Electronic Components
With the miniaturization of digital devices, electronic components are designed to be smaller and mounted at a higher density. Against such a background, more precise and finer coating is being used for adhesion and film-forming on electronic components, enabling miniaturization and higher production efficiency.
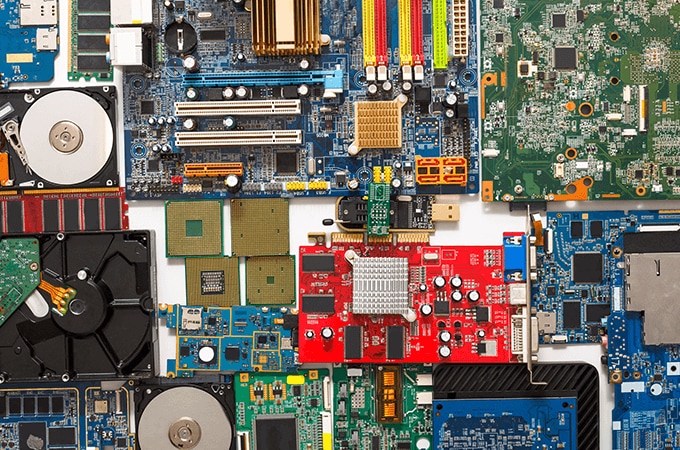
- Adhesion in electronic component manufacturing
- Functionalization and surface processing in electronic component manufacturing
Adhesion in electronic component manufacturing
With the trend toward miniaturization and higher density of electronic components, precision coating by dispensers and precision pattern coating though screen printing have been used for adhesion.
- Cream solder coating
-
- Surface mounting on PCBs: Precision pattern printing through screen printing, precision coating by dispensers
- UV curing adhesive coating
-
- Assembly of HDD and other electronic components: Small-quantity/precision coating by dispensers
- Small-quantity/precision coating of adhesive
-
- Assembly of precision modules such as compact cameras, small crystal oscillators, and CMOS sensors: Small-quantity coating of UV-curing adhesive], and bonding [Small-quantity/precision coating by dispensers
Topic: Quality control of precision coating
Despite the small quantity, cream solder or adhesive applied on small precision components have significant effects on quality and performance retention. Conventional inspection using cameras or displacement sensors suffer from incorrect detections caused by the shape or material of the target.
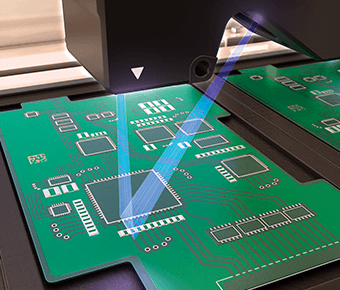
Such problems can be solved by using an inline profile measurement system equipped with a wide laser beam. This enables fast and stable measurement of coating shapes (height and volume). Even coating on the edges of precision components can be measured based on 3D shapes with no effects from the material, gloss, and shape of the target. Conducting 100% inspection immediately after coating allows quick detection of coating defects and prevents the release of defective workpieces.
Reference case: 3D shape measurement of precision coating (High-Speed 2D/3D Laser Scanner)
Functionalization and surface processing in electronic component manufacturing
In electronic component manufacturing processes, the following coating types have been used for functionalization and surface optimization.
- Underfilling
-
- Securing components on mounted PCBs and adding shock resistance (Single-component heat-curing epoxy resin): Precision coating by non-contact dispensers
- Potting
-
- Securing LEDs and other small module components and adding airtight sealing: Quantitative resin dispensing by dispensers
- Wiring patterning
-
- Forming wiring patterns on FPCs (Flexible PCBs): Screen printing, etc.
- Various coatings
-
- Adding moisture-proofing, insulation, or waterproofing to mounted PCBs and connectors: Dispensers, spray coaters, etc.
Topic: 100% inspection of small-quantity coating on small targets
The manufacturing processes of small precision electronic components require high accuracy for quantitative coating of small amounts of adhesive or for quantitative coating for potting. Because even the slightest difference in the coating amount may lead to a defective product, 100% inspection is necessary after coating. Conventional displacement sensors require frequent stage movement, which affects the takt time and leads to incorrect detection caused by materials or blind spots.
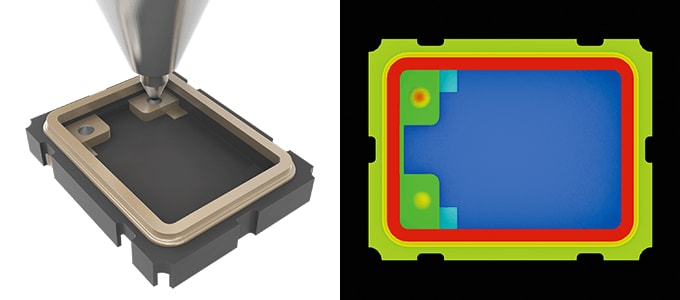
The use of a 3D Interference Measurement Sensor that measures an area instead of single points enables instant height capturing for 100% inline inspection of the accuracy of small-amount coating. Blind spots that affect conventional displacement sensors can be eliminated, and targets of different materials can be correctly detected, imaged, and measured. This ensures fast and stable measurement.