Improved Profitability Through Improved Introduction/Maintenance Efficiency
Increasing the efficiency of introduction/maintenance with a highly versatile image processing system
As high-mix low-volume production increases to meet diversified user needs, the burden of equipment investment has been increasing. Smartphones and other electronic devices have been miniaturized further and the LCD, semiconductor and electronic components used for them require high accuracy. Inspection of these devices and components needs a variety of inspection equipment.
It is difficult to unify the manufacturers and models of such manufacturing/inspection equipment. Some of them lack versatility or require special operation or maintenance. This can increase equipment inventory, resulting in increased equipment investment or inventory management costs. The key for reducing this wasteful spending is efficient use of equipment. So how can we select and use equipment efficiently? This page introduces a technique using an image processing system as one solution.
Have you ever experienced problems like these?
Versatility and flexibility must be considered when planning optimization and optimum deployment of equipment. When a single piece of equipment can serve several processes, the equipment inventory can be reduced. It is also effective for saving man-hours because workers do not have to learn operations for different equipment. Inspections, in particular, often use dedicated equipment which may lead to a large inventory. If you have experienced any of the items below, there is room for improvement.
- An image processing system has been introduced, but it cannot be used often because its functions are limited.
- Dedicated inspection equipment has been used, but the operating rate is low because functions cannot be added.
- Inspection jigs are used. Since different products require different jigs, inventory management is a lot of trouble.
- Inspection equipment comes from different manufacturers so maintenance takes a lot of labor.
- Designing the production processes require confirmation of compatibility among equipment.
Criteria for selecting an image processing system
If you have experienced any of the items above, first establish clear criteria for selecting inspection equipment. This section introduces the points about image processing systems that must be checked when selecting equipment for optimization and optimum deployment.
Supported robot manufacturers
Before selecting an image processing system, be sure to check the supported manufacturers. As described in the Vision-Guided Robots section, industrial robots use different programming languages depending on the manufacturer. KEYENCE's Vision-guided robotics supports 16 manufacturers from Japan and other countries. This ensures flexible operation in production lines where multiple industrial robots are mixed.
Variety of connectable machine vision
To use image processing for inspection, you need to use a proper machine vision according to the target. It is important to select the best-suited machine vision for the inspection, such as high-pixel cameras capable of detailed inspection for the inspection of LCDs; line scan cameras capable of wide-range inspection for appearance inspection of wide plate materials; and 3D cameras capable of height detection for inspection that is difficult with shading information only.
KEYENCE's machine vision, XG-X Series and CV-X Series, allow you to select freely from 22 area camera models (0.31 to 21 megapixels), 3 line scan camera models and 2 3D camera models. Since the optimum camera can be selected for each use, a variety of inspections can be achieved with one system.
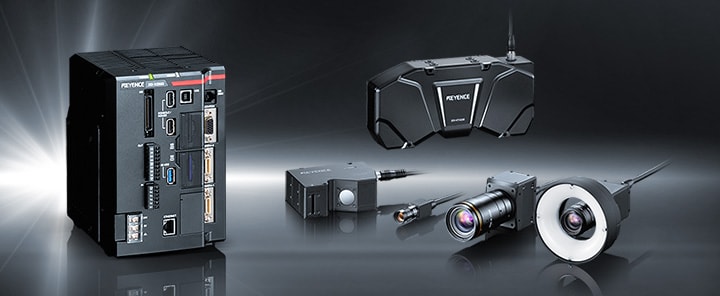
Mixed use of different types of cameras
Conventional machine vision did not allow mixed use of different types of cameras. KEYENCE's XG-X Series allows mixed use of up to four different types from 22 area camera models, 3 line scan camera models and 2 3D camera models. When you inspect cylindrical targets, for example, you can use a line scan camera to capture the lateral surface along the full 360-degree circumference as one image, and then use an area camera to capture an image of the top surface. Combining different types of cameras like this improves processing time and reduces cost simultaneously.
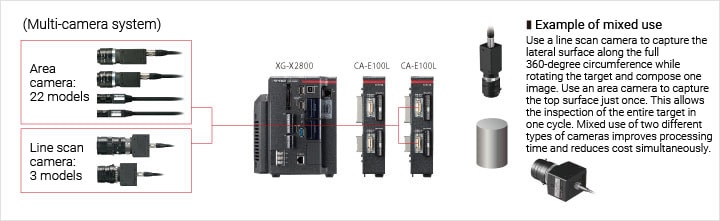
Example of improved profitability by increasing efficiency of introduction/maintenance
The introduction of KEYENCE's versatile image processing system achieves optimization and optimum deployment of inspection equipment. This section introduces a calculation formula for simple estimation of the effect. Please try it if you are considering the introduction of an image processing system.
Profitability improvement calculation
Number of devices purchased due to existing devices' lack of capability × Unit price + Number of existing devices × Unit price + Training costs = Revenue Improvement Effect
【①】models × $【②】 + 【③】models × $【④】+ $【⑤】= cost reduction of $【 】
Profitability improvement calculation sheet
① Number of devices purchased due to existing devices' lack of capability | models | |
---|---|---|
② Purchase price of ① | $ | |
③ Number of existing devices | models | |
④ Purchase price of ② | $ | |
⑤ Training costs | $ | |
cost reduction of $0
Please enter a numeric value
{item} is required.
{item} must be a positive values.
{item} must be an integer.
Calculation example
Assume that you are planning the introduction of three new image processing systems (purchase price: $10,000 each). There are three existing models (purchase price: $5,000 each). The education cost required for the new systems is estimated to be $2,000. What will the profitability improvement be when these multiple image processing systems can be integrated into one system?
3 systems x $10,000 + 3 systems x $5,000 + $2,000 = $47,000 of cost reduction
Effect of profitability improvement: $47,000 !