Principles of laser welding
Changing the intensity and spot size of the laser beam emitted by a laser processing machine makes it possible to weld and draw letters and patterns on the surface of base materials, and to perform cutting.
Laser welding uses a laser beam that is extremely stronger than those used for other processes. This beam is used as a heat source to melt and join together base materials.
Laser beams used in laser welding
The laser beam used for welding is invisible.
The medium used for laser excitation can be either a gas or a solid object. The excited laser is focused with a lens and applied to the base material. The power and spot diameter can also be changed for processing applications other than welding.
Marking
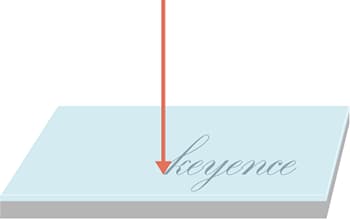
Marking is the process by which characters and patterns are engraved on the surface of various materials using a laser beam. Engraving is also possible by melting the material surface using heat.
Welding
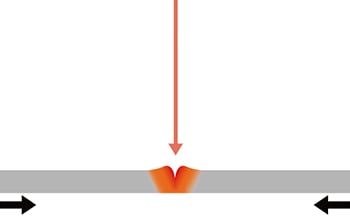
Laser welding uses a laser beam to melt and join metal materials together. Using a laser makes it possible to weld at higher speeds and with less distortion than normal welding.
With a high power output laser, high-level control of the beam convergence properties such as wavelength and energy density, and of laser beam qualities such as intensity and beam mode* are required. However, this method can be used for delicate applications in addition to joining both thick and thin plates, a strength of laser welding.
- * What is beam mode?
- Beam mode is the light intensity distribution unique to each oscillator. Beam modes include single mode (Gauss mode), multi-mode (multiple mode), and ring mode. With laser welding, single mode is effective when penetration welding is required for thick plates, and multi-mode is effective when spot welding requires a wide bead width and deep penetration is not required.
Features of laser welding
Laser beams can be focused to a very small point compared with arcs used in arc welding. Increasing the energy density using a converging lens makes it possible to use laser welding for localized welding and for joining materials with different melting points. This type of welding is also suitable for detailed welding applications thanks to reduced heat effects, a thin bead, and no generation of processing reaction forces.
- ■ Characteristic
- Because laser beams can be transmitted at atmospheric pressures, laser welding equipment does not require* a vacuum chamber like electron beam welding. The laser beam equipment in laser welding is smaller than the beam equipment in electron beam welding, and automation and precise control using a computer or robot are possible. Fibers and transmission path mirrors also make it possible to perform welding at a distance from the exciter. These advantages make laser welding highly adaptable to various applications, and the ability to utilize remote laser welding, fiber laser welding, and beam scan welding make it possible to meet a variety of welding process needs.
However, welding may be performed in a vacuum chamber with some high-power lasers, such as welding for the production of clad steel plates.
- ■ Plasma countermeasures in laser welding equipment
- Plasma (laser-induced plume) may be generated near the laser weld depending on the magnitude of the ionizing voltage of any metal or gas present in the laser irradiation area. When plasma is generated, the plasma causes laser absorption and refraction, which reduces the laser power and energy density entering the base material. This is because the absorption coefficient of the laser within the plasma is proportional to the square of the wavelength, so large changes in the state of the plasma are likely to cause welding defects.
Plasma is easily generated by metals and gases with a low ionization voltage. The ionization voltage for aluminum is about 6 V, and for iron about 7.9 V. As such, ionization due to metal vapor frequently occurs when laser welding these metals. For gases, the ionization voltage is about 15.8 V for argon and about 14.5 V for nitrogen. This means argon gas and nitrogen gas can turn into plasma during high-power CO2 (carbon dioxide) laser welding.
Helium gas, which has a high ionization voltage, is used as an assist gas to prevent this from occurring. The ionization voltage of helium gas is about 24.6 V, resulting in almost no plasma generation. Depending on the welding method, helium assist gas can be applied either from the side or from the back during welding to suppress plasma generation.
Plasma generation can also be suppressed by evacuating the weld chamber, but doing so requires vacuum equipment.
Laser welding application examples
Compared to arc welding and electron beam welding, laser welding is easier to combine with computer control and CAD/CAM. In addition to being easy to incorporate into production lines, laser welding is also suitable for use with robots. Laser welding is a high-accuracy, high-quality, high-speed, high-productivity joining method that utilizes the features of high energy density and small spots for the heat source. From large workpieces such as automobile outer panels to minute parts such as wires and pins in electronic components, laser welding is used in a wide variety of fields.
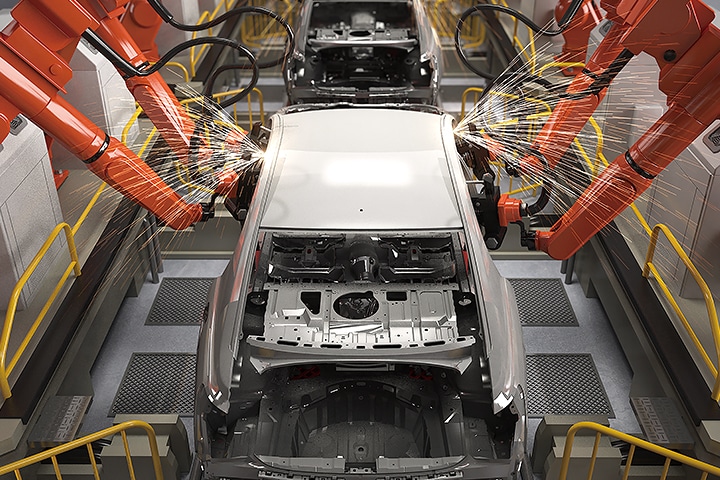

- ■ Spot welding on automobile frames/bodies
- Laser-based spot welding is done by irradiating a laser beam on one side of a base material. Unlike resistance spot welding, there is no need to sandwich the base material between electrodes. This makes it possible to perform welding on a robot arm with a high degree of freedom for use even in intricate and complicated locations.
