MIG welding
This page introduces MIG welding by looking at the types of MIG welding, the differences from MAG welding, and the features of the welding machines and welding methods. This page also explains the low-frequency superposition pulse welding method used in automobile and motorcycle manufacturing.
MIG (Metal Inert Gas) welding is another method of arc welding. As with TIG welding, an inert gas is used for the shielding gas, but MIG welding is a consumable electrode type of welding that uses a discharge electrode that melts during welding.
The process is generally used for joining stainless steel or aluminum alloy workpieces. An appropriate type of shielding gas must be used depending on the metal to be welded.
A coiled welding wire is used for the electrode. The coiled wire is attached to the wire feed unit and is sent automatically to the torch tip by a feed roller that is driven by an electric motor. The wire is energized when it passes through the contact tip. An arc is struck between the wire and base material, which melts the wire and base material simultaneously to weld them. During the process, the shielding gas is supplied through a nozzle into the weld area and its surroundings to shield the arc and weld pool from the atmosphere.
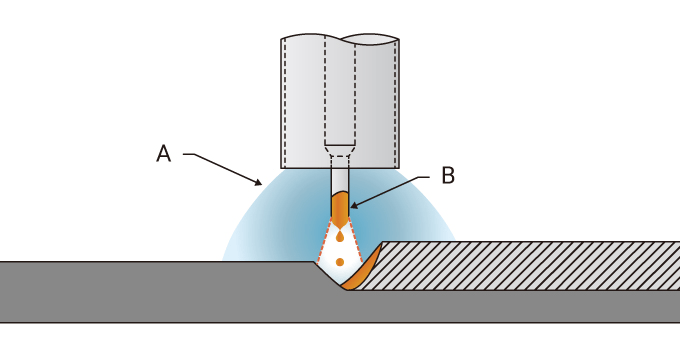
- Ar gas or
Ar + 2% O2 gas - Solid wire electrode
A semi-automatic MIG welding machine mainly consists of the following:
- Welding power supply
- Wire feed unit
- Welding torch
- Gas cylinder
The configuration is almost the same as that of a MAG welding machine, except for some improvements added to the wire feed unit. Since MIG welding is often used for welding aluminum, the wire feed unit has to be improved to allow stable feeding of soft aluminum wire (four-roll system).
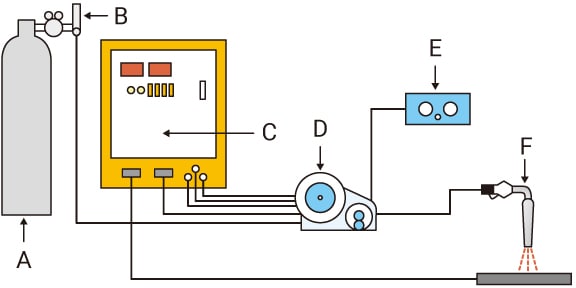
- Gas cylinder
- Gas flow controller
- Welding power supply
- Wire feed unit
- Remote controller box
- Welding torch
MIG welding can be classified according to its use of AC or DC, or a pulse or non-pulse current.
Pulse | Welding method | |
---|---|---|
Direct current (DC) | No | Short-arc MIG welding |
Spray MIG welding | ||
Large-current MIG welding | ||
Yes | Pulse MIG welding | |
Low-frequency superimposed pulse MIG welding | ||
Alternate current (AC) | Yes | AC pulse MIG welding |
Low-frequency superimposed AC pulse MIG welding | ||
DC + AC | Yes | AC/DC composite pulse MIG welding |
Short-arc MIG welding is a welding method that uses the short-circuit transfer (short arc) phenomenon. It is often used in semi-automatic systems intended for thin plates due to the low heat input to the base material. MAG welding using short arc is commonly used to weld plates of medium thickness in forced positions. In case of MIG welding, such workpieces are often welded with pulse MIG welding.
Spray MIG welding is a process that sets the welding current higher than the critical current to set a higher arc voltage. It uses the spray transfer phenomenon where the molten filler material vaporizes. When an aluminum workpiece is welded such that no spatter is generated, lack of fusion or other welding defects may result. To prevent this problem, the arc voltage must be decreased a little to allow welding in small spray transfer mode. Spray MIG welding is no longer commonly used because pulse MIG welding that can handle workpieces with low to medium thickness has become common.
Large-current MIG welding uses welding wires with thick diameters (approx. 3.2 to 5.6 mm). The welding system includes a welding torch with double-shielded gas nozzle and a constant-current characteristic power supply with a rated output current of about 1,000 A.
MIG welding using DC and pulse current is also called conventional pulse MIG welding.
The basic principle is the same as that of pulse MAG welding.
This welding method passes a small base current to maintain an arc and a pulse current exceeding the critical current alternately to allow spray droplets to transfer from the wire even when the average current drops below the critical current. They ensure effective and high-quality welding of thin to thick plates.
Low-frequency superimposed pulse MIG welding is a method developed based on pulse MIG welding to achieve high-value added welding of aluminum workpieces. Since the process can create beautiful scale-like beads, it is used to weld thin aluminum plates for automobiles or motorbikes.