What is Traceability?
Basic Knowledge about Traceability, an Indispensable System for Quality Management
Traceability is the ability to trace all processes from procurement of raw materials to production, consumption and disposal to clarify "when and where the product was produced by whom." Due to improving product quality and the rise in safety awareness in recent years, traceability has been increasing in importance and spreading into a wide range of fields, such as automotive, electronics, food and pharmaceutical. This section describes basic knowledge about the increasingly-popular traceability.
Concept of Traceability
The term Traceability is formed by Trace and Ability. Although its definition slightly varies depending on the industry, such as automobile, electronic component, food, and pharmaceutical, it is defined as follows in the manufacturing industry:
- Traceability
- Necessary information such as manufacturers, suppliers, and distributors is recorded. This information is tracked in all processes from procurement of raw materials and parts to machining, assembly, distribution, and sales to ensure that their histories can be traced.
Traceability has been defined in the ISO 9001 standard from the International Organization for Standardization.
Two Perspectives on Traceability
Although there are various ways to view traceability, it can be generally divided into two perspectives: chain traceability and internal traceability.
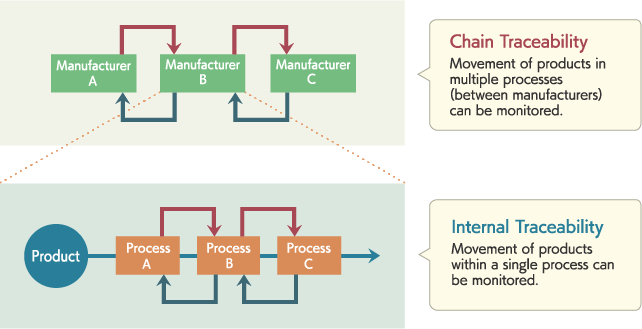
Chain Traceability
The general concept of traceability in the world applies to chain traceability. Chain traceability means that the history from procurement of raw materials and parts to machining, distribution, and sales can be traced forward or backward. Manufacturers can monitor “to where their products have been delivered (= can trace forward)” while companies and consumers in the downstream can understand “from where the products in their hands have come (= can trace back)”.
This provides manufacturers with the benefit of easier cause investigation and product recall when unexpected problems occur with their products. Consumers can also use this as a benchmark to select highly reliable products, without worries such as mislabeling.
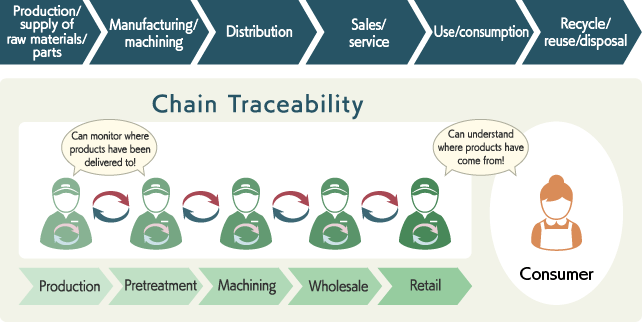
Internal Traceability
Internal traceability means to monitor the movement of parts/products within a limited specific area in a whole supply chain, such as a single company or plant.
For example, an engine assembly plant procures engine parts such as camshafts and pistons from suppliers and assembles them.
Management and utilization of the manufacturing history and inspection results of these parts by the plant can also be regarded as internal traceability.
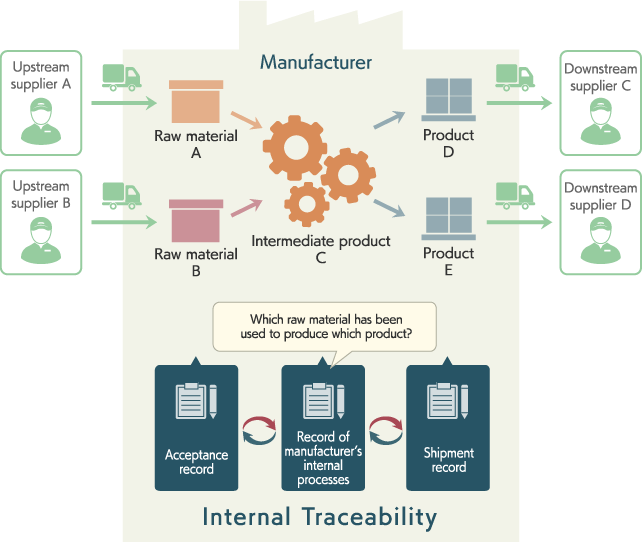
Specific Example of Internal Traceability
Traceability in Manufacturing Processes
Traceability in manufacturing processes is an activity of collecting and managing information regarding what has been done in manufacturing processes from acceptance of raw materials and parts to shipment of products. For traceability in manufacturing processes, each product or lot is assigned an identification number, and then information such as work details, inspection results, and dimensions are linked to this identification number in each process so that it can be utilized for assembly in a later process. Using this information for machining contributes to the improvement of production/work efficiency and quality.
