What is Injection Molding?
1. Overview and Characteristics
Injection molding is a forming process using molds. Materials such as synthetic resins (plastics) are heated and melted, and then sent to the mold where they are cooled to form the designed shape. Due to the resemblance to the process of injecting fluids using a syringe, this process is called injection molding. The flow of the process is as follows: Materials are melted and poured into the mold, where they harden, and then the products are taken out and finished.
With injection molding, diversely shaped parts, including those with complex shapes, can be continuously and quickly manufactured in large volumes. Therefore, injection molding is used to manufacture commodities and products in a wide range of industries.
2. Injection Molding Machines
Injection molding machines come in different types, such as motorized machines driven by servo motors, hydraulic machines driven by hydraulic motors, and hybrid machines driven by a combination of a servo motor and a hydraulic motor. The structure of an injection molding machine can be briefly summarized as consisting of an injection unit that sends the melted materials into the mold, and a clamping unit that operates the mold.
In recent years, the use of CNC has been increasingly adopted in injection molding machines, giving rise to the popularity of models that enable high-speed injection under programmed control. On the other hand, a number of specialized machines, such as models that form the light guide plates for LCD monitors, are also used.
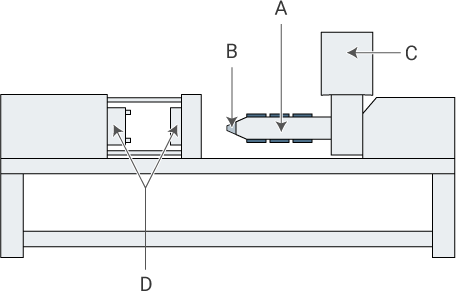
- A
- Cylinder (heats the material)
- B
- Nozzle (injects the melted material)
- C
- Hopper (material feeder)
- D
- Mold (material is poured into the mold cavity between two plates)
3. Injection Molding Process
Injection molding begins with resin pellets (granules) being poured into the hopper, the entry point for the material. The pellets are then heated and melted inside the cylinder in preparation for injection. The material is then forced through the nozzle of the injection unit before being delivered through a channel in the mold called a sprue and then through branched runners into the mold cavity. After the material cools and hardens, the mold opens, and the molded part is ejected from the mold. To finish the molded part, the sprue and runner are trimmed from the part.
It is important that the melted material is evenly delivered throughout the mold as often times there is more than one cavity within the mold allowing for the production of more than one part at a time. Therefore, the mold shape should be designed in a way that ensures this, such as by having runners of the same dimensions.
While injection molding is suitable for mass production, it is essential to have a good understanding of the various conditions required to produce high-precision products, which include the selection of resin material, the processing precision of the mold, and the temperature and speed of the melt injection.
Nozzle for injecting melted material
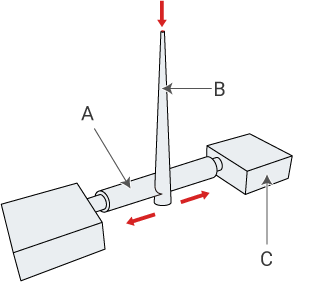
After forming, the runners are trimmed from the molded part to complete the process.
- A
- Runner
- B
- Sprue
- C
- Mold