Smartphone and Tablets
The trend toward higher functionality is continuously increasing for electronic equipment such as smartphones, tablets, and other touch panel terminals; smart watches and other wearable devices; and various IoT devices.
Because such equipment is designed to be smaller, thinner (lower profile), and lighter, the components are also required to be more functional through miniaturization, greater diversity, and higher density. Coating is used in many situations as an indispensable technique in the manufacturing processes.

- Adhesion in smartphone and tablet manufacturing
- Functionalization and surface processing in smartphone and tablet manufacturing
Adhesion in smartphone and tablet manufacturing
Using many screws (precision screws) for joining parts in product/component assembly hinders the trend toward smaller and thinner products, an increased number of components, and higher battery capacity.
To solve the problem, adhesive is used for joining parts to minimize the use of screws. This allows for the securement of spaces for numerous components and high-capacity batteries. Meanwhile, automatic adhesive coating improves production efficiency.
- Adhesive coating (UV curing, instant curing, anaerobic, etc.)
-
Product assembly: Cover glass, touch panels, optical films, LCD panels
Internal component assembly: Various modules, FPC (flexible PCBs), lithium-ion secondary batteries (LiBs)
- Cream solder coating
- PCB mounting: Chip assembly on mother boards
- Sealant coating
- Waterproof sealing: Cover glass, phone housing (case), connector surroundings
Topic: Coating quality that supports advanced device performance
The demands for smartphones are ever increasing, such as waterproofing and dustproofing as well as miniaturization and thiner and lighter bodies. This is also true for high-performance outdoor equipment such as wearable devices and drones. The technology most directly related to achieving such properties is automatic coating of small quantities of adhesive or sealant on small targets through the use of dispensers.
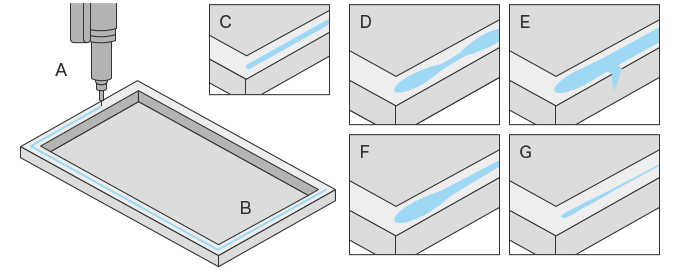
- A. Dispenser
- B. Target (workpiece)
- C. Normal coating
- D. Pulsation
- E. Excessive amount
- F. Pooling
- G. Insufficient amount
In the assembly of these advanced devices and the joining of their parts, coating accuracy directly affects the product quality and performance. Particularly for waterproofing sealant, a defective coating shape such as pulsations, excessive/insufficient amounts, or pooling are directly related to the quality and performance of the product. Coating inspection, however, becomes difficult after solidification or sealing is complete.
Consequently, it is important to conduct high-accuracy 100% inspection of the shape of the coated sealant and accurately detect coating defects in order to prevent the release of defective products.
Reference example: Waterproof device sealant shape measurement
Functionalization and surface processing in smartphone and tablet manufacturing
One of the major features of smartphones and tablets is the touch panel, a high-quality display with intuitive operation. During touch panel manufacturing, coating is used in many processes for adding functionalization and for surface processing.
Example of coating in touch panel manufacturing
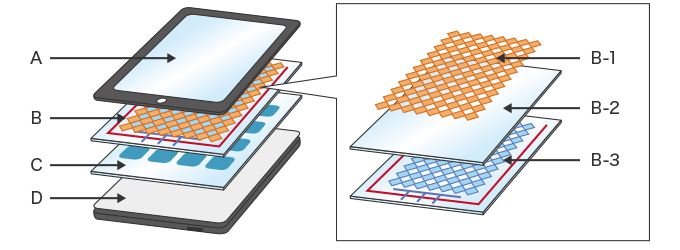
- A. Cover glass
- B. Touch sensor
- C. LCD panel
- D. Case
- B-1. ITO pattern (X axis)
- B-2. Insulation layer
- B-3. ITO pattern (Y axis)
- Cover glass (A)
-
- Various coating layers: Anti-reflection film, anti-smear/anti-fingerprint film, anti-scratch film (hard coat)
- Glass frame decoration (screen printing)
- Touch sensor (B)
-
- ITO film pattern forming: Resist coating, patterning by screen printing (such as transparent electrode pattern printing using silver nanowire ink), surface coating
- LCD panel (C)
-
- TFT (array) process: Glass surface processing, resist coating, alignment film coating
- Color filter process: Color resist coating, ITO film coating, protective film forming