History of Machine Vision : Factory Automation (FA)
Automation has become an unavoidable trend for achieving low costs and high quality in manufacturing. From simple tasks to assembly and inspection processes that require advanced techniques, this work is rapidly being automated and productivity has come to rise to levels greater than before. In this volume, we will introduce the beginnings of automation and the role of image processing.
The Beginnings and Turning Point of Automation
To provide the necessary value and services without the bother of labor... The history of the challenge of automation stretches back to ancient times. For example, it has been said there was a vending machine that sold holy water in ancient Egypt. At the time though, it probably only attracted attention as a novelty and may not have been of much practical use.
The turning point for automation came when humanity made great strides toward automation in the industrial revolution, which began the age of mass production and mass consumption. Massive amounts of manual labor were replaced with machines, and these machines began to be actively adopted to promote efficiency with fewer mistakes in work and to save labor. These machines also freed people from severe working environments and from having to repeat menial labor, and they started to be utilized in many fields as a way to increase safety and comfort.
Automation All-Star Factory Automation
The representative example of automation in manufacturing fields is factory automation systems. Systems that automate production processes do not simply take over work from people and give it to machines. They serve a large role as management systems for increasing productivity, reducing costs, and improving quality, which is why they have become indispensable.
The utility of factory automation equipment including the sensors in machine tools and industrial robots is now spreading into areas of high difficulty that “exceed human capabilities”, one of which is image processing techniques. Image processing is the manipulation and analysis of information included in images for specific purposes. People obtain the bulk of information through their eyes and ears, but in particular, a characteristic of the image information acquired through the eyes is that the volume of information to convey something to be easily understood is overwhelmingly large.
However, methods of communicating information for humans have a long history. For image information other than spoken words, the analog age including pictures (still images) and text has continued. Passing through the age of analog images, such as wall paintings and letters, the 20th century becomes the age of digital images with the advancement of electronic devices.
Practical Utilization of Digital Image Processing
Images to convey a wide range of information with more accuracy than spoken words... Imaging techniques in factory automation systems that efficiently process and utilize digital images by a computer began being put to practical use in Japanese industry in the 1960s. This started in the fields of scientific research that included images from artificial satellites. In the 1970s imaging tests by X-rays and ultrasound were being applied in medical fields, and in industrial fields as well including industrial manufacturing and distribution. Imaging techniques were actively used for automation, promotion of efficiency, and labor saving, which came to contribute greatly to increases in quality management.
In the 1980s and on, recognition processing techniques for drawings and document images started improving dramatically. Until then, large computers had been necessary, but general-purpose image processing equipment and low cost image processing programs to process images on personal computers have become commonplace, and the practical use of now familiar image processing techniques started to take off. It’s now normal for images that used to be monochrome to be high resolution and in color, and the usability of these systems will continue increasing due to further miniaturization, speed improvements, and reductions in cost.
Advances in the Volume of Information and Quick Processing
In general, 1 second of video contains 30 frames of still images. In other words, with a simple calculation the volume of information increases 30 times, and color video triples that, for a volume of information 90 times that of a monochrome image. An image is composed of a group of small pixels divided horizontally and vertically. If you increase the number of pixels by dividing them into an even finer group, resolution of the image increases and it becomes more accurate, but the volume of information also increases by that amount.
There used to be the dilemma where the more advanced images became, the more the volume of information increased and the slower processing became. But in recent years, image processing has continued to increase in speed. So why have we been able to quickly process large volumes of information? The answer is that high speed and high resolution imaging elements (devices that convert images to electronic information) have appeared and high speed integrated circuits have been developed to process large volumes of information at high speed. There has also been a benefit in the practical utilization of high resolution displays, going from CRT monitors to thin liquid crystal panels and OLEDs, and in the dramatic increase in the performance of personal computers.
The Optimal Factory Automation System for the “Imaging Age”
A system that possesses powerful information processing and image capture capabilities unavailable until now... In the present day, where we are equipped with the techniques and environment for image processing that would have been difficult even for supercomputers a half century ago, we can surely say that this is “the Age of Imaging” where information can be communicated and shared by images “anywhere, with anyone, and at any time”.
Automatically reading printed expiration dates, product shape (external appearance, damage, surface shape), sorting and assembly linked with robots, remote sensing including agricultural/marine processing and classifying... Image processing in factory automation systems, which continues to be applied to and put to practical use in a wide variety of industrial fields, continues to steadily evolve while it is being optimized according to various applications and needs.
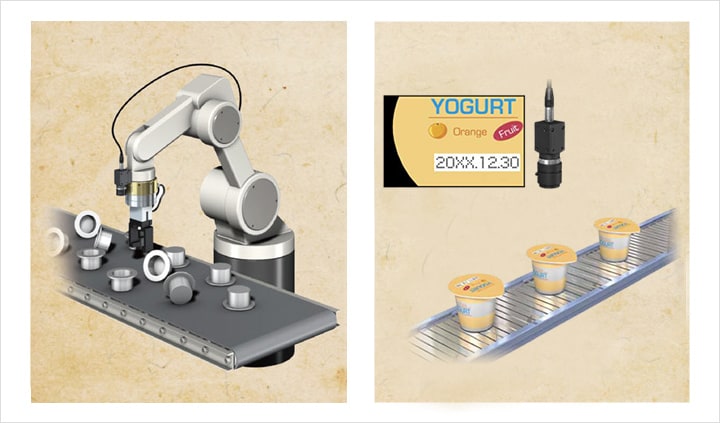
Factory Automation - Spreading Worldwide
Image processing techniques in factory automation systems are spreading their appeal worldwide. In addition to firms from leading industrialized countries moving production functions overseas, factory automation is being rapidly adopted in newly advanced economies (such as the BRICs), not just in manufacturing, but for the purpose of optimization. Optimizing of local resources included services, maintenance, and storage, and it is becoming a driving force in the expansion of demand.
Manufacturing companies are now facing an age of tumult and competition on a worldwide scale. Factory automation, which has come to support manufacturing in many ways in fields that include automobiles, industrial equipment, electronics, foods, and pharmaceuticals, has contributed to decreasing size and weight, increasing performance, and increasing quality in manufacturing industries all over the world. In the future, we anticipate new usefulness with next generation factory automation systems and increasing international competitiveness by opening up factory automation by unifying specifications for factory automation equipment and control software, creating effective links to ERP*1 and MES*2, and by establishing “smart factory automation” systems that cooperate with smart communities and smart grids to effectively utilize energy among companies and regions.
*1. Enterprise Resource Planning. An information systems package to support the core business of companies including inventory and production status.
*2. Manufacturing Execution System. Serves the role of understanding equipment and the quantities and status of raw materials and work-in-process items in real-time, assembling work schedules based on production plans, issuing instructions to workers, and providing information related to work procedures.