Secondary Battery
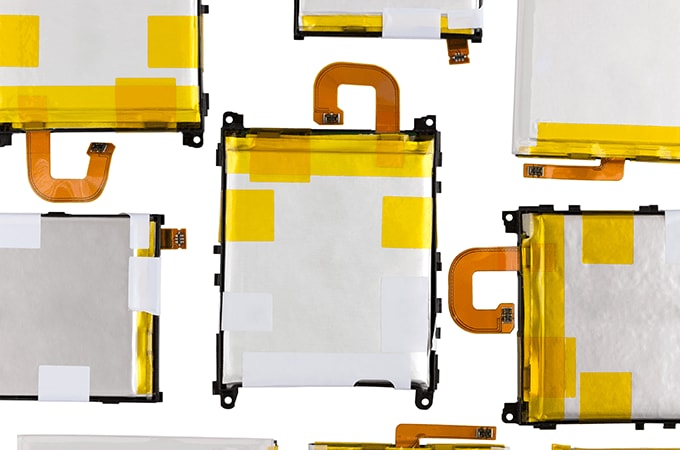
Lithium ion secondary batteries (LiBs) were invented in Japan and have become widespread all over the world. With the trend toward more compact and mobile electronic equipment, applications are ever increasing. This myriad of applications spans compact and thin-profile mobile devices, including smartphones, tablets, and laptop PCs; on-vehicle batteries for electric and hybrid-electric vehicles; and electricity storage systems for residential solar power systems and fuel cells. Consequently, research and improvements to secondary batteries have resulted in further miniaturization, higher capacities, and improved safety.
In addition, studies of all-solid-state lithium-ion batteries, in which the liquid electrolyte and separators are replaced with solid electrolyte, have been widely pursued for practical use and popularization in the future. Solid-state batteries are expected to be the next-generation battery due to their improved energy density, liquid electrolyte-free structure for less possibility of ignition, and high design flexibility. Currently, high-volume production through the use of coating is being investigated for many situations.
- Adhesion in secondary battery manufacturing
- Functionalization and surface processing in secondary battery manufacturing
Adhesion in secondary battery manufacturing
The housings of lithium-ion secondary batteries come in various shapes including cylindrical, square, and pouch (laminated) depending on the final use. The manufacturing processes also vary for each type. Laminated cells contain a layered electrode (layered element) sealed with laminated film that consists of aluminum foil and resin film bonded with adhesive coating. The demand for laminated cells is increasing because the cells are thinner and lighter compared with metal can types, are flexible in forming, and can be discarded easily with little environmental burden.
- Adhesion in the manufacturing of laminated cells
- Lithium-ion secondary battery cells are made of a fully sealed, layered electrode (layered element) consisting of alternating layers of positive and negative electrodes with separators in between. Laminated cells are capable of high capacities despite their thin and lightweight structure. They can also suppress temperature increases during charging/discharging because of the high heat dissipation from the large surface area. Another advantage is their low manufacturing cost because they can be mass-produced using coating equipment.
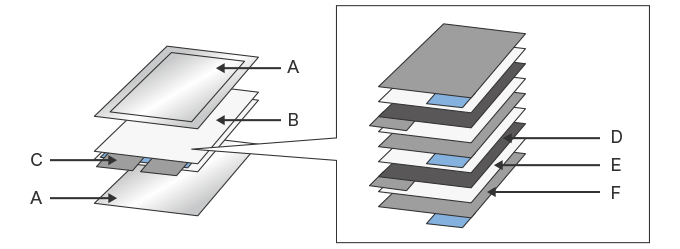
- A. Laminated film
- B. Layered electrode (Layered element)
- C. Tab
- D. Positive electrode
- E. Separator
- F. Negative electrode
The laminated film used for sealing and packing laminated cells (A in the figure above) is generally made of aluminum foil and resin film. The cells are coated with a special adhesive, bonded through lamination, and used to seal the layered electrode and electrolyte. The adhesive used for the laminated film needs to offer both high adhesion to dissimilar substrates (aluminum foil and resin film) and resistance to the strongly acidic electrolyte inside.
Functionalization and surface processing in secondary battery manufacturing
Coating is a core technology in the manufacturing process of lithium-ion secondary batteries (LiBs). Specific materials coated on the substrate function as the positive electrode (anode), negative electrode (cathode), and separator for isolating them, which combine to form the layered electrode (layered element).
Coating in the manufacturing of lithium-ion secondary batteries (LiBs)
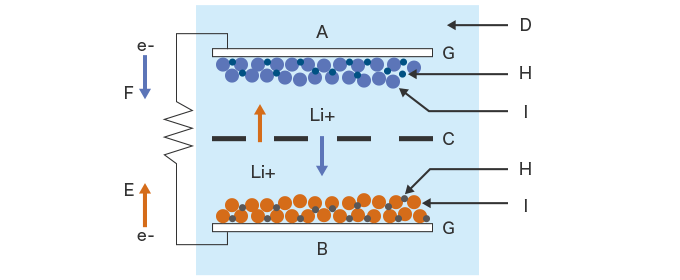
- A. Negative electrode (Cathode)
- B. Positive electrode (Anode)
- C. Separator
- D. Electrolyte
- E. Charge
- F. Discharge
- G. Current collector
- H. Binder
- I. Active material
Positive electrode (anode) coating
- Example of positive electrode slurry (solvent-based)
- An active material, conductive additive, binder, and organic solvent are mixed together to make positive electrode slurry (with organic solvent substituted for water and CMC as the thickener for water-based slurries).
