Understanding the Role of 3D Scanning in Industrial Metrology
Industrial metrology, the science of precise measurement in manufacturing and production, plays a crucial role in ensuring the quality, consistency, and reliability of products. As industries push for greater precision and efficiency, 3D scanning technology has emerged as a transformative tool in modern industrial metrology. Today, the 3D scanner is not just a luxury but an essential instrument for quality assurance, product development, and reverse engineering across a variety of sectors.
What is 3D Scanning?
3D scanning is the process of analyzing a real-world object or environment to collect data on its shape, dimensions, and surface characteristics. This data is then used to create a highly accurate digital 3D model.
Unlike traditional measurement tools that measure single points by contacting a surface with a probe or stylus, 3D scanners capture hundreds of thousands to millions of data points within seconds, producing detailed and realistic representations. These digital models can be used for inspection, reverse engineering, digital archiving, design modification, and even virtual reality applications.
CMM measuring with probe tip
Conventional 3D scanner
The VL-800 Series 3D Scanner CMM is an easy-to-use 3D scanner that can capture high-accuracy 360⁰ degree scans of an object without the need for fixtures or reference stickers – simply place a part on the stage and press a button to get started.
Get detailed information on our products by downloading our catalog.
View Catalog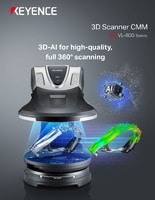
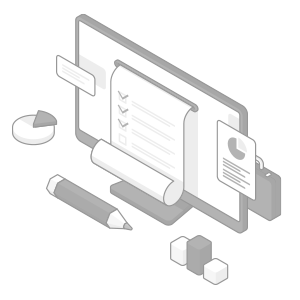
How are 3D Scanners Used in Manufacturing?
3D scanning in metrology involves using advanced optical, laser, or structured light technologies to capture accurate three-dimensional data of a physical object, often referred to as a 3D model or point cloud.
In industrial metrology, 3D scanning provides a non-contact method for capturing complex geometries, surface textures, and dimensional measurements without physically touching the part. This is particularly beneficial for delicate, intricate, or hard-to-reach components, where traditional contact measurement methods may fall short, or for objects that are difficult to measure such as those with freeform shapes.
Typical 3D scanners used in manufacturing include laser scanners, structured light scanners (SLS), and portable coordinate measuring machines (CMMs) equipped with 3D scanning probes. These devices ensure that manufacturers can quickly and accurately inspect parts, detect deviations, and maintain tight tolerances critical to performance and safety.
Here are some typical use cases for 3D scanners:
CAD comparison of exhaust manifold
Quality Control and Inspection
One of the most common uses of 3D scanners in manufacturing is quality control. After a part is produced, it can be scanned and compared directly to the original CAD model or against a gold-standard part to check for any deviations.
- Benefits:
-
- Quickly detect defects, warping, or dimensional inaccuracies
- Perform 100% inspections instead of random sampling at specific locations on the part
- Maintain high product consistency and reduce waste
Reverse Engineering
Sometimes manufacturers need to recreate parts for which no CAD model or technical drawing exists — especially for legacy equipment or aftermarket parts. A 3D scanner captures the exact geometry of the part, allowing engineers to create an accurate digital model for redesign, modification, or reproduction.
- Benefits:
-
- Save time compared to manual measurements
- Capture complex shapes that would be difficult to measure by hand
- Improve part performance with updated designs
Rapid Prototyping and Product Development
During the design and prototyping phase, 3D scanning can speed up the product development cycle. Engineers can scan prototype parts to quickly assess design changes or integrate existing components into new products. This has become increasingly helpful as more and more companies use additive manufacturing to speed up the prototyping process.
- Benefits:
-
- Shorter iteration cycles
- Easy integration with CAD and 3D printing workflows
- Better communication between design and production teams
Evaluation of mold wear using cross-sectional profile measurement
Tool and Mold Inspection
In industries like automotive and aerospace, tooling and molds must be extremely precise. 3D scanners are used to verify the condition and dimensions of molds, dies, and jigs to ensure they produce parts that meet tight tolerances.
- Benefits:
-
- Extend the lifespan of tooling through early detection of wear or deformation
- Avoid costly production delays or errors
- Validate repairs and maintenance work on critical tools
Assembly Verification
In complex assemblies, ensuring that all components fit together correctly is crucial. 3D scanning can check the final assembly to confirm correct part alignment, detect gaps, and verify geometric tolerances.
