Dimensional Measurement of Large-scale Quartz Glass Products
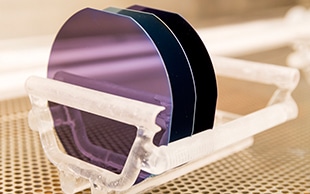
Quartz glass is superior to ordinary glass in various aspects such as its light transmission properties, heat resistance, and corrosion resistance. It is frequently used in optical components, semiconductors, and semiconductor manufacturing devices.
The dimensions of products made of quartz glass are usually measured using contact-type measuring instruments such as hand tools and bridge coordinate measuring machines (CMMs), with the instrument used selected according to the point to be measured.
In an increasing number of cases, these measuring instruments are not sufficient to meet requirements, including reducing manufacturing and installation time while maintaining dimensional accuracy.
This section explains basic knowledge of quartz glass. It also introduces various examples for optimizing these measurements while focusing on the necessity of dimensional measurement, precautions for measurement, and differences in measurement efficiency arising from differences in measuring instruments.
- What Is Quartz Glass?
- Necessity of Dimensional Measurement of Large-scale Quartz Glass
- Dimensional Measurement of Large-scale Quartz Glass Products
- Problems of Dimensional Measurement of Quartz Glass Products and Their Solutions
- Optimization of Dimensional Measurement of Large-scale Quartz Glass Products
What Is Quartz Glass?
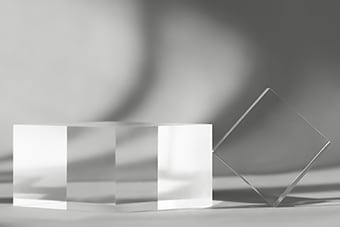
Quartz glass is a type of glass made from ultrapure crystals (silicon dioxide: SiO2). Compared with ordinary glass (soda-lime glass), quartz glass contains far fewer impurities such as metal, so it has better light transmission properties and heat resistance. Thanks to these characteristics, quartz glass is used as a material for optical parts, such as lenses and prisms, semiconductor manufacturing device parts, semiconductors, and windows of high-temperature chambers.
Differences from ordinary glass
Ordinary glass is made from sand called silica sand and contains various impurities. Quartz glass is made from refined or chemically synthesized crystals. Quartz glass is characterized by its very high light transmission properties because it contains few impurities. It can also withstand rapid temperature changes because it has high heat resistance and an extremely low coefficient of thermal expansion.
Type of quartz glass
Quartz glass can be broadly divided into fused silica glass and synthetic silica glass according to the manufacturing method.
Fused silica glass
Fused silica glass is manufactured by fusing crystal powder with an oxyhydrogen flame or electric furnace and then cooling. The crystals used for fused silica glass contain many metal impurities, but high transparency can be achieved by removing them through refining. Fused silica glass can be manufactured easily and at lower cost than synthetic silica glass.
Synthetic silica glass
Synthetic silica glass uses crystals containing few impurities as a raw material and is manufactured by chemical synthesis, such as hydrolysis of silane using hydrogen and oxygen. Synthetic silica glass has high light transmission properties over a wider wavelength band than fused silica glass. However, its manufacturing costs tend to be higher than fused silica glass because synthetic silica glass needs to be processed in clean environment.
Quartz glass applications
Quartz glass, which has high heat resistance and light transmission properties, is mainly used for electrical and electronic devices.
The high heat resistance of fused silica glass makes it suitable for parts that need to have high thermostability to retain their shapes, so it sees use in furnace tubes, boats, lamps, and other parts used in high-temperature processes such as heat treatment in semiconductor manufacturing. Fused silica glass is also used for vacuum depositors, vacuum chambers, and similar devices.
Synthetic silica glass has high homogeneity and light transmission properties, so it is used for optical parts, such as lenses and prisms mounted on exposure equipment used for semiconductor or liquid crystal manufacturing, photomasks for manufacturing of optical fibers, semiconductors, and liquid crystal displays, and other parts that need these characteristics. Synthetic silica glass also has high resistance to chemicals, including corrosion resistance, except for some solutions and gases such as hydrofluoric acid, phosphoric acid, alkalis, and alkali metal compounds. This makes it an indispensable material for parts used in semiconductor manufacturing processes that use chemicals.
Necessity of Dimensional Measurement of Large-scale Quartz Glass
Quartz glass is used for many electrical, electronic, and manufacturing devices, all of which are precision components that require extremely high dimensional accuracy. Even subtle errors in manufacturing can directly lead to product defects.
For example, boats used for batch deposition and batch etching during semiconductor manufacturing store wafers on their holders. A few dozen wafers can be held on a boat and the pitch accuracy of the wafers it holds affects process quality. If the dimensional accuracy of the outer diameter of holder parts and the assembly accuracy of boats are low, the wafer interval vary. Inappropriate intervals prevent correct processing and cause defective wafers. Boats need to be strictly inspected by measuring their dimensions during manufacturing. For boats used in heat treatment, dimensional measurement is also required during periodic maintenance because they may be deformed by heat.