- Active material: The active material to be used will have a significant effect on the capacity, voltage, and characteristics. The selection of materials (such as lithium cobalt oxide, lithium manganate oxide, or lithium iron phosphate), mixing ratios, and stirring methods vary among manufacturers.
- Conductive additive: This additive is used to reduce internal resistance, thereby improving conductivity.
- Binder: Binders are used for bonding mixed materials on the current collector foil.
- Organic solvent: This solvent promotes the mixing and stirring of the materials to adjust the viscosity of the slurry until it is appropriate for coating.
- Example of positive electrode slurry coating
- A die coater is used to coat a specific thickness of positive electrode slurry onto the aluminum foil, which works as the current collector. The thickness and weight of the electrode will have a significant effect on the energy density of the battery. Thicker coatings of film are believed to make the capacity larger and the rate characteristics lower. On the other hand, thinner coatings of film make the rate characteristics higher and the capacity smaller.
Negative electrode (cathode) coating
- Example of negative electrode slurry (solvent-based)
- An active material, binder, and organic solvent are mixed together to make negative electrode slurry (with organic solvent substituted for water and CMC as the thickener for water-based slurries).
- Active material: A highly conductive carbon material (such as black lead or lithium titanate) is used. In some case, conductive additive may also be used for the negative electrode to reduce the internal resistance. As with the positive electrode slurry, the active material to be used will have a significant effect on the capacity, voltage, and characteristics. The selection of materials, mixing ratios, and stirring methods vary among manufacturers.
- Binder: Binders are used for bonding mixed materials on the current collector foil.
- Organic solvent: This solvent promotes the mixing and stirring of the materials to adjust the viscosity of the slurry until it is appropriate for coating.
- Example of negative electrode slurry coating
- A die coater is used to coat a specific thickness of negative electrode slurry onto the copper foil. In general, the negative electrode forms a thinner coating of film than with the positive electrode. Changes in the capacity and rate characteristics according to the coating film thickness are the same as with positive electrode coating. The capacity balance between the positive and negative electrodes is also important. In many cases, when the coating film of one side becomes thicker, the coating film of the other side must also be thickened.
Separator manufacturing process
The following describes the manufacturing process of the separator, which is an important component used to isolate the positive and negative electrodes. Coating is used for adding heat resistance to the base film.
- Base film manufacturing process: The base film (a microporous membrane) is created from polyolefin material.
- Coating process: A uniform layer of aramid coating fluid (containing aramid polymer) is coated on the base film to form a heat-resistant layer.
- Slit process: The film is cut to the necessary size.
EVs (electric vehicles) and household storage batteries, which are becoming more and more popular, use laminated LiBs containing layered electrodes (layered elements).
The manufacturing process for layered electrodes uses positive and negative electrodes that have been cut into sheets for stacking. A sheet of negative electrode is placed as the outermost layer, and then the other components are stacked on it in the order of separator, positive electrode, separator, negative electrode, and so on. These stacked components are packaged with electrolyte to create a cell.
Topic: Controlling the coating quality in battery manufacturing
The coating thickness of electrode materials has a significant effect on capacity, voltage, and rate characteristics. In order to ensure mass production that satisfies the designed performance and specifications, it is necessary to ensure continuous and uniform coating to maintain the target thickness. Any problem on the coated surface, such as thickness variations or high end portions, will have a significant effect on the quality and performance of the battery product. As such, high-speed and high-accuracy inline measurement and control of coated surfaces are important.
The introduction of the Confocal Displacement Sensor— capable of high-speed and high-accuracy inline measurement—ensures stable thickness measurement and control without being affected by coarse surfaces or a material on which the laser does not reflect well.
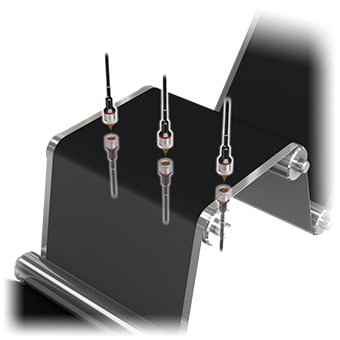
Introduction example: Coating thickness measurement of opaque materials
Coating defects including high edge portions caused by excessive edge thickness can be detected inline by using the High-Speed 2D/3D Laser Scanner, which uses a wide laser beam emitted through a slit to measure shapes.
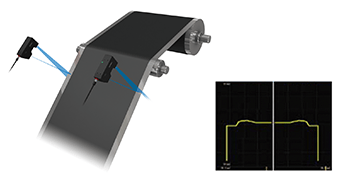