Vision Examples in the Food and Pharmaceutical Industries
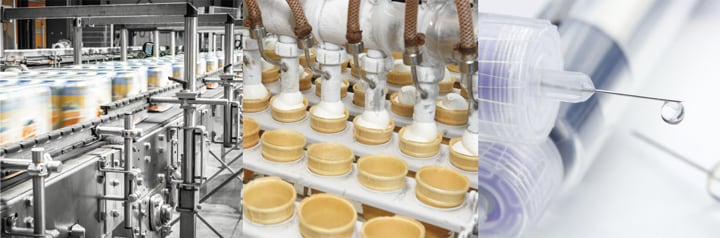
Type and orientation inspections of beverage cartons
Detect beverage cartons in the incorrect orientation or of different types in a cardboard box. The conventional method used multiple machine vision, and adjustment for changeover required a large number of man-hours. Monochrome cameras could not be used for inspection of the products with small brightness difference from the cardboard box.
The XG-X/CV-X Series supports the use of ultra high-pixel color cameras with 21 megapixels to achieve both inspection accuracy and a wide field of view. Consequently, a single camera can cover the inspection of large areas, which greatly reduces the amount of man-hours required for adjustment at changeover. The system includes a newly-developed color extraction engine, A.C.E, which uses the HSV model, said to be the closest color model to the human sensory system. This achieves stable inspection of products with low relative contrast.
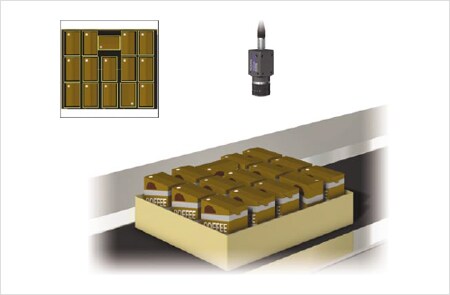
Inspection of bottle caps
Inspect bottle caps for different types. Visual inspection was commonly used and oversight could not be prevented. As this was a high-speed production line producing a great volume of products, it required multiple inspectors on the line.
Introduction of machine vision allows 100% inspection even for high-speed lines. This prevents the outflow of defective products and reduces costs for addressing customer complaints.
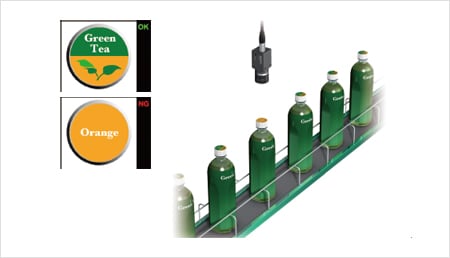
Counting medicine packets
Count the number of medicine packets in a package box. Conventional machine vision could not detect packets accurately due to the low contrast with the background.
With the XG-X/CV-X Series, you can apply the Blur filter, Shading Correction and Contrast Conversion to the packet edges that have low contrast with the background to reliably count the packet edges only.
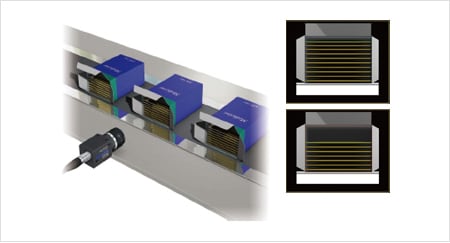
Liquid surface inspection of ampules
Check the height of liquid surfaces in ampules. Conventionally, visual inspection was performed by dedicated inspection personnel, which took time and was not consistently accurate.
The introduction of machine vision allows automation of the inspection. 100% inspection using machine vision ensures stable accuracy, and the inspection time can be reduced to improve processing time.
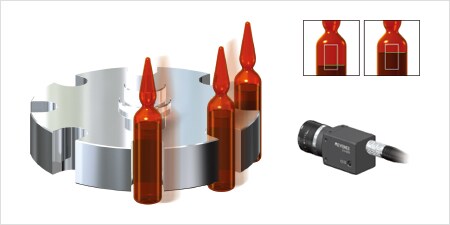
Detecting contents coming out of instant food containers
Detect ingredients or packets coming out of instant food containers. Conventional machine vision could not detect packets coming out of containers because of the limited inspection range.
The XG-X/CV-X Series offers a selection of cameras from 0.31 to 21 megapixel models to fit any inspection range. This ensures reliable detection of the ingredients or packets coming out of containers.
