Vision Examples in the Automotive Industry
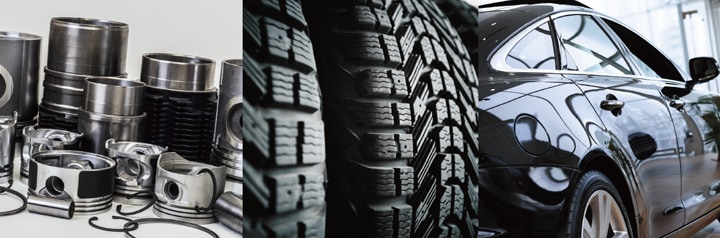
Using Vision to Inspect and Manage 30,000+ Parts
Various inspections of operation panels
Detect multiple defects in operation panels such as incorrect switch assembly or defective LCD display. Conventional image processing made detection based on the area or rough pattern shape of each mark. Detection failed due to similar shapes and sometimes multiple cameras were required to ensure judgment accuracy for the inspection of large panels.
The XG-X/CV-X Series offers a profile search function, PatternTrax, that allows high-accuracy detection through recognition using the profile information of the marks. Using a high-pixel camera with up to 21 megapixels achieves high-accuracy and simultaneous detection of several parts of large panels with a single camera.
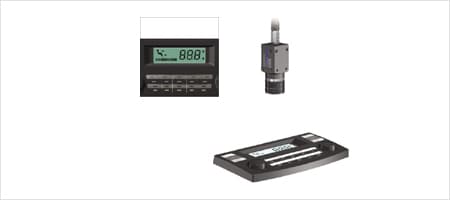
Inspection for defective motor wire tying and soldering
Detect defective motor wire tying and soldering. Image processing using monochrome cameras could not differentiate the colors of the wire, terminal and solder.
The XG-X/CV-X Series has a unique color extraction engine to ensure easy and reliable extraction of the wire which was unstable with conventional methods. Detection is stable even when the ambient light or the gloss of the target changes.
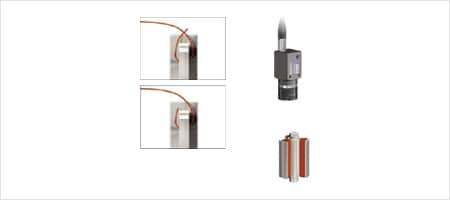
Inspection of injectors for improper assembly
Check for the improper assembly of injector components through outer diameter measurement and color differentiation. Conventional machine vision made false judements due to incorrect edge detection. Monochrome cameras could not correctly differentiate the colors of certain components.
The XG-X/CV-X Series has a unique edge detection algorithm that allows stable detection and eliminates misjudgment. The Profile Position function automatically determines the maximum and minimum diameters, which reduces man-hours for setup. Since color cameras are supported, it is also possible to differentiate the components by colors.
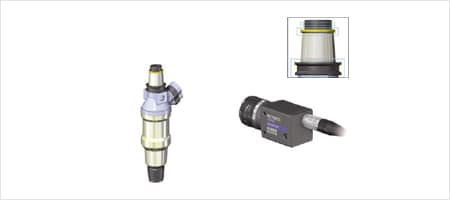
Checking the type of seat belt brackets
Detect the subtle differences among the shapes of seat belt brackets to identify the type. Conventional visual inspection took considerable time and involved higher risk of oversight when production volume increased.
The introduction of machine vision achieves automatic 100% inspection and eliminates oversight. Even when there are minor differences in shape, the XG-X/CV-X Series allow reliable differentiation by measuring several points simultaneously.
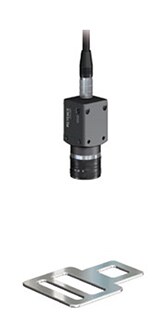
Camera Display
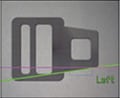
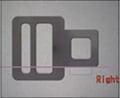
Differentiation of gear types
Detect the differences in the gear diameter or the number of gear teeth to identify the type. Conventionally, only visual inspection was conducted in the assembly process. Sometimes different types were found after assembly, which decreased the yield rate.
Introducing machine vision to conduct inspection before the assembly process prevents assembly failure from occurring. The XG-X/CV-X Series offers a profile search function, PatternTrax, to achieve stable detection regardless of variations in the target surface conditions, background brightness, or colors.
