Shielded metal arc welding
This page introduces shielded metal arc welding, also known as hand welding, by looking at the features and principles of this method, which can be performed easily with inexpensive equipment.
Shielded metal arc welding (SMAW) is an example of consumable (fusible) electrode type arc welding. It uses a metal rod (shielded metal arc welding rod) made of the same material as the base material as an electrode. The arc formed between the core wire of the electrode and base material is used as a heat source. The molten metal is covered by the gas and glasslike slag generated from the shield of the core wire. The process has the advantage of being less affected by wind or other disturbances on the worksite due to shielding by the gas and slag, and to the formation of a shielding tube at the tip of the welding rod.
SMAW has been used for a long time. Since the process is most often done manually, it is also called manual arc welding. The number of applications is decreasing due to the spread of automatic or semi-automatic MAG welding machines using carbon dioxide (CO2). SMAW, however, has been used in various applications due to its advantages of quick and easy welding both indoors and outdoors with relatively inexpensive equipment.
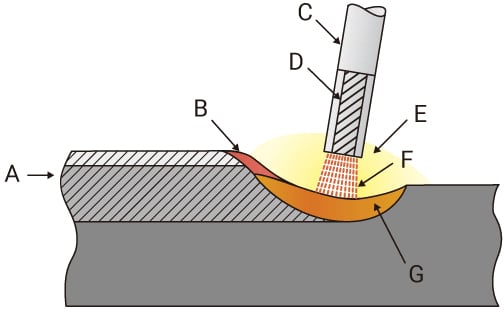
- Weld metal
- Molten slag
- Shield
- Core wire
- Gas atmosphere
- Arc
- Weld pool