Dimensional Measurement of Large-scale Quartz Glass Products
Typical large-scale quartz glass products include boats and tubes used in semiconductor manufacturing devices and photomasks for liquid crystal display manufacturing. This section explains dimensional measurement of quartz boats made from quartz glass as an example.
Measurement point
For dimensional measurement of quartz boats, it is important to measure the flatness of the top and bottom plates and the perpendicularity of the plates to the pillars that connect them. Inappropriate flatness or perpendicularity may cause misalignment between the centers of the top and bottom plate, which also needs to be inspected by dimensional measurement. It is also important to measure the width of wafer holders. These are important inspection points not only during manufacturing but also during periodic maintenance because their accuracy directly leads to process reliability.
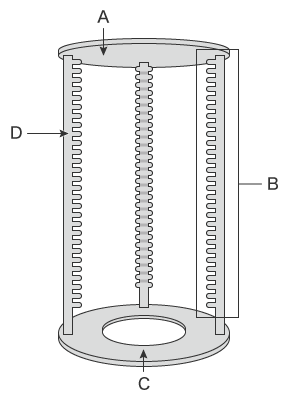
- A
- Top plate
- B
- Holders
- C
- Bottom plate
- D
- Column
Problems of Dimensional Measurement of Quartz Glass Products and Their Solutions
Dimensional accuracy of quartz glass products must be checked not only during manufacturing but also during the periodic maintenance carried out after installation. Quartz glass has high light transmission properties, which makes it difficult to measure its dimensions with measuring instruments that use lasers or LED light. For this reason, contact-type measuring instruments are used to measure quartz glass. However, measurement using hand tools, such as dial gauges and angle gauges, is not accurate enough, making it difficult to measure GD&T accurately. When a bridge CMM is used, measurement cannot be performed when you want, because delicate quartz glass products need to be transported to a measuring room. Due to the skills required for their operation, these instruments can only be used by a limited number of operators.
There are many cases in which dimensional measurement problems with quartz glass products cause delays in delivery and manufacturing process startup and process failures after installation in manufacturing lines.
To solve these problems, the latest CMMs are used in an increasing number of cases.
KEYENCE’s Wide Area Coordinate Measuring Machine WM Series enables high-accuracy dimensional measurement of quartz glass products with the wireless probe. Even recessed areas of products can be reached with no movement restrictions within the measurement range, which allows for single-person measurement with the simple operation of touching targets with the probe. Also, unlike measurements using hand tools such as dial gauges and angle gauges, results do not vary, enabling quantitative measurement. The WM Series is also equipped with functions that can compare measurement data with CAD data and create CAD data from measurement data.
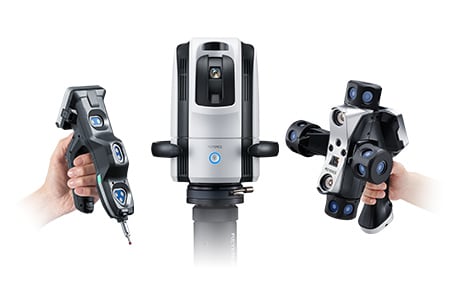
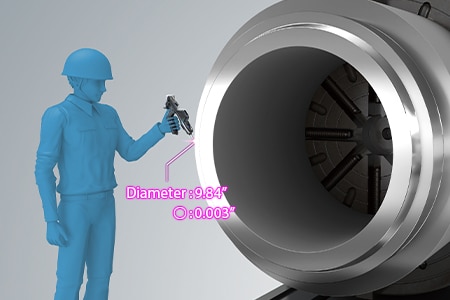
Dimensional measurement of quartz boats and quartz tubes
Important dimensional measurement elements for quartz boats include the width of holders, flatness of top and bottom plates and their perpendicularity to the pillars. For quartz tubes that cover quartz boats, important measurement elements are the cylindricity and distance between the cylinder center and the gas tube center as well as their inner and outer diameters.
Process reliability is especially likely to be impacted when the inner and outer diameters, cylindricity, or distance between the cylinder center and the gas tube center of quartz tubes are out of tolerance, because the boats are prevented from containing the correct number of wafers or achieving a high level of vacuum.
Hand tools are not accurate enough for measurement, because dimensions of the parts of quartz boats and quarts tubes need to be accurate within tolerances of 0.1 mm (0.0039″). Measured values can vary from measurer to measurer and it is difficult to convert warpage and curvature to values as flatness. When using bridge CMMs, the number of operators that can perform measurement is limited and a lot of work is required to transport workpieces to a measuring room.
The WM Series enables easy dimensional measurement of quartz boats and quartz tubes by simply touching with the wireless probe. Unlike hand tools, measurement results do not vary, enabling quantitative measurement. It is possible for a single person to measure GD&T of quartz tubes, such as flatness, circularity, and cylindricity, as well as their inner and outer diameters and the distance between the cylinder center and the gas tube center. The measured elements can be converted to values, and the distance between virtual lines can also be visualized.
What’s more, the portability of the WM Series allows it to be brought into manufacturing and installation sites and immediately measure the dimensions. Workpieces can be measured in manufacturing lines, so they do not need to be removed and returned, eliminating the risk of deformation.