- ■ Seam welding on automobile bodies
- Using a high-speed pulse laser or continuous wave laser makes it possible to weld in lines rather than spots. Line welding offers improved strength, and steel material for reinforcement is not required, allowing for reduced weight and higher rigidity.
- ■ Spot welding of wires/pins on electronic components
- Attaching a camera to the beam device and controlling the spot using a computer enable accurate capturing of the welding point. This makes it possible to perform detailed welding such as for wires and pins in electronic components.
- ■ Sealing and welding of ceramic packages on electronic devices
- Welding with a small amount of deformation is possible by using a continuous wave laser with a small heat input instead of a high power pulse laser. Melting a brazing material (filler wire for welding) for use also reduces spatter generation.
Automobile welding
Automobile bodies require various factors including strength, durability, rust prevention, collision energy durability, and lightness while also featuring an attractive design with high commercial value. Because of this, the thickness and materials of the steel sheets used for automobile bodies are carefully considered. Improving precision and productivity while also satisfying the performance requirements is the most important issue in automobile manufacturing.
This section introduces two methods—tailored blank welding and laser brazing welding—developed to meet these requirements. Both of these methods have had a significant impact on the welding processes for automobile bodies.
- ■ Tailored blank welding
-
The term “tailored blank” refers to a pressed material that is “tailored” for multiple purposes. Tailored blank welding is the method used to weld the materials together before press forming to form a single material.
Welding is performed before press forming.
Tailored blank welding is mainly used for manufacturing outer panels for automobile bodies.- Tailored blank method
-
-
Welding -
Punching -
Shaping
-
-
- Advantages of tailored blank welding
- With tailored blank welding, multiple steel sheets can be created into one steel sheet and press-formed all at once. This advantage reduces the number of panels required, improves body accuracy, and minimizes the overall number of parts used. Another advantage in terms of quality is the ability to make steel sheets of different materials into one material. This allows for optimum positioning of materials to satisfy various performance requirements such as reduced weight and increased rigidity.
Originally, tailored blank welding was used with TIG welding for manufacturing side panels. Today, the method is used for various manufacturing applications, including floor panels, sunroof reinforcements, side members for doors, and the inside of side panels. In addition to laser welding, tailored blank welding can also be done through mash seam welding and plasma welding depending on the material and productivity requirements.
-
- Using laser welding for tailored blank welding
- The bead created with laser welding is generally about 1 mm wide. This creates a more attractive appearance than is possible with arc welding, and heat-related material deformation can be kept to a minimum. The welded metal is also significantly hardened through rapid solidification and cooling of the molten pool due to heat conduction. This makes the structure of the weld similar to martensite before hardening, resulting in a strong bond.
However, welded parts created with the tailored blank method are prone to cracking during the press-forming process after welding. Also, welded parts that are taller than the surrounding steel sheet can damage the press die and shorten the service life. Countermeasures to prevent these problems must be utilized when performing tailored blank welding.
Such solutions include using an assist gas to prevent porosity and adjusting the welding speed to prevent undercutting. Also, depending on the material, the welded part or welded heat-affected zone (HAZ) may crack, so looking closely at the generation mechanism and the material characteristics in advance is necessary.
- * What is martensite?
- Martensite is a material formed by martensitic transformation. This transformation type refers to the change in a crystal structure caused by shearing. The result is a crystal that is smaller than the original crystal material. Martensitic transformation strengthens the bond between crystals while also increasing hardness.
- ■ Laser brazing joining
-
This joining method uses a brazing filler metal (filler wire) and a laser heat source. Laser brazing offers improved support for welding line gaps, a common drawback in laser welding.
-
- Advantages of laser brazing
- Whereas regular laser welding uses lines for joining materials, laser brazing joins material surfaces, providing excellent sealing performance. Using a brazing material with a low melting point also makes it possible to join steel sheets with no melting with twice as much joining strength as spot welding and at twice the speed.
Brazing material offers significant advantages, including shortened heating and cooling times during joining. For example, when brazing in a vacuum furnace, no material deterioration occurs when joining ceramic and metal. Laser brazing also offers significant advantages when joining aluminum and stainless steel or magnesium alloys.
-
- Using laser brazing for automobile body joining
- Steel sheets used for automobile bodies are coated with zinc to prevent rust. Laser brazing can be used to bond this coating without damaging the material. Also, joining roof panels and side panels can be done without any resin parts for connecting the panels. In terms of design, laser brazing eliminates parting lines not only between the roof panel and the side panel but also on vehicle exteriors.
Laser brazing combines high-speed joining capabilities with high rigidity, overcoming common drawbacks of laser welding. This method is ideal for use in automobile processes that require strength, durability, rust prevention, collision energy durability, and lightness in addition to beautiful design results with a high commercial value.
-