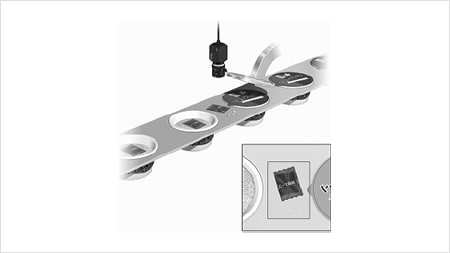
Inspecting package inserts and missing products
Inspect the presence of package inserts and check for missing products in package boxes. Photoelectric sensors were used conventionally, but the inspection was not accurate when the package insert or box was positioned differently.
The introduction of machine vision enables accurate inspection of package inserts and missing products regardless of their positions. The XG-X/CV-X Series offers a selection of cameras from 0.31 to 21 megapixel models to fit any inspection range. This enables inspection over a wide area.

Checking dairy products for defects
Inspect the packages of dairy products for defects such as marked characters. Conventional methods could not detect markings and patterns accurately due to the reflection of the background color.
Color cameras allow high-accuracy identification of marking and product types, resulting in stable inspection.
The XG-X/CV-X Series supports a variety of color cameras. You can select the optimum camera based on the number of pixels, specifications, and transfer time to match the inspection details.
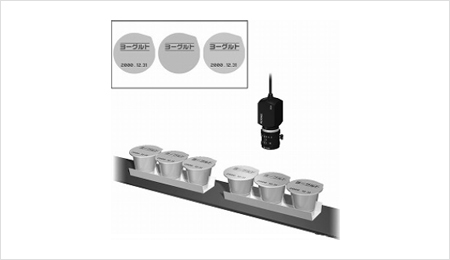
Checking for the presence of campaign stickers on beverage cans
Inspect the attachment of campaign stickers. These stickers are used during campaigns only, so the settings require extra work. Conventional machine vision could not detect deviation in position or orientation and sometimes caused the outflow of products without stickers.
Color cameras can accurately detect not only the presence of stickers but also their positions and angles. Color registration enables simultaneous detection of various defects, including upside-down attachment, tilt and different types. The XG-X/CV-X Series supports a variety of color cameras. You can select the optimum camera based on the number of pixels, specifications, and transfer time to match the inspection details.
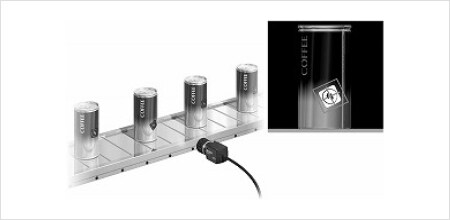
Inspecting the number of pills
Inspect finished blister packs for missing pills. The conventional method using machine vision could not count accurately due to the influence of the background.
Using a color camera and the Color Extraction function allows counting pills unaffected by the background. The XG-X/CV-X Series supports a variety of color cameras. You can select the optimum camera based on the number of pixels, specifications, and transfer time to match the inspection details.
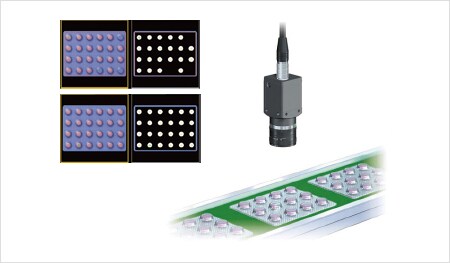
Inspecting the mixing of different types of beverage bottles
Using machine vision, check for mixing of different type beverage bottles. Visual inspection was commonly used, which costs a lot of labor and time. Sometimes different types were overlooked due to human error.
Using machine vision allows fully automated inspection. It also makes the inspection much faster and reduces labor costs and time significantly. The XG-X/CV-X Series offers high-accuracy color differentiation and high-accuracy profile judgment functions to allow reliable inspection of label conditions, including color, shape, and position, to prevent mixing of different products.
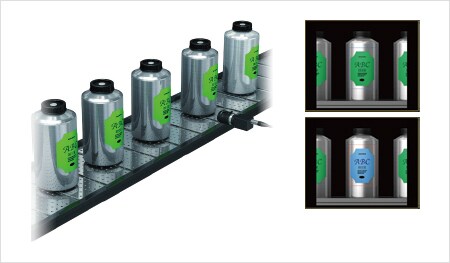
Reading inspection of barcodes on beverage cartons
Read barcodes marked on beverage cartons. Barcode readers or handheld mobile computers were generally used, but this solution did not provide the ability to read character information such as best-before date simultaneously.
Machine vision can read barcodes and character information simultaneously for collective management. This prevents mixing of different types or expired products and ensures traceability.