- Benefits:
-
- Reduce the risk of assembly failures
- Improve the reliability of mechanical systems
- Support automated assembly line verification
In-Process Monitoring
Some advanced manufacturing environments use 3D scanners inline during the production process to catch defects immediately. Automated robotic scanning systems can scan parts during manufacturing without stopping the production line.
- Benefits:
-
- Real-time defect detection
- Minimize costly rework and scrap
- Increase overall production efficiency
We’re here to provide you with more details.
Reach out today!
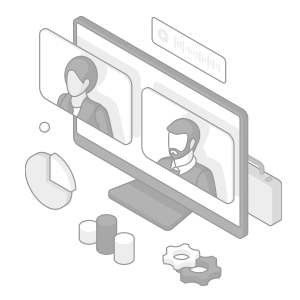
Key Advantages of 3D Scanning in Metrology
Enhanced Measurement Accuracy
Modern 3D scanners can deliver ultra-precise data, capable of capturing fine surface details and minute dimensional variations. This high resolution ensures that even the smallest manufacturing defects are detected before products reach the market.
The KEYENCE VL-800 Series 3D Scanner maintains a +/- 10 um (+/- 0.4 mil) accuracy with 2 um repeatability throughout its measurement envelope.
Faster Inspection Times
Compared to traditional measurement tools like calipers or fixed CMMs, 3D scanners drastically reduce inspection times. A full scan of a part can be completed in minutes, allowing for faster quality control processes and quicker decision-making. These scans can usually be done without the aid of a fixture, making their setup process much easier and faster than CMMs.
Non-Contact Measurement
3D scanning is a non-invasive technique, ideal for fragile components, soft materials, or sensitive surfaces that might be damaged through contact-based methods, including parts that may flex or deform when contacted. Non-contact scanning also improves safety and repeatability in the measurement process.
Comprehensive Data Storage and Analysis
The digital nature of 3D scanning means that data can be easily stored, retrieved, and analyzed. Engineers can overlay scans to detect changes over time, perform in-depth analyses with metrology software, and maintain a complete digital record for traceability and regulatory compliance.
KEYENCE VL-800 Series 3D Scanner CMM diagram showing both low and high mag integrated lenses
Flexibility and Versatility
Whether scanning a small, intricate part or a large industrial assembly, 3D scanners adapt to various sizes and materials. More advanced systems can even incorporate multiple lenses to provide high-resolution scans on these different-sized parts. Portable 3D scanners allow for on-site inspections in workshops, production lines, or even outdoor environments, enhancing flexibility.
Reverse Engineering and CAD Comparison
A 3D scanner enables reverse engineering by creating accurate digital models of existing parts. Additionally, scan data can be compared directly to CAD models to detect deviations, ensure parts meet specifications, and guide corrective actions. This can be particularly useful for legacy components or other parts that may not have a digital design file.
- Industries Benefiting from 3D Scanner Technology in Metrology:
-
- Automotive: Inspection of body panels, molds, and engine components
- Aerospace: Validation of complex turbine blades, fuselage parts, and aerospace tooling
- Manufacturing: Quality control of machined parts, injection-molded components, and assemblies
- Medical Devices: Precision measurements for implants, prosthetics, and surgical tools
- Energy: Inspection of large structures like wind turbine blades, pipelines, and valves
As the demand for tighter tolerances and faster production cycles grows, 3D scanning is reshaping the landscape of industrial metrology. Incorporating a 3D scanner into quality assurance processes allows manufacturers to achieve higher accuracy, streamline workflows, and ultimately deliver better products to market.
Whether for routine inspections, reverse engineering, or first-article validation, 3D scanners provide unparalleled capabilities that traditional measurement tools simply can't match. Embracing 3D scanning technology is not just an investment in better measurements—it's a step toward the future of smarter, faster, and more efficient manufacturing.
Contact us to learn more about how our advanced technology can help take your business to the next level.
Contact Us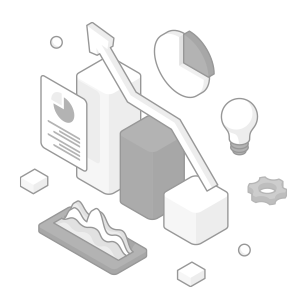
Related Downloads
Related Products
Scroll