Improving the yield rate is a major challenge in manufacturing, and the causes of its decline are diverse. To solve this problem, it is necessary to accurately understand the entire manufacturing process and identify the issues. In recent years, the use of 3D scanners have been attracting attention as a measure against this. KEYENCE’s 3D scanner-type three-dimensional measuring machine, the “VL Series”, scans and digitizes the 3D shape of products with high precision. This allows for detailed analysis at each stage of the manufacturing process. As a result, it is possible to quickly detect variations in quality and manufacturing problems, and swiftly implement improvements that directly lead to an increase in yield rate.
What is Yield Rate
The 'yield rate' represents the percentage of products meeting quality standards during manufacturing and suitable for market distribution. It's a vital manufacturing metric. For instance, if you input materials for 100 products and yield 95 profitable items while 5 are defective and unprofitable, the yield rate is 95%. A high yield rate leads to a reduction in manufacturing costs, an improvement in production efficiency, and an increase in corporate profits.
We’re here to provide you with more details.
Reach out today!
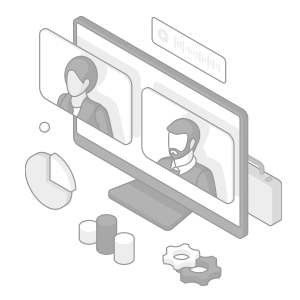
Causes and Countermeasures for Yield Rate Decline
Variations in Materials
Differences in material quality and dimensions can lead to variations in the final product's quality, despite undergoing the same process. Therefore, it's crucial to thoroughly inspect materials during procurement to identify any potential issues.
Instability in Manufacturing Process
Fluctuations and errors in the manufacturing process can cause product defects and lower the yield rate. Therefore, stabilization of the process is required.
Insufficiency in Quality Inspection
Poor quality inspections can result in losses, such as incorrectly identifying products within tolerance as non-conforming, thereby reducing the yield rate. Implementing precise inspections can mitigate losses caused by misjudgments, ultimately lowering manufacturing expenses.
Contact us to learn more about how our advanced technology can help take your business to the next level.
Contact Us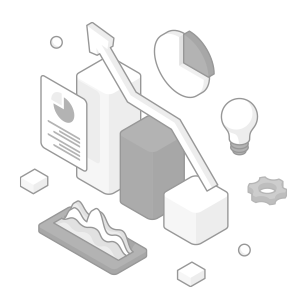
Current Challenges
Understanding the Overall Shape
With tools like calipers, the measurement becomes a point measurement at the clamped part, making it difficult to grasp the overall shape in many cases. Therefore, there is a risk of yield rate decline as accurate feedback cannot be performed without understanding the product shape and subtle dimensional differences. Delays in discovering and identifying the causes of defects, can hinder prompt corrections, thus contributing to a decline in the yield rate.
We’re here to provide you with more details.
Reach out today!
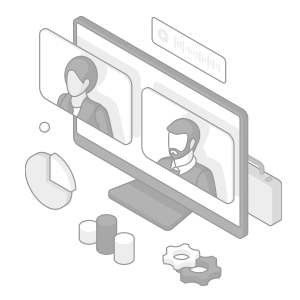
Case Studies of Solutions with the “VL Series” 3D Scanner CMM
Comparison with 3D CAD
The VL Series can scan and digitize the entire product, both front and back. It visualizes the deviation from the design value (3D CAD data) of the entire product with a color map. By grasping the overall shape trend that cannot be grasped by point measurement, you can easily provide corrective feedback. This is an approach to improve the yield rate by fundamentally improving the direct yield rate.
Automatic OK/NG Determination of Products
With the VL Series, continuous measurement of the same shape can automatically determine OK/NG. This can reduce mistakes such as judging a good product as defective due to variations in measurement by people. This allows you to check the finish without human error. It can also be used for inspections at the time of material acceptance, so you can quickly notice variations in materials that cause a decrease in yield rate and take measures.
Discover how the VL Series 3D scanner revolutionizes quality control across industries, ensuring unmatched efficiency and reliability in your measurement processes. Request a demo today!
Discover more about this product.
Click here to book your demo.
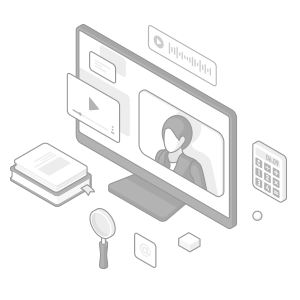
Summary
The VL Series offers 3D scanning capabilities for the entire circumference, enabling the capture of full-front and back product data. By overlaying this scan data with 3D CAD models, you can easily visualize the overall shape. This facilitates quick and accurate defect identification, enabling prompt feedback for corrections to prevent a decrease in yield rate.
Get detailed information on our products by downloading our catalog.
View Catalog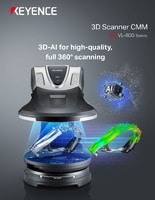
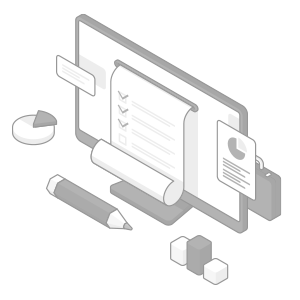
Related Downloads
Related Products
Scroll