Automotive Body
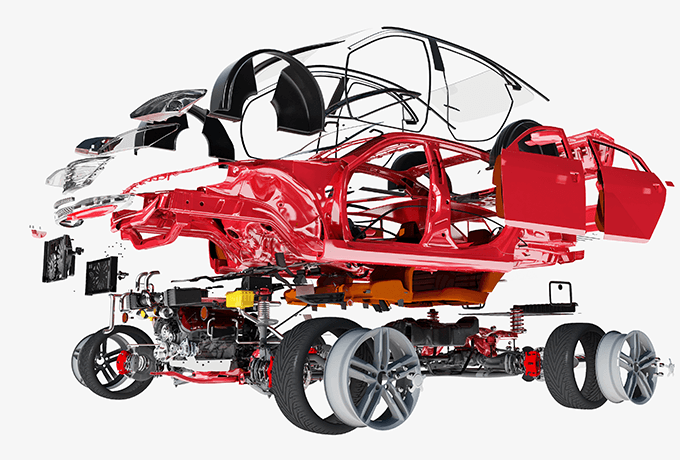
An automobile consists of many different components. While EVs (electric vehicles) and connected cars have become a popular topic of conversation in recent years, reducing the vehicle body weight has been a challenge against the backdrop of demands for reducing environmental loads and improving fuel efficiency. This is also true for automotive components such as secondary batteries, ECUs, and connectors.
As technology for satisfying these needs, coating for adhesion and film-forming has become a popular option in vehicle bod-related processes.
- Adhesion in automotive manufacturing (Body assembly)
- Functionalization and surface processing in automotive manufacturing (Body manufacturing)
Adhesion in automotive manufacturing (Body assembly)
- Structural adhesive (Weld bonding)
- Weld bonding has become a hot topic in the body assembly process. This technology combines spot welding for joining points and structural adhesives (weld bonding) for joining surfaces. This method can reduce the number of bolts and other parts in addition to the number of labor hours required for welding, all while achieving a lightweight and strong bond. Moreover, the reduced number of welding points creates high added value for body manufacturing such as increased-flexibility body designs.
Topic: Multi-material production for body weight reduction
Body weight reduction has become an important issue for addressing environmental regulations and improving fuel efficiency. To achieve this goal, the use of composite materials made of CFRP (Carbon Fiber Reinforced Plastic) joined with aluminum alloy or magnesium alloy has been increasing in Europe and Japan.
Direct joining by friction heat utilizing the thermoplasticity (the property of a material becoming soft when heated) of CFRP has been studied as a way of joining dissimilar materials. Due to the differences in thermal expansion ratios, some challenges yet remain, such as strength retention in a driving environment, and the corrosion resistance of the joined part. The combination of coating with a lightweight, high-strength structural adhesive and the use of bolts is a currently effective joining method.
Topic: Automatic coating of sealant (sealer, primer) during glass pane assembly
When assembling glass panes to car bodies, a dispenser robot is used for automatic coating of sealant (sealer, primer). If the sealant is coated improperly, water and other foreign matter may enter inside and degrade the corrosion resistance of the body.
The bead of sealant must be applied continuously in an appropriate shape (height, width, and volume) along the entire circumference. To prevent the release of defective workpieces, it is necessary to measure the shape of the sealant in real time by tracking the automatic coating.
Functionalization and surface processing in automotive manufacturing (Body manufacturing)
The series of coating processes in automotive body manufacturing includes coating not only for design purposes but also for adding functions to the body surface. The coating layers of typical car body surfaces are as follows:
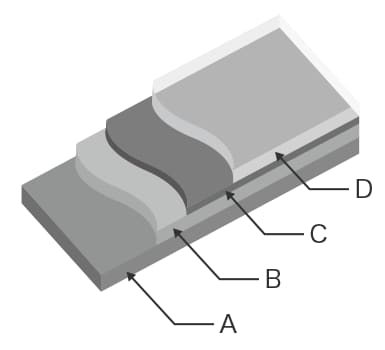
- Electrodeposition layer (A)
- This layer adds a rust prevention function. Dip coating (immersion) is generally used.
- Middle coat (B)
- This layer adds a chipping prevention function. The function prevents exposure of the base steel due to stone impacts or other events.
- Base coat (C)
- This layer adds color for design purposes. Multiple processes may be used depending on the design purpose.
- Clear coat (D)
- The purpose of this layer is to improve durability such as for surface protection and weather resistance.
Other than the deposition layer, car body coating processes use electrostatic painting with painting robots. The sophistication of painting robots has continued to develop, such as with multi-axis structures, the ability to paint in small spaces, and automatic tool changing.
Additional information: Present state of painting robots
Topic: Vibration-damping coating for improving efficiency and functionality
Vibration-damping materials are used on car body floors in order to reduce vibration noises and improve the quietness in the cabin. Conventional typical methods involved manually cutting and pasting a sheet of material. In recent years, however, such methods have been replaced with coating type vibration-damping materials for improved efficiency and functionality.
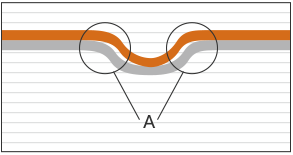
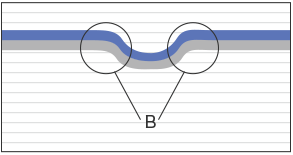
- A. Gaps that degrade performance
- B. Perfect adhesion that improves performance
Using sheet-type material also poses a problem of lower vibration-damping performance due to gaps when the sheet is applied on uneven or rounded surfaces.
On the other hand, coating-type material can be coated automatically at high accuracy using a dispenser robot capable of applying coating even at an angle. Such robots can shorten the process, save labor, and reduce material loss. The adhesion ensures reliable coating of the necessary amount in complete contact with the surface, regardless of whether it is uneven or curved. This results in a lightweight construction with a high vibration-damping effect.
For automatic coating with a dispenser robot, it is important to implement shape inspection immediately after coating by tracking the dispenser nozzle as a precaution for coating defects.
Reference example: Coating Inspection of Automotive Components