Appearance Inspection (Foreign Particles, Flaws, Defects)
Appearance inspection (foreign particles, flaws, defects)
Appearance inspection checks for foreign particles, flaws and defects on the surface of parts or products. Appearance inspection typically includes:
- Checking for foreign particles on food packages
- Checking for stains on cloth
- Checking for flaws on metal/resin components
- Inspection for defects, such as chipping or burrs, generated during resin/rubber molding processes
- Inspection for defects in unlit LEDs
Appearance inspection used to rely on visual inspection. Due to increased factory automation (FA), image processing systems have seen increasing use. This page describes applications of image processing that improve inspection for foreign particles, flaws and defects, and introduces the basic principle and latest trends of appearance inspection.
Basic principle of appearance inspection for detection of foreign particles, flaws and defects in images
Advantages of introducing image processing
Appearance inspection is used to find foreign particles, stain, flaws and chipping and to prevent outflow of defective workpieces. Unfortunately, visual inspection has limitations. 100% inspection consumes a large amount of labor and incurs high costs. There are also problems with variation in accuracy due to individual differences among workers and human errors.
It is difficult to find minute flaws or stains, so images must be magnified with microscopes to ensure quality. If the number of targets is limited, offline inspection with a microscope may be possible. If, however, the number of targets is in the thousands or tens of thousands, inspection requires tremendous labor, resulting in significant reductions of production efficiency. Image processing is indispensable for achieving both quality and production efficiency under these conditions.
Capable of differentiating minute foreign particles, flaws and defects
Appearance inspection used to rely on human eyes. Machine vision and image processing technologies have now developed to the point that they can detect minute foreign particles, flaws and defects. KEYENCE provides a lineup of machine vision that range from standard 0.31 megapixel models to high-resolution 21 megapixel models. We can suggest cost-effective image processing systems that meet the specific needs of customers.
Sometimes customers who are considering introducing image processing systems ask“what is the minimum size of foreign particles or black spots that can be found via inspection?”The approximate size can be calculated with the formula below.
Minimum detectable size = B / A x C
- A: Number of pixels of the image pickup device in the Y direction
- B: Field of view (Y direction) [mm]
- C: Minimum number of pixels on the image pickup device that can detect a target [pixels]
The number of pixels varies depending on the camera used. For example, a 0.31 megapixel camera has 480 vertical pixels, whereas a 21 megapixel camera has 4092 vertical pixels. This value refers to [A: Number of pixels of the image pickup device in the Y direction] in the calculation formula.
Item B, field of view (Y direction), can be changed to 10 mm, 100 mm, or any other value by changing the lens. Item C, minimum number of pixels on the image pickup device that can detect a target, should be set to 3 pixels under normal conditions, or 5 pixels under specific difficult conditions.
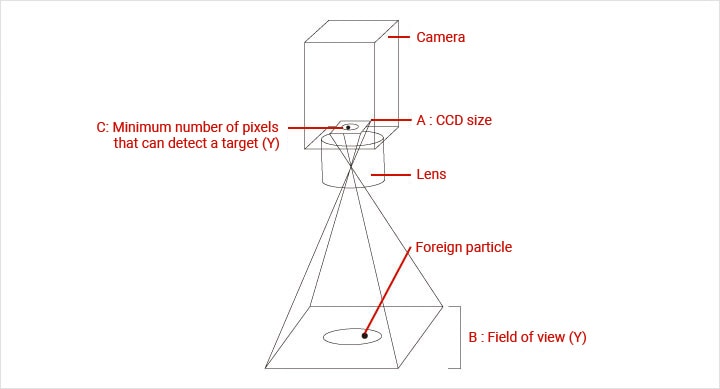
Under the condition above, assume that A = 480 pixels, B = 50 mm and C = 3 pixels, and the calculation is:Minimum detectable size = 50 / 480 x 3 = 0.312 mmThis means that foreign particles or flaws as small as 0.312 mm can be found in the inspection.
