Improved Profitability Due to Less Downtime
Finding partners that will lead to quick recovery from problems
Problems are unavoidable at manufacturing worksites. The best thing would be to eliminate all problems, but it is more important to assume that problems will occur and be ready to recover from them quickly. Especially at worksites where the switch to FA is progressing, small problems result in the stoppage of all production, which leads to major losses.
Machine vision and image processing systems, which are the key parts of operations such as inspection and positioning, serve the vital role of judging the status of the target and controlling operations accordingly. Image processing systems are so important that recovering them quickly can be said to be the most vital element in minimizing loss. This section explains profitability improvements obtained through the quick recovery of image processing systems.
Realizing quick recovery from problems
Production worksites contain a large number of devices including machine vision, image processing systems, PLCs, servo motors, and industrial robots. Realistically, it is not possible to set up a system for understanding and supporting all these devices just with the personnel within your company. To recover from problems quickly and minimize loss, it is important to find partners who can perform maintenance quickly and who can respond to operation problems.
Point 01 Specialized knowledge of image processing
Image processing requires specialized knowledge. Furthermore, cases in which various types of devices are linked together (not used independently) are the norm. Hence, not only is knowledge of image processing required but so is knowledge of other items including knowledge of hardware such as external devices and connections, knowledge of the image processing that processes the information of the captured images, and knowledge of the PLCs that handle this information. When requesting support from a company, the key concept is whether they have engineers who specialize in image processing or not.
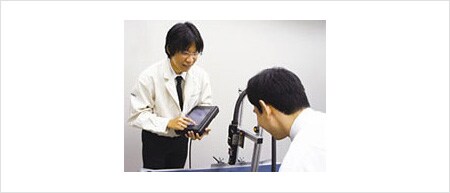
Point 02 Quick repairs and the availability of replacement devices
When a problem causes your production line to stop, not only does your production burst size fall to zero, but major changes need to be made to your production schedule in order to recover the delay in production. This results in losses attributable to factors such as labor costs and utility costs corresponding to the changed schedule. Hence, recovering from problems even 1 minute or 1 second faster is very important. There are also cases where repairs are difficult and it is necessary to ship or replace a replacement device immediately. In this situation, the key point is whether or not the company has devices in stock and can respond to such requirements immediately.
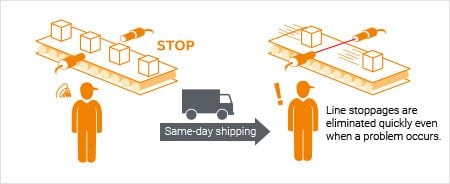
Point 03 Global support system
The globalization of manufacturing has progressed in recent years. It is not rare to only assemble products domestically, with parts being manufactured overseas. One example case is purchasing inspection devices domestically and exporting them to overseas factories. In situations such as this, devices can be repaired and replacements can be requested smoothly so long as the manufacturer also has overseas facilities. Hence, overseas local support is also important for companies that are expanding all over the world.
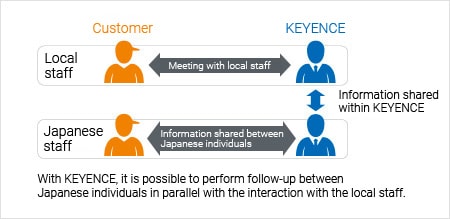
Have you ever experienced any of the following problems?
Have you ever experienced any of the following problems while using image processing systems?
- Only a limited number of employees can handle problems that occur with machine vision and image processing systems.
- You have to go through your distributor to contact the manufacturer, so it takes a long time for replies to reach you.
- You have to go through your distributor to obtain product replacements, and they have a small inventory, so this takes a long time.
- Your representatives at the manufacturer work in sales, so it is not possible for them to handle your technical consultations immediately.
- There is no support for machine vision and image processing systems exported to overseas factories.
- When a problem occurs at an overseas factory, it takes a long time for repair parts to be shipped from Japan.
Domestic and overseas support provided by engineers who specialize in image processing
At KEYENCE, we have established a system that can provide quick support by placing engineers who specialize in image processing to domestic and overseas locations in order to respond to comments from our customers like those listed above. After a product is purchased, we not only explain how to operate it and provide seminars and after-sales support, but we also promptly ship replacement devices as necessary. Our support system covers the entirety of Japan. Furthermore, by establishing facilities around the world starting with the over 30 facilities in our North and Central America network and also including countries in Europe, China, Asia, the Middle East, Oceania, and Africa, we have realized a support system that is equivalent to our domestic one.
We aim to solve problems quickly by having specialized technical representatives follow up on problems not only related to machine vision and image processing systems but peripheral equipment such as lighting and lenses as well. Another one of KEYENCE's characteristics is our insistence to sell directly to our customers without going through distributors. Because all our products are in stock, we can ship products as soon as they are requested from a customer. Products can be shipped immediately to locations within Japan and overseas. This minimizes losses attributable to problems and thereby contributes to improved profitability.
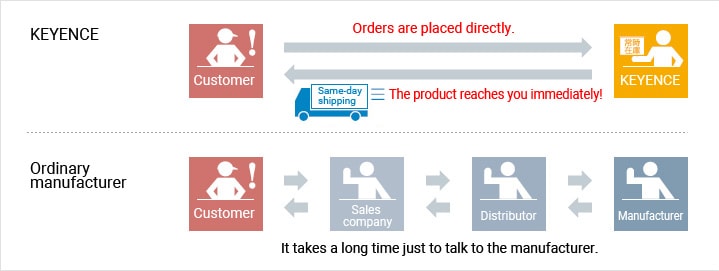
Example of improved profitability through quick recovery from problems
KEYENCE has realized a system that has global support provided by technical representatives who specialize in image processing and the ability to promptly ship products globally. As such, we can immediately respond to inquiries and, if necessary, immediately ship replacements all over the world. The following formula can be used to calculate the profitability improvement obtained through quick recovery from problems, so feel free to use this formula if you are considering introducing an image processing system.
Profitability improvement calculation
Production volume × Unit price × Difference in time required for troubleshooting = Profit improvement effect
【①】products/time × $【②】 × 【③】hours = $【 】of avoided loss
Profitability improvement calculation sheet
① Production volume | products/time | |
---|---|---|
② Unit price | $ | |
③ Difference in time required for troubleshooting | hours | |
$0 of avoided loss
Please enter a numeric value
{item} is required.
{item} must be a positive values.
{item} must be an integer.
Calculation example
A problem occurs on a production line having a productivity of 1,000 products per hour (with each product having a unit cost of $1). It would normally take 3 days to recover from this problem, but calculate the loss recovery amount assuming that a replacement device can be delivered on the same day that the problem occurs. Assuming that the operation time for a day is 8 hours, 3 days of down time would be 24 hours. However, if the down time is only a single day, the time is 8 hours, which results in a difference in lengths of time required for recovery of 16 hours.
1,000 items/hour x $1 x 16 hours = loss recovery of $16,000
The loss recovery is $16,000 and the recovery period is shortened by 2 days!