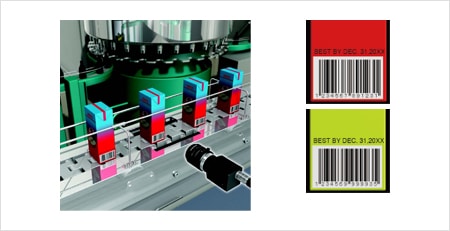
Inspecting the marking on chemical packages
Inspect the marking on chemical packages. Conventional machine vision caused frequent misjudgment due to the influence of the gloss (glare) from transparent films. The yield rate was low and disposal costs were high.
The XG-X/CV-X Series can cancel the influence of gloss (glare) to ensure stable detection. This improves the yield rate and significantly reduces disposal costs for defective products.
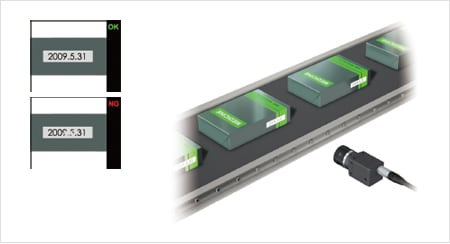
Checking the marking on aluminum packages
Inspect the marking on aluminum packages. Conventional machine vision caused misjudgment due to the influence of the glare that occurred on the aluminum surface.
Selecting machine vision and proper lighting to remove glare enables accurate identification of the marking on aluminum packages.
The XG-X/CV-X Series is equipped with KEYENCE's original LumiTrax function to conduct stable inspection without being affected by reflections or shadows.
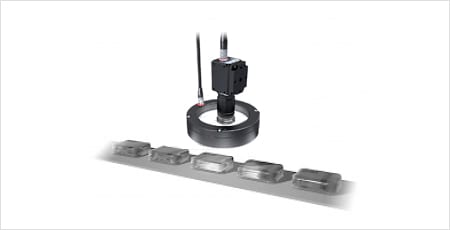
Inspecting marking on retort pouch packages
Inspect marking on retort pouch packages. Conventional machine vision could not detect characters on glossy targets of indefinite shape. The inspection of retort pouch packages suffered from misjudgment.
The XG-X/CV-X Series supports a variety of lights and image processing technologies to enable accurate detection of characters marked on reflective materials with indefinite shapes, such as retort pouch packages. The system can quickly address changes in characters and accurately recognize subtle changes such as fading.
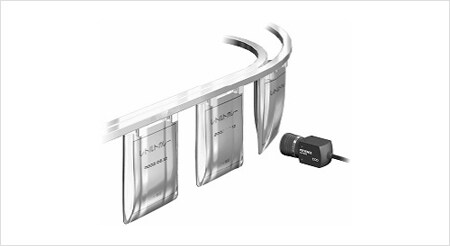
Inspecting inkjet markings
Evaluate markings made by an inkjet printer. Conventional machine vision may cause misjudgment depending on the marking target due to the influence of the shape or reflectivity of the material surface.
The XG-X/CV-X Series can accurately recognize marking defects such as distorted or faded characters due to the influence of electrostatic charge.
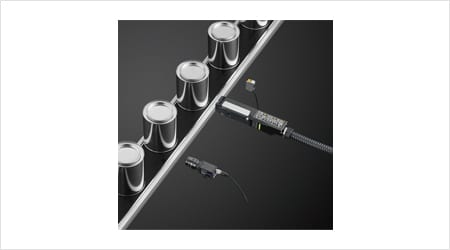
Inspecting for loose caps
Using machine vision, detect loose caps attached to eye drop bottles. Conventional image processing systems could only connect up to two cameras. Defective products were sometimes overlooked depending on the loose section of the cap. Another problem was short takt time. Even with multiple cameras, image processing could not keep up with the line speed.
The XG-X/CV-X Series can connect up to four cameras. The largest number of cores in the industry and advanced parallel processing allow the system to be used for high-speed lines. Detection is stable even when the line requires short takt time.
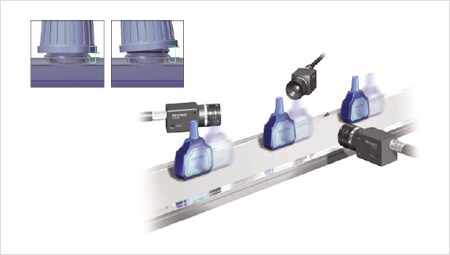
Inspecting the filling level of PET bottles
Inspect the level of liquid in PET bottles. Conventional methods used photoelectric sensors. The detection was unstable due to the influence of bubbles.
The XG-X/CV-X Series can use image processing to accurately detect the border between bubbles and liquid to determine the level.