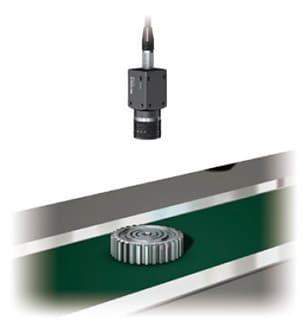
Camera Display
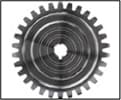
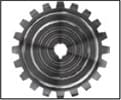
Differentiation of connecting rod types
Measure the total length or diameter of connecting rods to check for different types. Conventionally, visual inspection was conducted before the parts were fed to the line. Sometimes different types were found in the assembly process.
Using machine vision to measure the total length or diameter of connecting rods during transfer can prevent the mixing of different types. The XG-X/CV-X Series can measure hard-to-find subtle differences in hole diameters to ensure accurate differentiation of types.
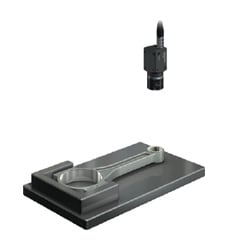


(different diameter and total length)
Detecting grease application amount
Inspect the grease application amount. Conventional inspection used color sensors, which were capable of presence detection only. The parts with insufficient application were also judged as OK.
The XG-X/CV-X Series allows stable detection without being affected by variations in the color of the grease or target surfaces. The 3D inspection function can measure the area and volume of the grease, which enables the judgment of the amount as well as presence detection.
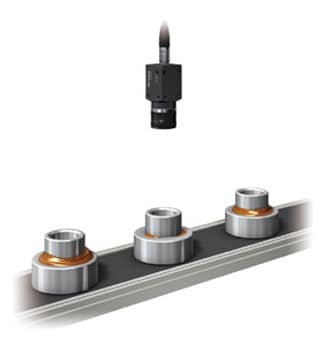
Camera Display
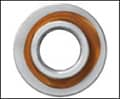
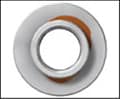
(not enough grease)
Inspection of the presence/misalignment of O-rings during EGR valve assembly
Check for the misalignment of O-rings before press fitting in the assembly process of EGR (Exhaust Gas Recirculation) valves. Conventionally, presence and misalignment were checked only visually before press fitting. The inspection was not reliable because the O-rings were hard to see.
The introduction of machine vision into the inspection process achieves reliable automatic 100% inspection without errors. The XG-X/CV-X Series offers a profile search function, PatternTrax, to achieve stable detection regardless of variations in the background colors. The ultra-compact camera (12 mm square) and side view attachment enable installation in tight spaces.
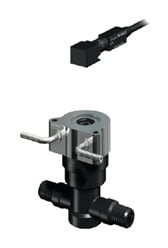


(misaligned O-ring)
Seating confirmation of targets inside hot forging molds
Confirm the seating of a target inside a mold in a hot forging process. The press cycle was three to five seconds. Conventionally, an operator had to attend constantly to confirm seating, so labor costs were high. In rare instances, defective forging was found due to oversight.
Color to Gray processing of the XG-X/CV-X Series can convert even the influence of the infrared light emitted from the metal heated red hot into a clear image with high contrast. This ensures stable automatic inspection and saves labor.
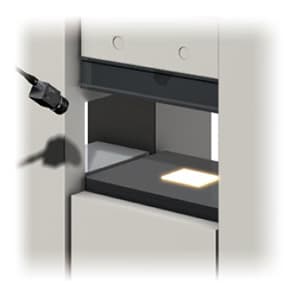
Camera Display
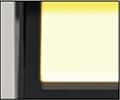
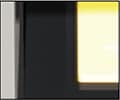
(part position drift)
Inspection of wheel covers for mixing of different types
Inspect the differences in wheel cover shapes to prevent mixing of different types. Conventional machine vision could not recognize subtle differences.
The XG-X/CV-X Series offers a profile search function, PatternTrax, that allows recognition of subtle shape differences based on edge information. This allows reliable detection of the differences among types.
