Industrial Robots
This page introduces network connection examples for industrial robots as well as connection examples using KEYENCE’s KV-XLE02 Ethernet unit.
- Network example
- KEYENCE Ethernet units
- Devices compatible with PROTOCOL STUDIO (Ethernet version)
- Typical connection example
Network example
Connecting an industrial robot to a network can be done using Ethernet or any other supported open network connection.
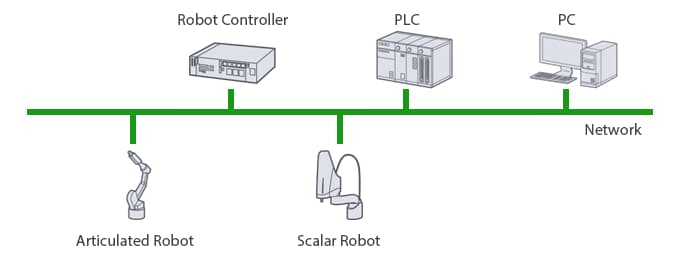
- A network-compatible unit or board is required for PLCs and PCs.
KEYENCE Ethernet units
Most industrial robots support Ethernet communication. KEYENCE’s KV-XLE02 Ethernet unit and PROTOCOL STUDIO Ethernet communication setup software make communicating with industrial robots and other equipment incredibly simple.
Ethernet UnitKV-XLE02
Hardware |
Ethernet
|
Communication speed: 1 Gbps
|
2-port
|
---|---|---|---|
Functions |
EtherNet/IP®
|
EtherCAT*1
|
CC-Link IE
Field*2 |
PROFINET*3
|
PLC link
|
PROTOCOL STUDIO
|
|
Sensor
applications |
Modbus/TCP
clients/servers |
FTP clients/
FTP servers |
|
KV socket
|
Host link
|
MC protocol/SLMP
|
|
Mail sending/receiving
|
Unit interrupt
|
Inter-unit synchronization
|
- Slave
- Intelligent device station
- Device
Supporting the creation of communication protocols for a wide range of devices PROTOCOL STUDIO
Completely ladder-less equipment communication
- Simply select the communication format and command settings in the tool.
- Automatic communication schedule adjustment within the unit
- Simple rearrangement of sending and receiving processes into flow format
- Serial communication support When used with the KV-XL202/XL402
Devices compatible with PROTOCOL STUDIO (Ethernet version)
Manufacturer | Series | Model |
---|---|---|
YASKAWA Electric Corporation
|
YRC1000/DX200/FS100
|
YRC1000/DX200/FS100
|
FANUC CORPORATION
|
R-30iB Series
|
R-30iB Series
|
Seiko Epson Corporation
|
RC700/RC90
|
RC700-A, RC90 (RC + 7.0)
|
Yamaha Motor Co., Ltd.
|
RCX340
|
RCX340
|
DENSO WAVE INCORPORATED
|
RC8
|
RC8A, RC8
|
Typical connection example
Connecting to a network makes it possible to collect and manage various information from industrial robots. This allows for real-time status monitoring and changing settings from the PLC.
The following example includes network-connected industrial robots.
Simplified PLC-based operation changes and changeovers
Utilizing Ethernet communication with industrial robots makes it possible to perform various management operations—including monitoring operation statuses and changing settings—all at once. This allows for robot teaching and changing operations from the PLC without the need for dedicated software or pendants.
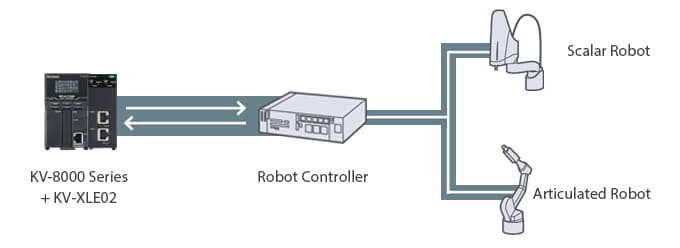