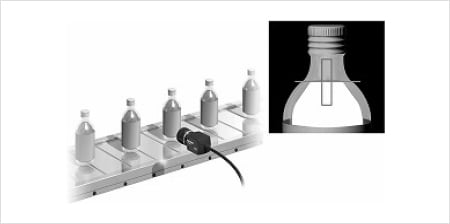
Checking the liquid level in glass bottles
Inspect the level of liquid filling glass bottles. Glass bottles may vary in volume, so some appear to have less (or more) content even when they are filled with the same amount of liquid. The level of the liquid therefore needed to be inspected visually in the final process, which required labor costs and time.
Using machine vision for the inspection of the liquid level allows judgment based on the visual amount instead of the filling amount. Even if the filling amount is the same, an extremely low liquid level may lead to customer complaints in stores. Liquid level inspection can prevent these problems from occurring.
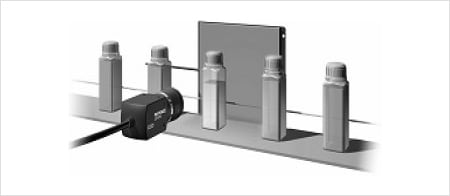
Inspecting for stains on the bottoms of cans
Detect foreign particles or stains adhering to the bottoms of cans. Conventional machine vision could not stably detect foreign particles only, due to the influence of lighting unevenness and color irregularity.
Real-time Image Extraction processing by the XG-X/CV-X Series allows reliable detection of minute foreign particles only. Contrast View Display enables intuitive differentiation by visualizing the intensity differences between defects and their surroundings with color coding between blue and red.
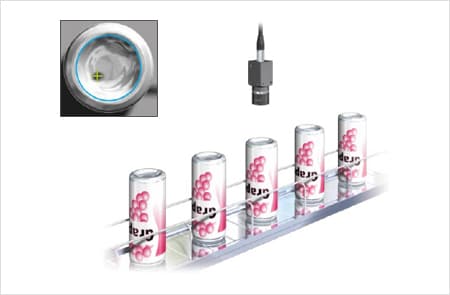
Inspecting resin caps for burrs
Detect burrs and sink marks generated on resin caps. The inspection conventionally relied on visual checking and oversight could not be fully prevented.
The Trend edge stain mode of the XG-X/CV-X Series ensures reliable detection of defects on a free curve, including those that look like the brim of a cap.
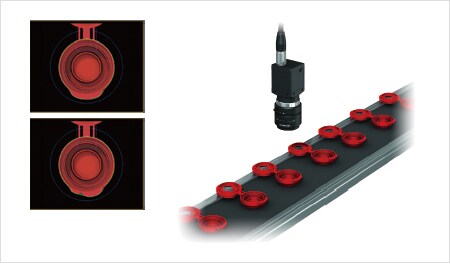
Inspecting for chipping of bottle mouths
Inspect the mouths of glass bottles for chipping. Conventional machine vision could not inspect minute defects such as chipping, resulting in misjudgment.
The XG-X/CV-X Series provides image enhance filters, including Shading Correction and Contrast Conversion, to ensure reliable detection of the change in shade. The system can recognize chipping of glass bottles generated during manufacturing and prevent the chips from entering products and leakage of contents after shipment.
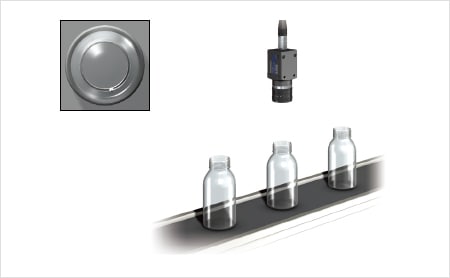
Detecting stains and foreign particles on pills
Detect stains and foreign particles adhering to pills. Monochrome cameras could not detect stains of colors similar to the background. Another problem was that the resolution was too low to recognize minute foreign particles.
The XG-X/CV-X Series supports color cameras to allow more accurate recognition of stains and foreign particles through color differentiation. The system offers a selection of cameras from 0.31 to 21 megapixel models to suit the inspection items. This ensures reliable recognition of even minute changes. Accurate detection of stains, foreign particles, oil adhesion, deformation and misalignment will prevent the outflow of defective products and reduce the costs for addressing customer complaints.
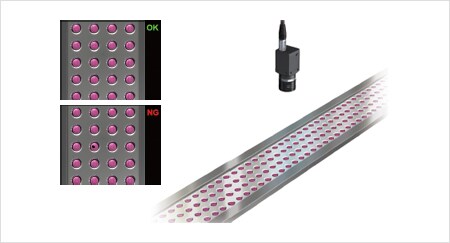
Detecting pinholes in aluminum packages
Detect pinholes in aluminum packages. Visual inspection was performed conventionally, which costs a lot of labor and time.