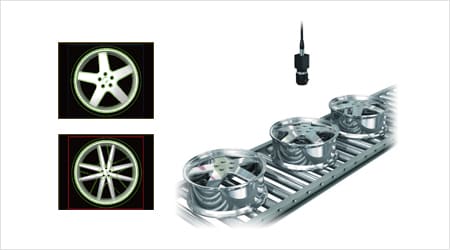
Differentiation of tire types
Detect the differences in color marks of tires to prevent mixing of different types. It was difficult to accurately recognize the differences among marks with conventional monochrome images.
Color cameras allows checking of the shades by color extraction and reliable identification of different types. The XG-X/CV-X Series supports a variety of color cameras. You can select the optimum camera based on the number of pixels, specifications, and transfer time to match the inspection details.
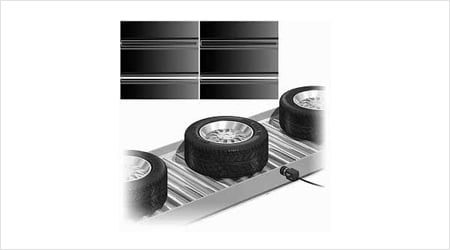
Inspection of liquid gasket (FIPG) application
Detect defective application of liquid gasket (FIPG) applied to various parts such as engines, ATs and oil pans. Conventionally, inspection was performed visually. This could find a complete lack of application; however, delicate judgment such as thicker or thinner application depended on the inspector.
The Profile Width mode of the XG-X/CV-X Series allows measurement of application width continuously at multiple points, so thicker or thinner application can be inspected accurately. Another advantage of archived image saving function is that it allows easy checking of the section of defective application at a later time.
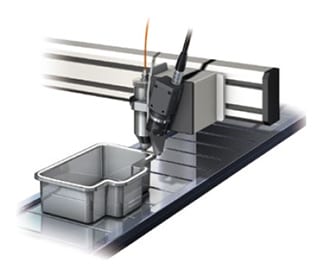
Camera Display
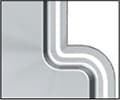
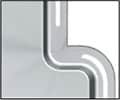
(coating break)
Inspection of camshafts for pinholes
Rotate a camshaft to check for pinholes on the surface. Conventionally, 100% inspection was conducted visually; however, there were problems with oversights and high labor costs.
Line scan cameras allow reliable inspection of cylindrical products. The introduction of machine vision enables reliable 100% inspection as well as reduced inspection costs.
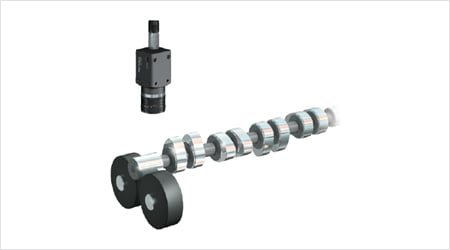
Appearance inspection of bearings
Check bearings for appearance defects. Conventional visual inspection had problems of variation in judgment among workers and oversights.
The introduction of machine vision ensures reliable inspection of size, inner/outer ring assembly, and appearance. This inspection can easily be applied to high-mix production lines.
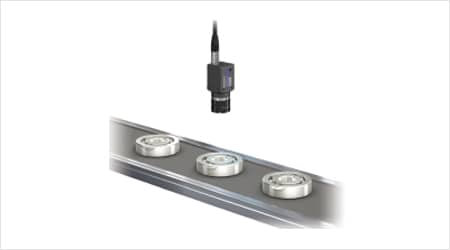
Inspection for swarf remaining on pistons
Detect swarf remaining in piston grooves. Conventionally, this was done visually by inspection personnel. The judgment depended on the individual and it was impossible to perform inspection based on certain criteria.
Using the XG-X/CV-X Series with back lights to detect the presence of swarf in the groove allows 100% inspection for minute swarf based on specific quantitative criteria without oversight.
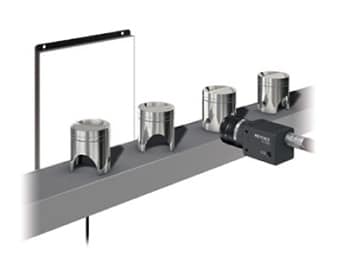
Camera Display
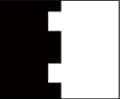
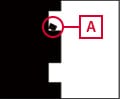
Chip
Inspection of car audio LCD characters
Check if parts of characters shown on the display are missing. Conventionally, the inspection was done visually; however, some products escaped inspection and the labor costs were high.
