Storage and Cargo Handling
This section describes transportation and delivery in the logistics functions and the core functions of storage and cargo handling. Storage is a typical term and easy to understand, but cargo handling can be more difficult to imagine because it involves loading and unloading at a warehouse or logistics center, transportation, warehousing management, sorting, and assortment. We need a solid understanding of these functions because they make up a large portion of logistics costs.
- What Is Storage and Cargo Handling?
- What Is the Receiving Inspection?
- What Is Material Handling?
- What Is Taking Inventory?
- What Is Picking?
- Sorting
- What Is the Shipping Inspection?
What Is Storage and Cargo Handling?
This section describes the meaning, differences, and roles of storage and cargo handling.
Storage Is Necessary to Fill the Temporal Gap and Steadily Supply Goods to the Market
Storage is the activity of storing products at warehouses and logistics centers. Its role is to provide a steady supply of goods to the market to fill the temporal gap between producers and consumers. It also plays an important role in maintaining quality at warehouses and logistics centers and value of products. For example, the storage function for fresh fish, vegetables, and fruits has dramatically improved with the advent of freezer and refrigerated warehouses. Important logistics centers in storage include: distribution centers (DC), transfer centers (TC), and process distribution centers (PDC).
Cargo Handling Refers to the Overall Transportation Activities in Warehouses and Logistics Centers
Cargo handling refers to the overall activities in warehouses and logistics centers, such as loading and unloading cargo, transporting cargo, warehousing, picking, and sorting. The main work in cargo handling is separated into six tasks: assortment, stacking/taking inventory, transportation, storage (allocation), sorting, and picking. These tasks greatly effect productivity and quality in logistics. Cargo handling is a very important part of logistics, and losses in cargo handling directly increase logistics costs. Cargo handling involves many different tasks, so next we will explain in detail the most common.
What Is the Receiving Inspection?
Retailers typically purchase products to sell and sell those products to the end user. In manufacturing, the necessary raw materials and parts are purchased and shipped as products. In logistics as well, cargo is accepted, inspected, stored, and shipped to markets each day.
- Cargo is received.
- Received cargo is inspected.
- Goods are warehoused.
- Goods are stored and distribution processing and packaging is performed.
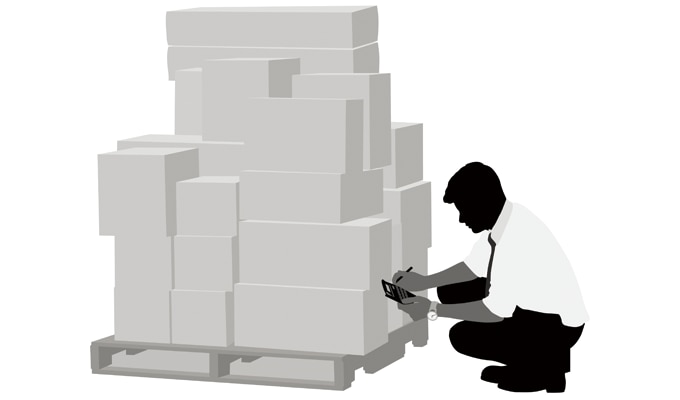
First, received cargo is verified against the receiving cargo list and the products, quantities, and quality are inspected. The inspection may also involve an acceptance inspection, and if there is no problem with the received cargo, the goods are entered into warehouse. Later, the goods are stored and distribution processing and packaging is performed as necessary. Warehousing and inspection data management can be recorded on paper in a ledger if the volume is low, but generally this is performed with handheld computers in warehouses and logistics centers that receive a large volume of cargo. Inventory management can be performed on cargo from storage to shipping based on the data obtained using a handheld computer when the cargo was received and inspected. This flow that took time to record on paper can now be performed smoothly and accurately.
What Is Material Handling?
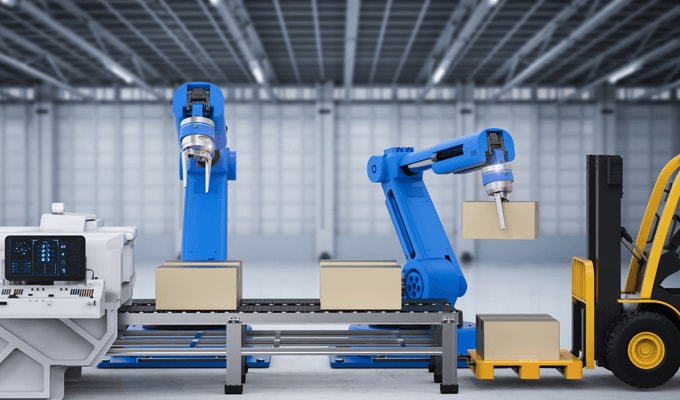
Material handling is a general term for the machines that make cargo handling work (e.g., assortment, loading and unloading, transportation, and sorting) more efficiently. More simply, it refers to the machines in general that make it easy to move cargo around or automate handling. This includes simple machines such as carts, pallets, forklifts, and conveyors, as well as industrial robots and automated warehouses that reduce labor requirements and loading times. Material handling also includes automated picking machines, product management machines using RFID tags, and machines that perform automated conveyance and sorting as examples of machines that have been increasing in recent years.
What Is Taking Inventory?