It can also automatically convert measurement results into inspection reports. Photographs can be included in inspection reports, making them easy to understand. The reports use the rich text format (RTF) is used, so they can be edited easily.
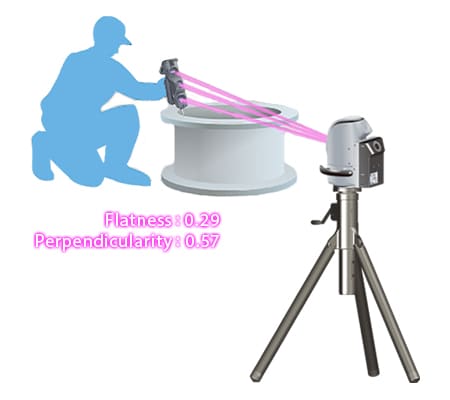
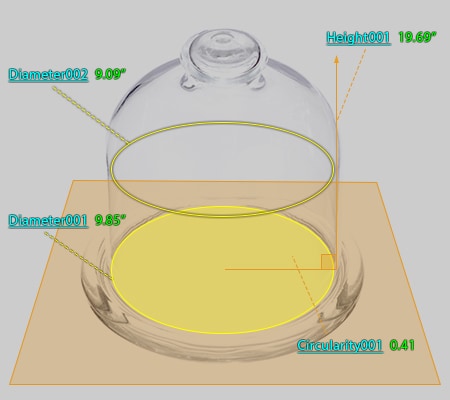
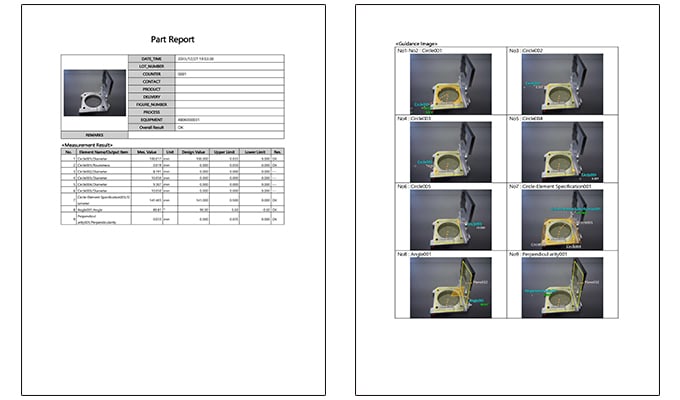
Optimization of Dimensional Measurement of Large-scale Quartz Glass Products
The WM Series enables single-person measurement of quartz glass products with the simple operation of touching the wireless probe to the measurement point. In addition to the features introduced above, the WM Series has the following advantages.
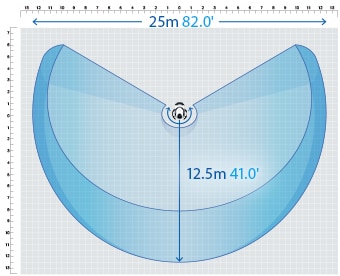
- High-accuracy measurement over a large area
- A wide measurement range up to 25 m (82.0'′) can be measured with high accuracy. The WM Series is equipped with the navigation measurement mode, which enables measurement at the same point according to a memorized measurement procedure, allowing anyone to obtain the same measurement data.
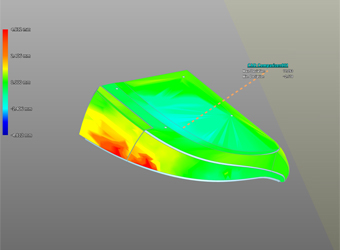
- Check with 3D CAD data
- Comparison measurements are possible between a part being measured and a shape imported from a 3D CAD file. The points of difference between the part and the 3D CAD data can be displayed as a color map. This allows for measurement of free-form curved surfaces and profile tolerances.
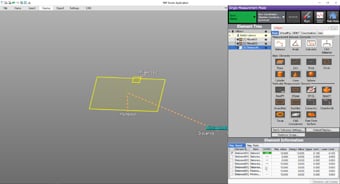
- Easy-to-understand interface
- CMM interfaces are often a mess of complex and unfamiliar commands. The WM Series provides intuitive operation using images and icons, so anyone can easily understand how to operate the system.
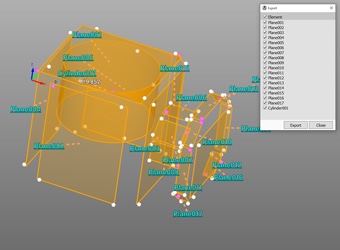
- Measurement results can be output as 3D models
- The measured elements can be exported as a STEP/IGES file. 3D CAD data can be created on the basis of the measurement results of an actual product even if no drawing is available.
The WM Series strongly supports post-measurement work, such as comparison with 3D CAD data and inspection report issuance, as well as dimensional measurement of large-scale quartz glass products. It dramatically improves the efficiency of manufacturing of large-scale quartz glass products, their dimensional check after assembly, and of work indispensable for their quality management.