Dispensing
Overview of dispensers
In the manufacturing industry, “dispenser” is a generic term for both equipment that discharges a constant amount of coating fluid and the entire system for that purpose. A dispenser system consists of a central controller for accurate control of coating fluids in addition to a barrel, pump, nozzle, and needle, all with varying structures depending on the material being coated. Dispensers (systems) with various discharge methods are available depending on the coating fluid properties. The following table lists the typical discharge methods.
Method | Description |
---|---|
Pneumatic (syringe) | Coating material is pushed out by air pulses. This is the most popular method and can be used for general purposes. It is also called the air pulse method. |
Volumetric metering | Coating fluid is pushed out though motor-driven volume metering without the use of air. Such dispensers are also called mechanical dispensers. |
Non-contact | Coating fluid is applied through dispersion without making contact with the target. Such dispensers are also called jet dispensers. |
Tubing | Coating fluid is applied through pressure on the coating material tube. |
Plunger | Coating fluid is mechanically compressed in a cylinder. This method works in the same manner as pistons and is effective for highly viscous materials that require high pressure. |
The classifications here are merely examples. There are various ways to classify the types, and some may differ from the descriptions provided here.
- Basic structure of a pneumatic (syringe) dispenser
-
- Air source
- Pneumatic piping
- Regulator/filter
- Dispenser (discharge controller)
- Syringe
Present state of dispensers
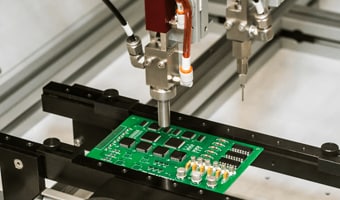
In recent factory automation usage, mainstream coating is performed through high-speed, high-accuracy automatic dispenser systems including multi-axis robots, stage operation, and sensors.
Improvements in automatic coating technology has expanded its use from small-quantity (precision) dispensing, to larger quantity applications. Creating beads of sealant for liquid gaskets, and gear box grease dispension are now possible with automated dispension. Automatic coating with dispensers improves efficiency and functionality even when new materials are introduced.
Application examples of dispensers
Electronic components
- Cream solder coating on packaged PCBs
- Dispenser robots have been used increasingly for high-speed precision coating under conditions where screen printing is difficult.
- Underfilling of PCBs
- A non-contact type dispenser is used to apply underfill to protect packaged PCBs. Accurate control ensures that coating is only applied to target areas without the need for masking
- Bonding of camera modules and lenses
- A small quantity of adhesive is applied without contact (by a jet dispenser) onto camera modules and other components that have been miniaturized as a result of thinner device design.
- LED module potting
- Precise dropping and dispensing is used for potting, enabling quick and accurate fixation and encapsulation.
Automobiles
- Applying moisture-proof agent on ECU PCBs
- The high-accuracy control of non-contact dispensers makes it possible to apply moisture-proof agents only onto target spots of composite components without the need for masking.
- Applying sealant (sealer, primer) onto engine parts
- A dispenser robot with a mechanical pump is used for automatic coating of highly viscous materials of FIPG and CIPG. Applying sealant (sealer, primer) or liquid gaskets in a uniform bead shape ensures high airtightness.
- Greasing of interior parts
- A non-contact (jet) dispenser and multi-axis robot apply grease at an angle to ensure greasing in narrow spaces such as instrument panels and door components.
- Molding on ECU PCBs
- Two-component curing adhesive—which requires care regarding curing time—is automatically applied by a two-component mixing dispenser through robot control.
- Applying vibration-damping material onto car floor
- Compared with conventional sheet material, a coating of vibration-damping material offers higher adhesion and damping ability to curved floor surfaces with a thinner and lighterweight finish in addition to higher work efficiency. A multi-axis dispenser robot automatically applies the material onto only the necessary areas.
Display products
- Adhesion sealing of the glass and polarizing plates of OLED displays (OELDs)
- A small quantity of adhesive is applied uniformly into the small gap between the glass and the polarizing plates to achieve a filled sealing. Piezoelectric jet dispensers are becoming more popular because of their ability for high-speed and fine discharge. This discharge is made possible by the reciprocating motion of a rod controlled by piezoelectric elements that exhibit minute deformation when under voltage.
- Coating of TAB reinforcement agent on FPCs (Flexible PCBs)
- After an FPC is connected to a low-profile LCD or touch panel, a coating of UV curing reinforcement agent is applied to strengthen the thin joined section. The agent can be applied automatically based on precise coating range settings, preventing contact with the panel.
- Applying polarizing agent along the edge of LCD glass
- Conventionally, polarizing tape was used along the edge of LCD glass panels. However, with the trend toward thinner glass panels in recent years, non-contact dispensers have been used to apply a polarizing agent along the edge in accordance with the conditions of the target and to improve productivity through automation.
- Smartphone assembly
- Smartphones and tablets consist of many small components including touch panels, organic EL displays (OELDs), LCDs, FPCs (flexible PCBs), small cameras, sensors, and batteries. As the devices are designed to be thinner and lighter weight, various dispensers have been used for precision coating of small quantities of adhesive in many situations in the assembly process.
Batteries (Secondary batteries and solar cells)
- Secondary batteries
- Sealant is applied to seal electrolyte compartments and other sections of rechargeable batteries.
- Solar cells
- Lines are drawn on the cells and modules of solar panels, or potting is performed
To continue providing high-speed, high-accuracy, stable automatic dispensing using these dispenser robots, it is essential to provide accurate positioning, to monitor the dispensing status, and to send feedback to the equipment. Consequently, the use of high-accuracy laser displacement sensors, cameras, and sensors that serve as the eye of the robot is extremely important for keeping and improving coating quality.