The cost for visual inspection can be reduced by automating the inspection with machine vision. In addition to missing parts of characters, the system can inspect several items simultaneously, such as checking for the flaws on the LCD surface and recognizing displayed characters.
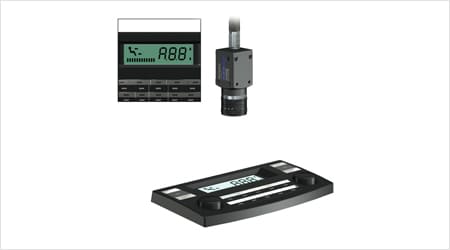
Appearance inspection of various sections of rubber molded parts
Inspect rubber molded parts for defects. Conventionally, visual inspection was performed but it was difficult to identify defects reliably.
The LumiTrax function captures an image of a target using a ultra high-speed camera and ultra high-speed segmented lighting. This enables high-speed and stable detection of minute defects without being affected by variations in targets or the surrounding environment.
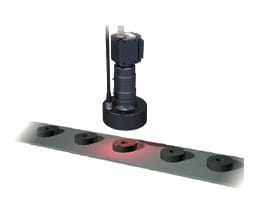


LED lighting inspection of taillights
Inspect the LED lighting of taillights and high mount lamps. Visual inspection was conventionally performed, but oversight could not be prevented. It was impossible to conduct quantitative control of the brightness of LEDs.
The XG-X/CV-X Series has a unique color extraction engine that allows easy and quantitative detection of LED light emission. Transferring all measured values and actual inspection images to a PC for storage also enables traceability management.
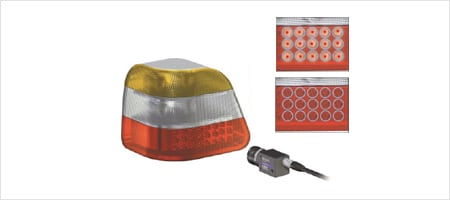
Inspection for missing bearing balls
Inspect bearings for missing balls. Conventionally, the balls were counted visually, but missing balls were often overlooked.
Blob mode, one of the image processing modes included in the XG-X/CV-X Series, can count the balls instantaneously to achieve 100% inspection.
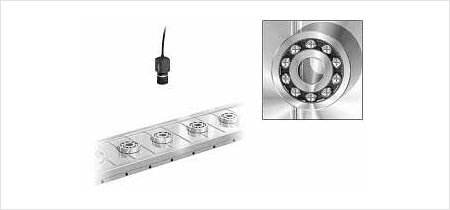
Inspection for burrs and chips of O-rings
Inspect O-rings for burrs and chips. Conventional machine vision could not measure circular distortions, which affected the inspection result and caused variations.
The Profile Defect stain mode of the XG-X/CV-X Series allows high-speed 100% inspection to detect only abrupt distortions such as burrs and chips without being affected by subtle circular distortion of the O-rings.
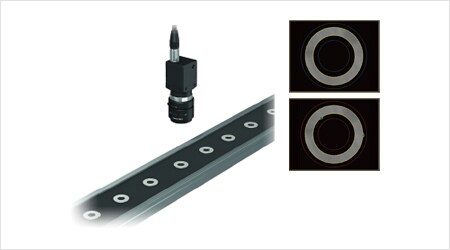
Inspection of meters
Check the position and angle of meter pointers using machine vision. Conventional machine vision required a large amount of difficult calculation settings to measure various positions and angles. There were problems of incorrect detection of edge positions and low accuracy with 0.24 megapixel cameras.
The XG-X/CV-X Series offers eight detection modes for edge detection alone which makes it possible to perform position and angle measurements without the need for difficult calculations. Cameras can be selected from 0.31 to 21 megapixel to achieve high-accuracy measurement that meets the need of the application.