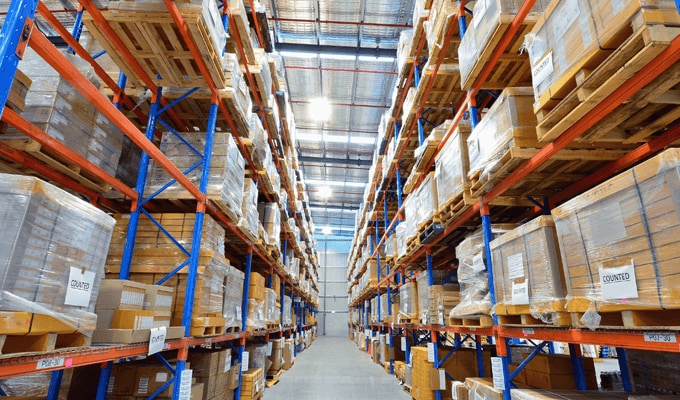
Taking inventory is a task in which the numbers, types, and quality of all items in inventory are checked. Many people imagine inventory being taken by even small retail stores before closing the accounts. The number of products remaining in inventory is counted and the value of inventory is checked so that the amount of profit can be understood accurately, which is useful for making business decisions. Taking inventory is important in inventory and business management. However, it can be difficult in a large-scale facility such as a warehouse or logistics center due to the massive amounts of labor, time, and costs because all goods must be checked. All operations or a portion of operations must also be stopped during the period in which inventory is taken. However, if warehousing management is performed accurately in daily work, the burden of taking inventory can be greatly reduced by adding up that data. Inventory management can be performed in real-time to help make speedy business decisions.
What Is Picking?
-
Work in which orders are received for products in inventory or storage (distribution center work)
Single Picking Method -
Work in which the various products received that day are sorted for specific delivery destinations (transfer center work)
Total Picking Method
Picking is work to gather products to ship while checking the item numbers and quantities of those products written on a shipping instruction form (picking list). There are two picking methods: the single picking method in which products are collected individually for each shipping destination and the total picking method in which products collected in advance are sorted by shipping destination.
The single picking method is the most typical method in which the products written on the shipping instruction form (picking list) are searched for and then shipped. This is also called order picking, and it is used to send a wide variety of products to many shipping destinations. This picking method is suitable to mail order and other businesses because it is very flexible and products can be shipped immediately after they are picked. However, it takes time and effort for workers to look for products in the warehouse.
The total picking method is also called assort method. This method is optimal for shipping a large amount of a few types of products to a small number of destinations. Products are collected in bulk so the burden on workers can be lessened, but space is required to sort the products. Disadvantages to this method are that it is difficult to know the status of sorting products and handle sudden additions of products.
Picking Systems
This section gives a simple introduction to picking systems. The simplest picking method is to have a person look at the shipping instruction form (picking list) and search for the products. However, there is a high chance of worker-caused mistakes occurring and the method takes time and effort. At present, many different picking systems are used according to the purpose and products.
- List Picking
- The most basic picking method in which a person looks at the shipping instruction form (picking list), checks the product names and quantities, and searches for the products. This method is easy to implement, but it depends on the accuracy and speed of the worker, and the chance of worker-caused mistakes also increases. To prevent mistakes, checks are required, such as inspecting products with barcodes, before the products are shipped.
- Digital Picking System (DPS)
- In this picking method, digital displays are attached to racks that store cargo and products, and the products are collected according to the instructions on the displays. A advantage of this system is that workers can perform the work easily without any experience because they simply pick the products while looking at the indicators and worker-caused mistakes are kept to a minimum. This system is also desirable because it can be easily adopted and displays can be attached to any storage location.
- Barcodes
- In this method, picking is performed by turning shipping instruction information into barcodes and reading the barcodes of products. If the wrong product is selected, the barcode scanner or handheld computer emits an error sound or vibrates to prevent the wrong product from being picked.
- RFID Tags
- Attach RFID (radio frequency identifier) tags, with which information can be exchanged over the wireless network, to product racks to prevent the wrong product from being picked. The advantage is that nothing needs to be read like a barcode, which makes this effective for implementing speedy work.
Sorting
Just like picking, sorting is a central part of shipping work Sorting is work to separate products by type or shipping destination. There are two broad categorizes of sorting methods: manual sorting and automated sorting. The difference is whether workers perform the sorting or machines. A machine called a sorter is mainly used for automated sorting. Sorting is broadly classified into three types depending on how cargo is brought into the sorting area.
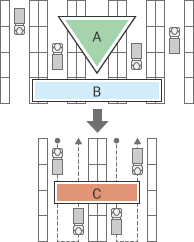
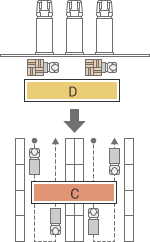
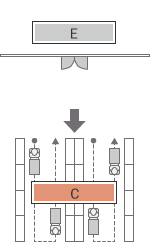
- A. Inventory
- B. Total picking
- C. Sorting
- D. Receiving inspection
- E. Manufacturing
- Inventory Type (Distribution Center)
- The logistics center holds inventory and cargo picked from the inventory is sorted.
- Click for Distribution Centers
- Pass-Through Type (Transfer Center)
- The logistics center holds no inventory and sorts received products.
- Click for Transfer Centers
- Distribution Processing and Inventory Type (Processing Distribution Center)
- Products manufactured in a factory are brought in as-is and sorted.
- Click for Processing Distribution Centers
What Is the Shipping Inspection?
The same as the receiving inspection, the contents of the shipment are inspected for mistakes when shipped. This is called the shipping inspection.
- Create a shipping instruction form (picking list) for the contents of the order.
- Pick the products according to the shipping instruction form (picking list).
- Perform distribution processing.
- Inspect.
- Package.
- Ship.
In shipping, create a shipping instruction form (picking list) for the contents of the order, and the worker picks the products according to the shipping instruction form (picking list). After the products are picked, distribution processing is performed as required, a shipping inspection is performed to determine if there are any problems with the products before they are packaged, and then the products are packaged and shipped. Data is recorded during picking and the shipping inspection in the same manner as during receiving. If products are managed using a handheld computer by giving them a barcode or 2D code when received, warehousing management and inventory management can be performed accurately.