Machine Presses, Hydraulic Presses, and Punch Presses
1. Overview
In plastic forming, presses play a central role in forming materials with applied pressure. Using dies makes it possible to manufacture products with complex shapes in a short time and in large volumes. Additionally, the ability to automate rolled sheet metal processing through continuous press operation has resulted in widespread use in a broad range of metalworking sites.
Pressure applied from above
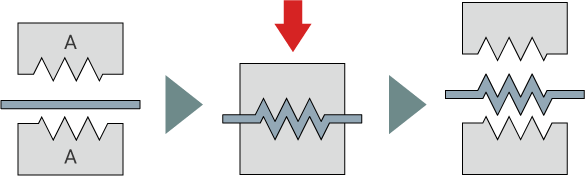
2. Machine Presses
Today, most production sites use machine presses. This is due to the advantages of quick processing and relatively easy maintenance. As automation continues to grow in processing, machine presses are a vital tool in mass producing metal parts. Also, unlike hydraulic presses, machine presses have the benefit of being free of fluid leakage.
Machine presses have several model groups based on the slide mechanism of the pressurizing unit. The most commonly used type is the crank mechanism, where the rotational motion of the motor is translated into vertical reciprocation motion by means of a crank. Other designs include knuckle presses, which feature enhanced pressurization by adding a knuckle joint to the crank mechanism, and link presses, which provide improved productivity over crank machines.
3. Hydraulic Presses
A hydraulic press pumps fluid into a cylinder and uses the resulting compressive force for forming. Hydraulic pressure control provides characteristic flexibility in the plastic forming process. Another advantage is the ability to create long workpieces. As a typical example of a current hydraulic press, hydraulic press brakes are able to adjust the applied force according to the material and thickness of the workpiece.
Conventional hydraulic presses mostly used water as the confined fluid, but as industries grew, oil-based hydraulic presses became the standard. Recent advancements in (computerized) numerical control have also enabled high-speed, high-accuracy stamping under digital control.
The benefits of water-based hydraulic presses include the fluid itself being non-flammable, the relatively ease of maintenance, and low running costs. Large hydraulic presses are also capable of compressive forces in the tens of thousands of tons.
Meanwhile, compared with water-based presses, oil-based hydraulic presses allow for finer control, enabling higher precision forming. The metal components used in oil-based hydraulic presses are also not prone to rust as water is not used. Currently, oil-based hydraulic presses are more widely used than their water-based counterparts
4. Punch Presses
Punching is a forming process where holes or shapes are made in sheet metal using a tool or a die. Punch presses are commonly used for punching processes. The punch force is in the several tens of tons class and is primarily used to form sheet materials.
Punch presses that punch out sheet material with dies attached to a tool holder—called a turret—is known as a turret punch press.
Pressure
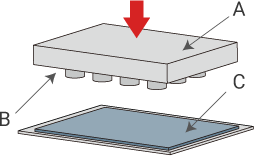
- A
- Holder with dies attached
- B
- Dies (molds)
- C
- Sheet workpiece
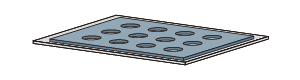