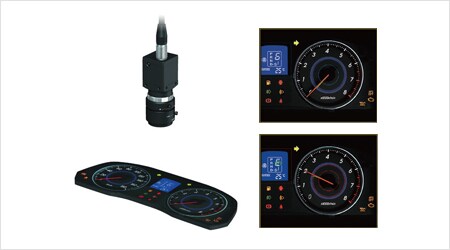
Dimension inspection of piston ring joint clearance
Measure the joint butting clearance of a piston ring. Conventionally, a contact-type feeler gauge was used. However, as the management tolerance has become more severe every year, measurement with the feeler gauge showed variations due to the push-in force, which prevented accurate inspection.
Machine vision ensures quantitative control independent of inspectors and allows complicated dimension measurement to be performed easily. It is possible to make various calculations for measuring the dimension of rounded surfaces or obtaining virtual intersection points of lines, as well as to conduct inspection of products of several hundred types.
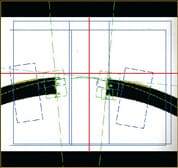
Measuring car body distortion
Measure the distortion of a car body. Strain gauges and other tools were used conventionally, but preparation and measurement took time and labor.
Machine vision can measure the distortion of car bodies by detecting the spot positions of laser pointers. Since the system detects the change in position relative to reference positions, the distortion of car bodies can be measured accurately.
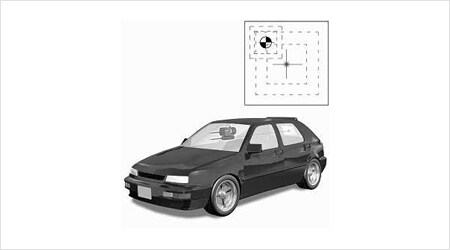
Measuring parallelism of assembled drive shafts
Measure the parallelism of drive shafts. Conventional methods required a dedicated tester or other tools which made the introduction cost high.
The XG-X/CV-X Series can measure the parallelism by measuring the positions of the shafts in images captured with two cameras. Its highly versatile design allows the use of telephoto lenses to provide high-accuracy measurement even from long distances.
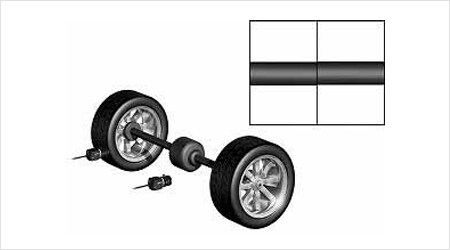
Checking door assembly
Check the accuracy of door assembly. Conventionally, measurement was made visually or with a gauge, which required time and labor. The use of a gauge involves a risk of contact.
The introduction of machine vision reduces labor costs and eliminates the risk of contact. The XG-X/CV-X Series includes Dimensions/Geometry tools that are specially designed for dimension and geometry measurement. You can perform geometry measurement by just selecting the tool and specifying the points with the mouse. Inspection for accurate door assembly can be done easily through dimension measurement of the gap in the door.
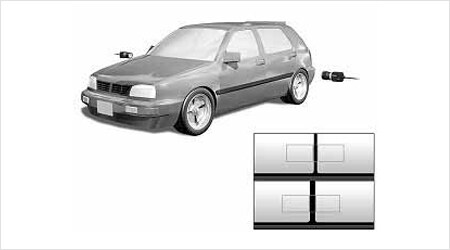
Position detection/Positioning of bead
Detect bead position before bending. Fiberoptic sensors or color sensors were used conventionally, but detection failed due to variations in the surface conditions among lots or because spot detection was used.
The introduction of machine vision prevents the outflow of defective workpieces caused by malfunction. The Defect/Flow inspection mode of the XG-X/CV-X Series ensures reliable detection of bead position based on the degree of color change. This eliminates the need for sensitivity adjustment for variations among lots every time the lot is changed.
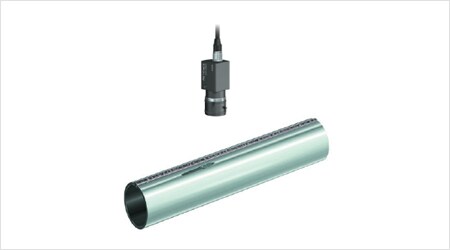
Sensing guide holes during car body assembly
Using machine vision, control robot position and assembly heavy parts such as windshields and doors. Conventionally, this control could not be automated due to the difficulty of position detection of a variety of targets.
