Seam welding
Seam welding is a method used for applications requiring high air-tightness and waterproofness. This page introduces the principles and the advantages/disadvantages of the seam welding method, also known as lap seam welding. This page also introduces butt seam welding and mash seam welding, two methods that use similar welding principles.
Weld materials are held from above and below with circular electrodes. A current is passed while the electrodes are rotated, and the heat generated by electrical resistance joins the weld materials continuously. The method is also called lap seam welding.
Making a line of overlapping spot welds ensures leak tightness. This is cost effective because the welding speed is fast and no gas is used. Since sparks are not produced during welding, there are no safety problems and no need for protective equipment.
Practical applications include welding parts or sections requiring leak tightness or waterproofing such as fuel tanks. In addition to lap seam welding, seam welding has variations such as butt seam welding that continues heating butted surfaces by applying pressure and passing a welding current to weld the seam, and mush seam welding that uses roller electrodes to mush up slightly overlapped edges of base materials by passing an electric current and applying pressure to weld the seam continuously.
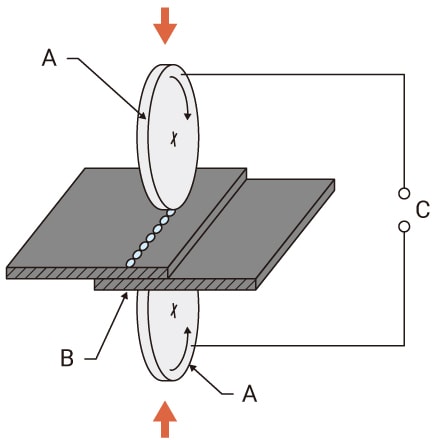
- Roller electrode
- Weld
- Welding power supply
During the production of small crystal oscillators and gyroscope sensors, it is necessary to seam-weld their lids in vacuum to improve product performance and suppress performance degradation over time. This is done with a vacuum seam welder that can provide leak-tight sealing using roller electrodes in a vacuum.