Adhesive Coating
Adhesion is the state in which two surfaces have been bonded by a chemical or physical force, or a combination of both via an adhesive medium. This section explains the mechanisms of adhesion, as well as the types and functions of adhesives.
Mechanisms of adhesion
The mechanisms of adhesion can be divided into the following three major subcategories.
Mechanical bonding
Two surfaces are bonded by an adhesive that cures after filling the holes and asperities on the surfaces. This is called an "anchor effect” (or a “fastener effect”).
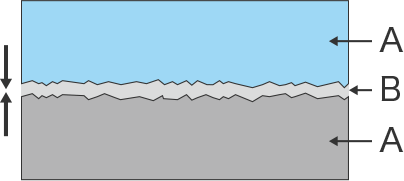
- Target material
- Adhesive
Physical interaction
Physical interaction bonding is the principle of adhesion based on the van der Waals force (intermolecular force), which is the force of attraction between all molecules. This force is also called a “secondary bonding force”.
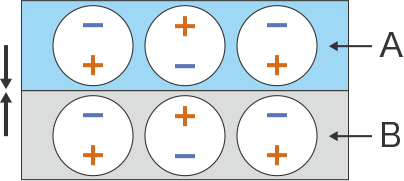
- Target material
- Adhesive
Chemical interaction
The chemical interaction between the target material and the adhesive causes a chemical bond between atoms, resulting in a relatively strong adhesion. This is also called a "primary bonding force," and includes covalent and hydrogen bonding.
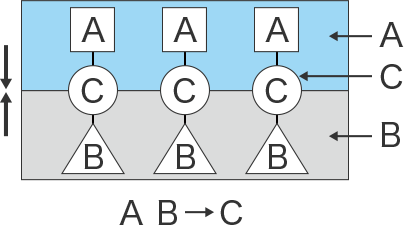
- Target material
- Adhesive
- Chemical bond
These classifications above are for example purposes only. There are many ways to classify the types of adhesion, and some may differ from the descriptions above.
Types and functions of adhesives
Classification of adhesives
Adhesion by coating is a process of bonding objects using an adhesive that wets a target and then solidifies. There are various types of adhesives, including liquid and solid types. The solid adhesives must be melted by heat, and the objects become bonded when the adhesive solidifies. Adhesives can be divided into the following three major types.
- One-component and two-component adhesives (such as urethane or epoxy)
- Classified as liquid adhesives, one-component adhesives cure using moisture in the air or through heat. Two-component adhesives cure when two types of liquid—resin and a hardener—are mixed together. Compared with hot melt adhesives, two-component adhesives generally offer higher adhesion strength.
- Hot melt adhesives
- These solid adhesives (in blocks or granules) must be melted by heat before use. This type is characterized by a shorter curing time with less conditions. Common materials include polyether, olefin, rubber, EVA, and PA.
- Reactive hot melt adhesives
- Reactive hot melt adhesives are adhesives with heat-resistant properties. The adhesive cures in response to moisture in the surrounding air. These adhesives are characterized by low melting and coating temperatures, and are used for a variety of target types.
These classifications above are for example purposes only. There are many ways to classify the types of adhesion, and some may differ from the descriptions above.
Functional adhesives
While the basic goal of adhesives is to bond objects together, there are "functional adhesives" that offer a variety of bonding properties, such as different curing processes and adhesion speeds. Additional material functions such as specific conductivity, durability, transparency, or elasticity can also be achieved.
Type | Function |
---|---|
Instant curing adhesive | Adhesives that cure quickly (in 5 seconds or less). |
Contact curing adhesive | One surface is coated with agent A, and the other is coated with agent B. Curing starts when agent A comes into contact with agent B. This makes mixing the agents beforehand unnecessary. |
UV curing adhesive | These adhesives are used for bonding light-transmissive materials. The adhesive cures instantaneously when UV (ultraviolet) light is applied. |
Anaerobic curing adhesive | This adhesive is permeated through gaps such as those around screws, and cures in the absence of air (oxygen). |
Property | Function |
---|---|
Transparency | Offers transparency with a refractive index equivalent to that of glass lenses. |
Conductivity | Offers the ability to absorb electromagnetic waves to prevent radio interference. |
Heat resistance | Offers high heat resistance (e.g., alumina, zirconia, or other inorganics). |
Elasticity | Offers an extremely high level of stretchiness. Used for bonding materials with different thermal expansion coefficients or for bonding that requires greater durability. |
Stiffness | Offers high stiffness of the joined section through the use of both "point" bonding with resistive welding and "area" bonding with adhesives (weld bonding). |
In addition to the above, there are also adhesives that offer various other properties and functions such as sealing, insulation, flame retardance, heat conductivity, and foaming.
Expanding applications of adhesives
While adhesives and coating equipment have become more diversified and sophisticated, the applications of adhesive bonding has also been expanding into a wider variety of fields. For structural adhesives in particular, demand is growing for precise adhesive applications such as small-quantity adhesive coating that satisfies thinner design requirements for displays (LCD and organic EL) and smart devices (smartphones, tablets), as well as for stronger bonding of different materials in the quest for lighter weight and higher rigidity in automotive and aerospace industries.
What is a structural adhesive?
In general, a structural adhesive is an adhesive designed for high-strength bonding. Using a coating with these adhesive properties provide "area" bonding, resulting in a lightweight and strong bond. Combining area bonding with "point" bonding, such as spot welding, bolts, or rivets a bond with even higher rigidity can be created. A typical example is "weld bonding", which uses spot welding in the car body assembly process.
Applications of structural adhesives
Structural adhesives have been widely used in the aerospace industry for more than half a century, including for airplanes, helicopters, supersonic jets, the Apollo spacecraft, and space shuttles.
Today, the need for bonding of different materials is growing due to an increased use of composite materials (multi-materials) in car bodies and other products for reducing environmental loads and improving productivity. As a result, structural lightweight and high-strength adhesives have been attracting attention not only in state-of-the art advanced fields such as space development, but also in high-volume production fields such as the automotive industry.
- Applications of structural adhesives for bonding different materials
-
Automobile-related Requirement Bonding of composite materials for reducing weight and increasing rigidity in car bodies Material Aluminum chassis + CFRP interior Bonding method Urethane-based structural adhesive + A small number of bolts Securing various motor magnets (such as FA servo motors) Requirement Bonding of different materials offering high heat resistance and high strength Material Nd (neodymium) magnet + Laminated core Bonding method SGA adhesive (reactive acrylic adhesive) Solar battery panel (for artificial satellites) Requirement Resistance against heat cycle (-150°C to +200°C), resistance to radiation, transparency, etc. Material Solar battery cell + Cover glass Bonding method Silicone adhesive