Building an Identification System
Building a System that can Clarify and Identify the Flow of Objects
This section describes the procedures for implementing traceability step by step by using an example of a typical production flow in the manufacturing industry. In order to ensure traceability, you first need to identify parts and products and then manage them by linking objects and information to them. The important concepts are identification and association. This page first describes the method of organizing the flow of objects, which is the initial step toward achieving traceability, and then explains identification.
Flow of objects
There are various ways to view traceability, such as internal traceability and chain traceability. This section describes an example of internal traceability that is implemented within a limited range, such as a plant or a company. When you consider implementing traceability, start clarifying the flow of the production processes by checking points such as:
- Are the raw materials and parts supplied from one company or multiple companies?
- Who checks the delivered materials and parts against the delivery slips and how?
- Is inventory controlled individually or by lots?
- How are the work reports on machining, assembly and inspection recorded and managed?
Keep track of the flow of objects from the acceptance of raw materials and parts to the shipment of products, and consider questions such as "are materials and parts controlled individually or by lots?" "how is the information assigned, read and managed?" "what information is necessary and what information should be acquired in preceding and subsequent processes?" and "how can we change the processes to ensure traceability effectively?"
Identification and Association
Identification
Identification means uniquely recognizing raw materials, parts and products individually or by lots. The basics of identification are to allow recognition of every single product even when products of the same shape and material are manufactured in volume.
Identification can be made in two ways: Assigning individual identification symbols to each part or product; and viewing a specific group to be a lot and assigning an identification symbol to the lot. Individual items or groups to which a single identification symbol is assigned are called identification units.
Individual management (Serial number management) | Lot management |
---|---|
Each part or product is assigned a unique serial number and managed individually. When a recall occurs, problematic products can be located reliably. This method is also called serial number management because it uses serial numbers (unique numbers).
|
Products manufactured under the identical conditions are viewed as one group (lot) and each lot is assigned an identification number. The prerequisite is that all products of the lot are confirmed to have identical quality. Since all products of the lot have the same identification number, individual products cannot be identified.
|
Serial No. | Lot No. |
---|---|
![]() |
![]() |
Lot management allows you to achieve traceability at a lower cost because you can save management efforts by enlarging the scope or range of identification. On the contrary, if high accuracy is required for traceability, you need to make the lot smaller or to select individual management.
Association
Association is linking an object to an object, an object to information, or information to information. For example, assume you have an engine into which parts of varying sizes, such as crankshafts and piston valves, are assembled. Association is a set of rules to accumulate, organize, and retrieve information so that you can determine details from the identification symbol, such as where the piston being used was manufactured or in what process the connecting rod was machined. It is also called linking, and is essential for implementing tracing forward and tracing back.
Cautions on Lot Creation
In lot management, the tracking accuracy varies depending on where you separate one lot from another. The simplest way of lot creation is to group identical products manufactured in a day as one lot. For example, when 1000 pieces are manufactured in a day, group the 1000 such pieces as a single lot and use the same lot number for them. The parts or products of a single lot must be manufactured with the same machine in the same day and have the same quality.
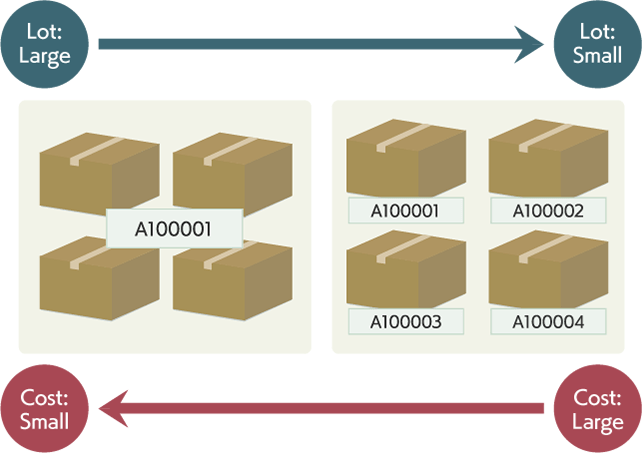
If robot settings are changed, screws from a different supplier are used, or the person in charge of work changes during production, the product quality may vary. In such cases, the lot number may be changed as well (making the lot smaller). When a lot is made smaller, you can limit the scope of recalls when defective products are found; however, that requires more labor for segregation management and increases management costs. Therefore, it is important to consider cost-effectiveness when you create lots.
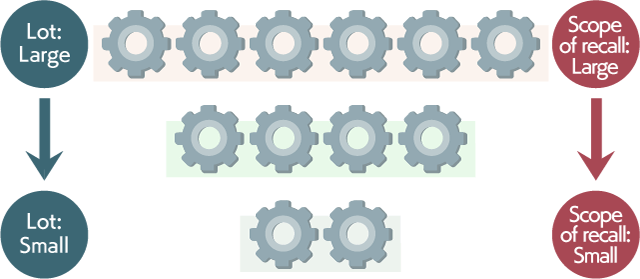
Optimized Lot Creation through Segregation Management
Sometimes lots are made smaller in order to prevent the entry of different products in a production process or to increase the tracking accuracy. You can adjust the identification units without greatly changing the current production process, such as by using different lot numbers for different lines to be used, or by changing lot numbers at shorter time intervals. This method of lot management by dividing a lot is called segregation management.