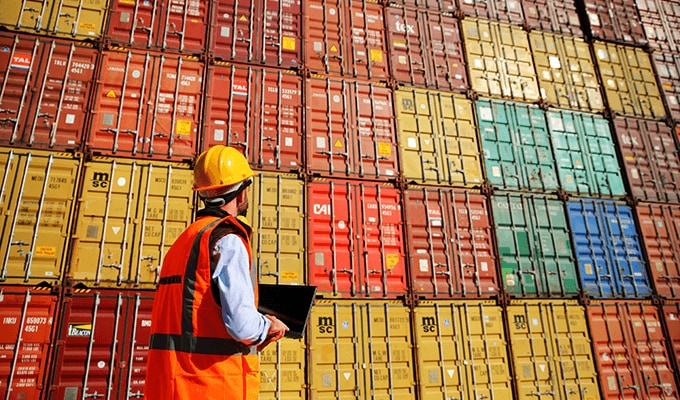
To solve the issues in logistics worksites, the flow of goods, flow of work, and flow of information at the worksite must be totally optimized, from receiving to shipping. When all work is made more efficient, this is when “Kaizen” can first be achieved. This section explains the points of making work more efficient at logistics worksites from the standpoints of simplifying work, changing the flow of traffic/layout, and automating work using material handling devices.
- Simplifying Work
- Optimizing the Flow of Traffic/Layout
- Automation/Labor Saving Using Handheld Computers
Simplifying Work
To implement “Kaizen” of a logistics worksite by making work more efficient, you basically start by simplifying flows and processes. The speed of work can increase, mistakes can decrease, and the number of workers can be minimized through simplification. However, just making complicated work simple is not making it more efficient. The essence of simplifying work is that the work on which time and labor are wasted is uncovered, the current state reviewed, and the measures for improvements and their effects are analyzed.
For example, duplicate work, such as putting a picked product in a box and moving it to a different box when passing it to the packaging worker, is a typical example of inefficiency. It seems very inefficient when you write about it, but at actual worksites, this kind of work has become normal due to habits over many years, and often times nobody notices this waste. What is important is the simple accumulation of questioning these types of habits, keeping the necessary work, and eliminating the wasted work.
Optimizing the Flow of Traffic/Layout
In manufacturing worksites, in the kitchen, and even in logistics processes, what determines ease-of-use and good efficiency is the flow of traffic and layout of the worksite. It would be idea for each process to be connected as closely as possible, but a flow of traffic or layout design in which forklifts and workers move in the same area would be a problem for safety. However, being too careful of safety and having the loose goods storage area and pallet area too far away from each other would take time to move and replenish goods and not be efficient. It is important to optimize the traffic flow of work and layout while appropriately adjusting these types of mutually exclusive elements.
For example, there are improvement measures that can be adopted immediately such as creating a work-friendly environment for even shorter workers by consolidating products that are frequently shipped on lower shelves. Packing materials that are frequently used being pushed out to the corner of the materials storage space where they cannot be immediately found when needed is also a basic type of waste. This kind of waste in the traffic flow and layout can be resolved simply by moving the packing materials closer to the packaging section. Hints for these kinds of improvements can be found at any worksite, and optimizing the traffic flow and layout from the accumulation of these small improvements is what is important.
Automation/Labor Saving Using Handheld Computers
At logistics worksites, the biggest inefficiency is visual inspection work and checking invoices/delivery statements with actual goods. This work is not only a waste, it also leads to the occurrence of simple mistakes such as oversights and omissions. Using handheld computers for this verification work without relying on humans can make work dramatically more efficient and prevent mistaken shipments and other simple mistakes.
Verification by handheld computer is accurate and fast to a degree that it cannot even be compared to visual inspection, so mistakes in the prescribed work can drastically reduced even when performed by inexperienced staff. When you think of making warehousing work more efficient, effective use of handheld computers is the key.