What is Cutting?
1. An Introduction to Machine Tools
Machining refers to using machines to process materials according to the specifications based on the design drawings. Machine tools are the pieces of equipment essential to achieve this. Machine tools are useful as machines that produce not only machines but also machine tools themselves.
With the progression of the digitization of machine tools, high-performance manufacturing may seem within reach for any manufacturer through the introduction of machine tools, but this is not always the case. In addition to simply introducing machine tools, manufacturers have employed creative use of machine tools, making their own tools and jigs, including tool bits (cutting tools), and developing original techniques. These efforts are still crucial today even with drastic increases and improvement in NC (numerical control) and CNC (computerized numerical control).
It is often said on the work floors that even the most advanced machine tools “have a uniqueness in each model.” Operators fine-tune the parameters according to the individual characteristics of the machine tool to constantly achieve precision cutting. In conclusion, when using machine tools, it is crucial to be versed in the characteristics of the machines and to be creative in order to fully utilize the machines’ potential based on the understanding of the individual qualities.
Moreover, knowing about machine tool on their own does not make one an excellent engineer. The knowledge of the origin of machine tools―how line marking, cutting, bending, and filing are done manually―also leads to work excellence.
- Machine No. 1 has slight operation errors.
- Machine No. 2 is in the best condition.
- Machine No. 3’s grinding is not perfect.
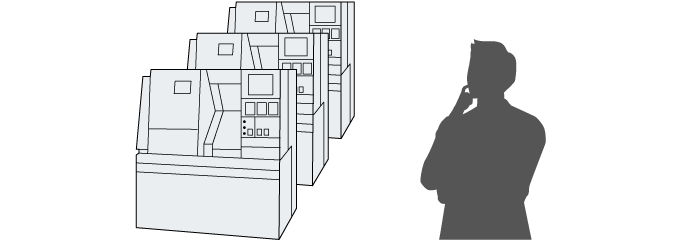
in addition to knowing its functions and performance, produces good machining.
2. Cutting Precision Factors
[1] Stiffness
When an object is subjected to a force, the shape attempts to change while also generating a force to resist this change. This property is called stiffness. For machine tools, the stiffness is the key to successful machining with the desired accuracy. While today’s machine tools are capable of progressively meeting stiffness requirements, in cases where micron-order precision is necessary, operators need a deeper understanding of stiffness.
Stiffness can be categorized into two types, static stiffness and dynamic stiffness. Static stiffness, explained as simply as possible, is stiffness when the direction and magnitude of the force are constant. With machine tools, the moving part is not moving on the table.Strictly speaking, the table is deformed by the weight of the moving part. While the actual impact is extremely small, in some cases the machining precision may decrease.
On the other hand, dynamic stiffness is stiffness when the direction and magnitude of the force varies. For example, vibration occurs when turning on the machine tool, which may cause some machine tools to chatter or otherwise vibrate in a way that affects the machining precision. When cutting or machining workpieces in any other way, both static and dynamic stiffness are key factors to consider.
[2] Thermal deformation
Objects expand with increases in temperature. Metals are no exception to this law, and to accurately measure length, the measuring room must be completely temperature-regulated.
In machining, operators need to take particular care to prevent thermal deformation in workpieces. This is because machine tool components generate heat when the machine tool is in operation, increasing the temperature of the workpieces being cut. Thermal deformation becomes a greater consideration as the machine tool continues to operate. Therefore, it is important to know the temperatures at different points of an operation in order to ensure precision machining.
vibrations and heat that can affect machining precision.
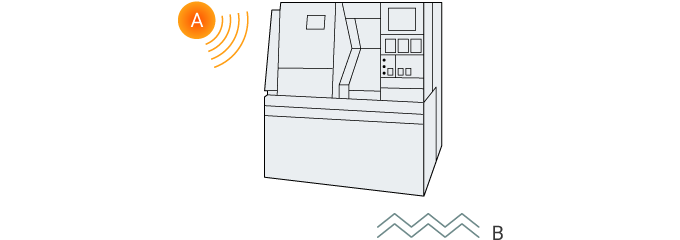
- A
- Heat
- B
- Vibration
3. Cutting Basics
[1] Cutting movements
Cutting means to cut off parts from workpieces using a tool. Broadly defined, two movements—cutting and feeding—are required in machining.
Cutting is the movement that cuts off parts from the workpiece, and generally is achieved by a cutting tool moving in a straight line.
Feeding, on the other hand, is the movement that enables cutting of other parts by moving the cutting tool. For example, after cutting on one line, by feeding the cutting tool perpendicularly to the cutting direction, a new surface can be cut. Repeating this can create a plane.
[2] Machining and deflection
When machining, the tool and workpiece come into contact and their forces interfere with each other, generating deflection. It must be noted that the generated deflection varies according to the tool being used.
For example, when using a cutting tool, the deflection depends on such factors as the material of the workpiece, the area of the cut end, and the type of cutting tool being used. In particular, the area of the cut end affects deflection significantly, which should be noted when machining.
When it comes to drilling, the operator must also consider deflection for torque and feeding. Torque is the strength of torsion and is also called the torsional moment. On the other hand, feed is the movement in the direction of moving the drill forward.
In drilling, the value of deflection varies depending on the material of the workpiece, drill type (shape of the blade), rotational speed of the drill, and feed speed.
The quality, efficiency, and durability of tools can be improved by planning machining on the work floor with influences of deflection in mind.
[3] Machining and speed
On the machining work floor, work efficiency is another key element alongside quality control. Speeding up machining improves efficiency.
However, increasing the speed of the machine requires additional planning due to the risk of increased deflection and thermal deformation caused by higher speeds. Increasing machining speed can also shorten the life of tool bits. This can shorten the replacement cycle of tool bits and consequently increase the cost per machining unit. Therefore, it is important to consider the speed, precision, and the life of tools when machining.
[4] Machining and temperature
As mentioned above in the sections about deflection and speed, the contact between the tool and workpiece during cutting and other machining generates heat. This causes the temperature of the workpiece to rise, which can result in machining precision being affected and/or the durability of tools being reduced.
The most influential factors of this are the machining speed and the area being machined. The higher the machining speed, the more heat will be generated. Likewise, a larger area being machined increases friction and consequently causes a larger temperature rise. It is important to constantly be aware of temperature changes while machining.
The cutting oil (cutting agent) plays an important part in temperature control during machining. The oil reduces friction between the tool and the workpiece. It is also essential for minimizing heat generation during machining and rinsing away chips.
Oil-soluble cutting oil was mainstream in the past, but with today’s growing awareness for environmental conservation, water-soluble types are currently more common. Because machining uses a large amount of cutting oil, the oil is often reused through a circulating system that filters the oil.
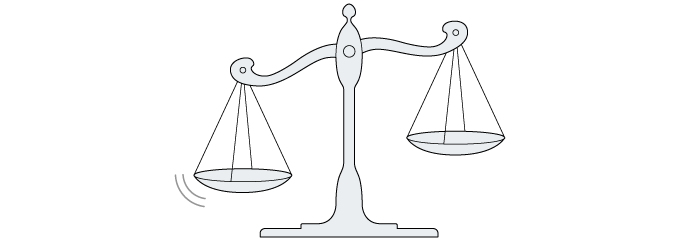