If you use a 21 megapixel camera, the calculation is:Minimum detectable size = 50 / 4092 x 3 = 0.037 mmYou can find foreign particles or flaws as small as 0.037 mm, which are difficult to find visually.
When higher inspection accuracy is desired, you need to make the minimum detectable size smaller by using a high-resolution camera such as 21 megapixel type, or by reducing the viewing angle.
Inline 100% inspection is possible
Visual inspection requires offline appearance check, depending on the inspection item. Image processing, however, enables accurate inline inspection for foreign particles, flaws and defects.
Relationship between target speed and image processing speed
Intermittent feeding
These calculation formulas give the maximum number of inspections per minute and the machine vision system processing speed required by using an example of intermittent feeding, in which inspection targets are fed intermittently and the line is stopped for a specific period when each target arrives in front of the camera.
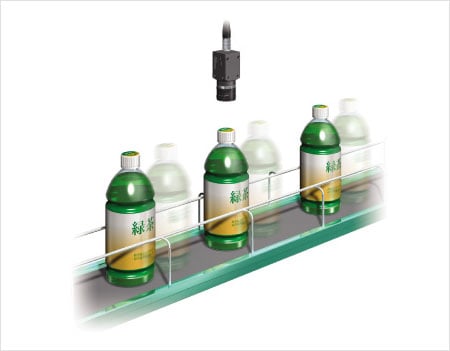
Maximum number of inspections per minute = 60 seconds / Processing time of the machine vision system in seconds
Example: When the processing speed of the machine vision system is 20 ms
60 seconds / 0.02 seconds = 3,000 times/minute (50 times/second)
General appearance inspections can be processed within 20 to 100 ms. If you know the desired inspection speed, you can obtain the necessary processing speed with this formula:
Processing speed required of the machine vision system (ms) = 1 second/Desired number of inspections per second x 1000
Example: When the desired number of inspections is 50 times/second
1 / 50 x 1000 = 20 ms
You can use the formula above to select machine vision that can satisfy your requirements. Note that this is for the case of intermittent feeding. For continuous feeding, where products are fed constantly without stopping the line, you need to consider the shutter speed.
Continuous feeding
For continuous feeding, you need to ensure sufficient shutter speed for the line speed. Otherwise, the captured image will be blurred and accurate inspection will be impossible. In general, set the speed so that the distance moved is about one-fifth of the minimum detectable target size.
Example: the desired minimum detectable size is 1 mm and the line speed is 1 m/second
Reference shutter speed = 1 (mm) / 5 / 1000 (mm/s) = 1/5000 second
Basics of appearance inspection: Image enhance filters
In appearance inspection, you need to recognize and differentiate minute flaws and chipping. Image enhance filters play an important role in producing stable inspection results.
Shading correction
It was difficult to use binary processing,described in the presence inspection section to find foreign particles or flaws. Shading correction cancels gloss or shadows on the target surface to allow accurate extraction of stains or flaws only.
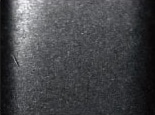
Original image

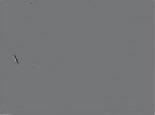
After image enhancement
Bidirectional smoothing filter
This filter removes hairlines or other patterns in the background, and noise. The smoothing effect can be set in the X and Y directions separately. This filter allows extraction of foreign particles only.
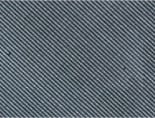
Original image

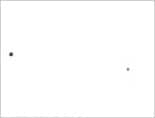
After image enhancement
Blob filter
This filter applies blob analysis described in the presence inspection section to image enhancement. It allows extraction of specific factors only, while removing gloss, shadows, backgrounds, and surface unevenness.