The introduction of machine vision allows automatic detection of pinholes and tears in the aluminum sheet used for caps and packages. The XG-X/CV-X Series can reliably detect minute changes such as pinholes by using the Shading Correction or Blur filter. This prevents the outflow of defective products. Automated inspection is effective for reducing labor costs and man-hours.
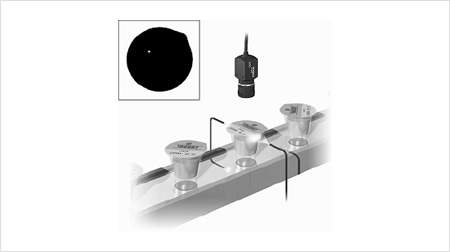
Detecting defective heat sealing
Detect pinholes and other defects generated during heat sealing. Visual inspection was performed conventionally, but judgment was difficult and sometimes caused the outflow of defective products.
Machine vision can identify pinholes, wrinkles and defective cutting. The XG-X/CV-X Series supports a high-pixel camera with 21 megapixels. It can capture an entire image from a distance to achieve comprehensive inspection, checking that the target is in the specified position, that the cutter is positioned properly, and identifying minute defects. Long distance inspection increases the flexibility of installation.

Detecting peeling of medicine container lids
Detect peeling of the lids of medicine containers. Conventional machine vision could not recognize the defect depending on the position of the peeling.
The XG-X/CV-X Series offers a wide range of cameras from 0.31 to 21 megapixel models to suit any inspection range. Inspection is stable regardless of the position of peeling of the lid and reliably prevents the outflow of defective products.
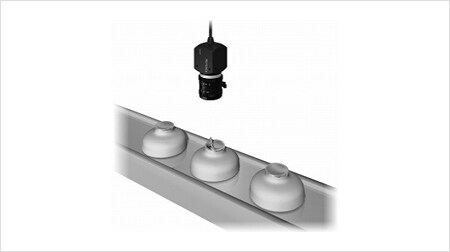
Detecting peeling/presence of sealing stickers
Using machine vision, detect the presence or peeling of sealing stickers. Conventional monochrome cameras could not differentiate product types and required a lot of labor for changeover.
Color differentiation by the XG-X/CV-X Series allows accurate differentiation of product types as well as peeling/presence inspection. Even when the color of the sticker is changed, the settings can be changed with the press of a button. This greatly reduces the labor for changeover and is effective for productivity improvement.

Composite inspection of dressing containers
The cap and label of dressing containers can be inspected simultaneously. Conventionally, the cap and label were inspected separately, which made the inspection process a bottleneck.
The XG-X/CV-X Series supports both a 21 megapixel camera and high-speed processing. This allows multiple inspections to be performed at high speed and improves production efficiency. The Position Correction function ensures stable inspection even when the target is misaligned, so the system can be used for high-speed lines.
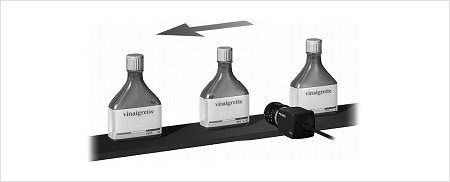
Detecting crushed PET bottles
Detect crush damage on the sides of PET bottles. Conventional image processing systems could not recognize changes with low contrast such as crushing.
Installing machine vision in a star wheel transfer process to detect crushed bottles improves work efficiency. The XG-X/CV-X Series provides various processing functions to ensure reliable 100% inspection even for crushing, for which differentiation was difficult with conventional methods.
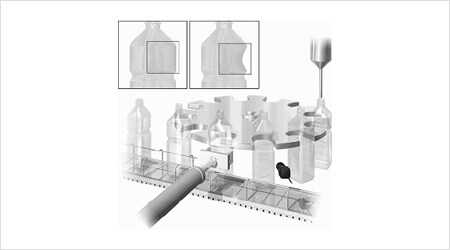
Detecting PET bottles with crushed corners
Detect crushing at the corners of PET bottles. Conventionally, the differentiation was performed visually and overlooked damage was inevitable. Since the takt speed was fast, many inspection personnel were required.
The introduction of machine vision enables stable detection of crushing at the corners of PET bottles. The XG-X/CV-X Series is capable of high-speed processing, so the inspection is reliable, even for high-speed lines requiring fast takt speed.
