NC Lathes
1. Major Functions and Characteristics
Numerically controlled (NC) machine tools have drastically advanced metalworking since their emergence in the 1950s. Operations previously performed by hand could now be automated with NC machine tools. Not long after their emergence, NC machine tools began to be embedded with computers, a technical evolution that led to the adoption of the name CNC (Computer Numerical Control) machine tool.
Notably, NC lathes were originally developed at a Japanese university in the late 1950’s. Afterwards, existing lathes were commonly equipped with servo mechanisms, and both of these developments showcased and resulted in a significant evolution of the lathe up to the present day.
A lathe is a machine tool that rotates a cylindrical material and cuts off unnecessary parts by putting a tool bit (cutting tool) against it. Besides turning using a basic right-cut tool, other lathe methods include drilling, boring, grooving, and threading.
An NC lathe by comparison can selectively use several dozen types of tool bits in a preset procedure on numerical control-based automated machining. Not only does this make it possible to control the precise cutting or other machining positions through the use of a triaxial coordinate system, but it is also possible to achieve flexible machining by controlling the rotational speed and tool feed speed according to the material of the workpiece and the desired shape.
2. Common Types of NC Lathes
When machining with a lathe, various shapes can be created by using different types of cutting tools, such as basic right-cut tool bits, parting tools, and boring tools. The ability to use a set of tools continuously used without changeover can improve machining efficiency as well as prevent deterioration in machining precision that might otherwise occur when changing the orientation of the workpiece or exchanging different tool bits.
Mainstream NC lathes are generally equipped with a turret―a rotating unit with multiple mounted tool bits―that rotates to enable machining using different cutting tools. This enables a seamless transition from one completed process to the next while holding the workpiece chucked in position.
A multi-spindle automatic lathe has more than one spindle, which makes it capable of operating different processes at the same time, giving it the characteristic of high production efficiency. In contrast, a single-spindle automatic lathe is suitable for continuous machining of a single process. Such lathes have an autoloader that loads workpieces automatically and can manufacture same-shaped products in large volume. Other special machine tools include face lathes and vertical lathes for large workpieces, and wheel lathes for machining railroad car wheels.
3. Evolution of NC Lathes
Today, NC lathes have become so computerized that there is little to no distinction between NC lathes and CNC lathes. With the goal of ever greater production efficiency, models equipped with multiple spindles and turrets capable of machining several dimensions at a time with a single chucking are becoming common.
At the same time, precision is also improving thanks to high-precision lathes that support submicron-order machining, commonly used for precision machining in the electronic device industry. Additionally, the automation of peripheral functions such as feeding, delivery, washing, and measuring of workpieces also significantly contributes to streamlined manufacturing.
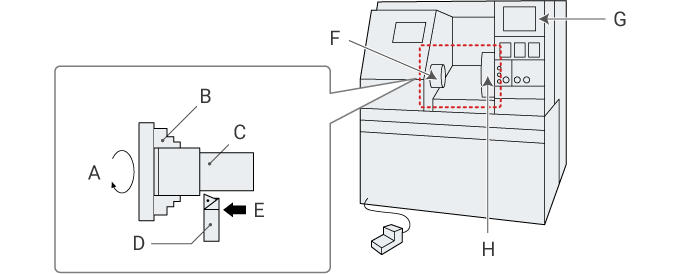
- A
- Spindle rotation
- B
- Chuck
- C
- Workpiece
- D
- Tool bit
- E
- Turning
- F
- Spindle
A chuck restrains the workpiece. - G
- Control panel
- H
- Turret
Holds a number of tools.