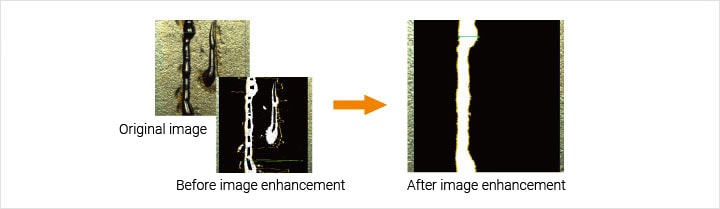
Contrast conversion
This filter creates an image with the best contrast for each area to enhance edges or reduce background noise. Expanding the range of shade difference makes the detection of stains or other defects easier.
Practical applications
Image processing has been effectively used in various appearance inspections. Here we'll see some examples of practical applications.
Inspection for swarf remaining on pistons
Swarf remaining on pistons for car engines is hard to recognize visually and often overlooked during inspection. Image processing systems allow accurate recognition and differentiation of microscopic swarf.
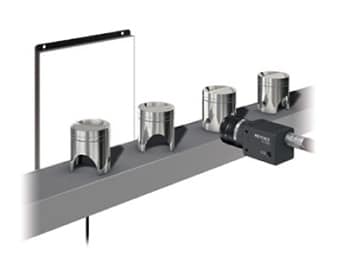
Inspection screen
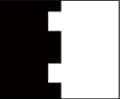
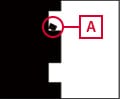
Swarf
Appearance inspection of chip capacitors for various defects
Appearance inspection of chip capacitors for various defects, such as stains, flaws and chips, can be completed simultaneously through the introduction of image processing. Reliable 100% inspection can be achieved and accumulated inspection data is helpful for process improvement.
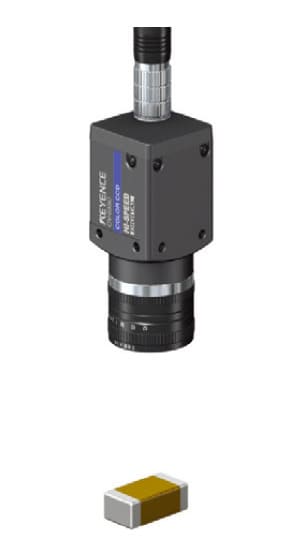
Inspection screen
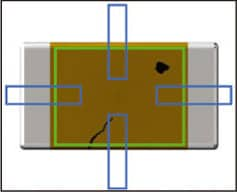
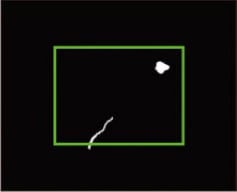
Inspection of foreign particles on trays
As food safety attracts increasing attention, the introduction of image processing systems has been on the rise in the food industry. Foreign particles on trays were previously checked through sample inspection. Image processing allows 100% inspection without extra time or effort. The inspection can also check and identify minute stains, which contributes to stable quality.
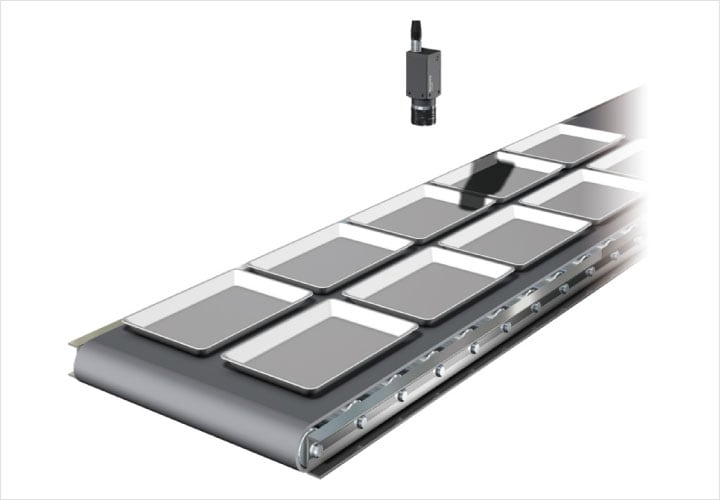