The XG-X/CV-X Series offers profile search, virtual circle detection by multi-point edge detection, and flexible search to achieve automation by dealing with various targets and surface conditions. Robots from many manufacturers are supported and can be connected directly without complicated programs. The advanced Auto-calibration function significantly reduces the man-hours for startup.
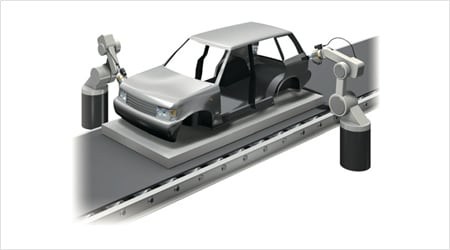
Detecting gear notch angles
Measure the angle of a gear notch and control the operation to ensure assembly at the correct angle. The conventional method rotated the target and used a fiberoptic sensor to detect the presence of the notch and determine the angle. This led to problems with the long time required for positioning and incorrect detection due to center misalignment of the parts.
The Trend edge tool of the XG-X/CV-X Series can find the center of a virtual circle to locate the center of the target based on the periphery. By detecting the line of the notch simultaneously, the system can achieve high-speed, high-accuracy rotation angle detection.
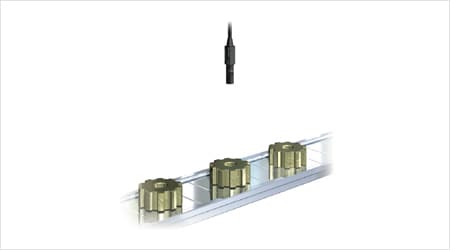
Controlling robot position
Using machine vision, control the position of an assembly/processing robot. Conventional methods required manual teaching, resulting in a lot of man-hours for startup.
You can automate positioning by using machine vision to detect the position of a hole in a car body and feeding it back to the robot. Even when the position of the target deviates a little, the system can correct it. There is no need for confirmation by workers. The XG-X/CV-X series achieves high accuracy based on sub-pixel processing.
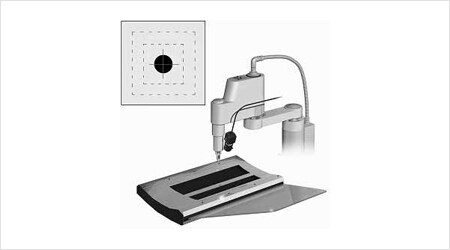
OCR of seat belt buckles
Recognize the characters marked on buckles to identify the type. OCR can be used to identify types such as domestic or overseas, or for left-hand drive or right-hand drive. Visual inspection based on human eyes was the conventional method; however, recognition could fail and cause mixing of different types. Since car seat belts are safety parts, mistakes such as mixing of different types are never allowed.
The introduction of machine vision ensures 100% inspection to prevent mixing of different types. The most important point for inspection using machine vision is to create sharp contrast between the marking and target surface. The XG-X/CV-X Series offers a wide selection of lenses and lights. Its unique OCR function allows stable inspection regardless of variations in marking density, angle of characters, and character size.
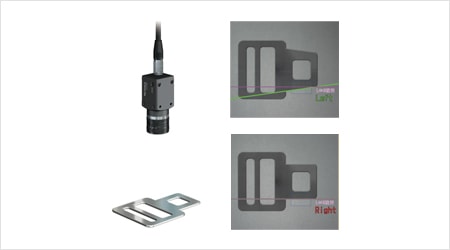
Measuring the width and volume of sealer application
Measure the shape of sealing agent to check the applied amount. Conventional 2D cameras could not determine the height. It was impossible to accurately measure the amount applied.
When the XG-X/CV-X Series is connected with the LJ-V Series in-line 2D/3D laser scanner, the system can measure height, width, position, cross-sectional area, and volume based on 3D vision inspection. This allows automation of the inspection of sealer application. The misalignment of targets can also be corrected in real time.
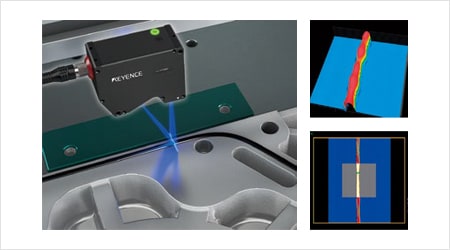