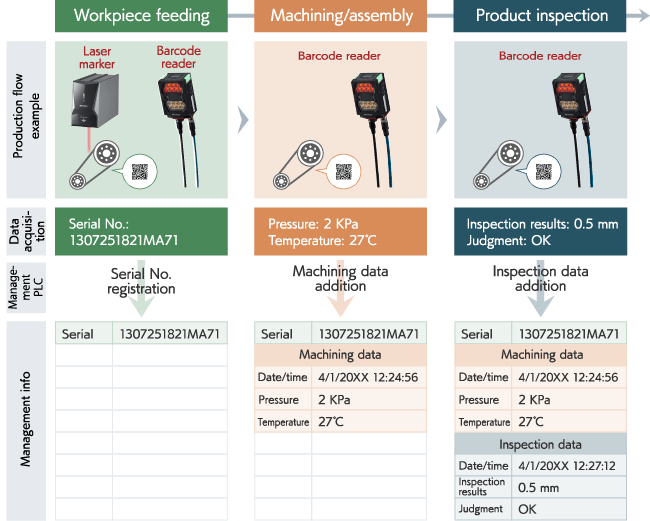
Traceability in Parts Control
Traceability in parts management is used to control and operate repeatedly used parts such as tools and jigs. Serial numbers for individual identification (such as 2D codes) are marked on each tool to manage their conditions, including usage and wear limits. As the entire flow, warehoused tools and other parts are marked with management 2D codes and assigned information such as plant names, shelf numbers, and serial numbers to manage put-out and return. Other information such as the count and date/time of grinding is collected and managed to maintain and stabilize product quality.
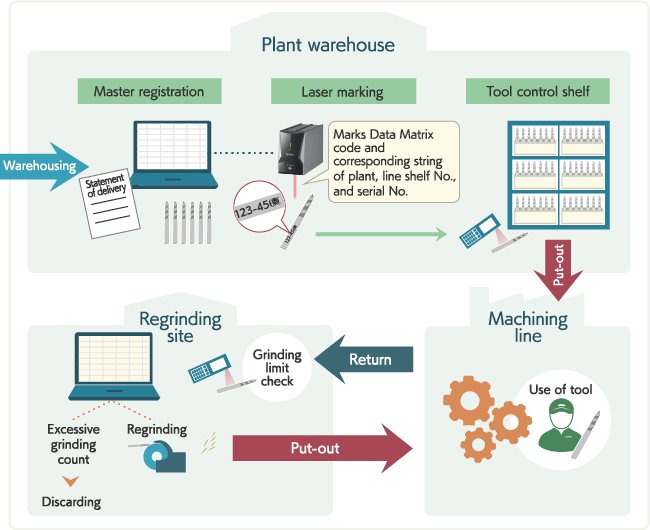
Why is “Traceability” Important?
If a product quality problem occurs, the manufacturer of the product must take effective measures promptly.
A slow or ineffective response from the manufacturer will create a sense of distrust among consumers or business partners, which may even endanger the existence of the company.
In addition, as laws to protect consumers have been implemented, the number of companies required to quickly recall their products due to problems has been increasing every year.
Traceability has long been aggressively promoted in the automotive industry. It is widely utilized for preventing recall problems, minimizing damages, and extracting/improving management challenges as well as ensuring quality management. It is, however, difficult to check the data from manufacturing through disposal of all components numbering several tens of thousands, and to observe laws and regulations that change with the times. Furthermore, globalization is progressing, while cost and delivery-time competition are intensifying in recent years, so the importance of traceability keeps increasing. There is an urgent need for building a history management system from a global perspective that covers both inside and outside of the plant. For details, refer to Automotive industry in the section describing the standards, laws and regulations concerning traceability.