Multisensor Measurement System
Micromachining: Benefits and Industries
Micromachining is for small parts, but its impact is mighty.
Rapidly growing and expected to reach a market value of $3.3 billion USD by 2025, micromachining is producing more powerful and intelligent parts at an exponentially smaller size than we’re used to. It is making manufacturing cheaper and more efficient, leading to enhanced patient comfort, longer-lasting cars, and smarter electronics.
What Is Micromachining?
Micromachining is the process of removing material at a micrometer level with computer numerical control (CNC) or laser machinery. The material removal results in intricate surface feature designs or shapes. This process is versatile across industries and materials. Notably, electronics, automotive, and medical device industries use micromachining for plastic, metal, ceramic, and silicon parts.
As with standard machining, micromachining includes subcategories like micro-milling, micro-turning, micro-grinding, and laser micromachining.
Micromilling is the process of using a rotating cutting tool to remove material. The removed material cuts out shapes or surface features.
Micro-turning is the process of using a linearly moving cutting tool on a rotating round or cylindrical workpiece.
Micro-grinding is a micromachining process that removes material from a spinning ceramic or glass workpiece.
Laser micromachining shoots a thin laser beam to machine any workpiece material or shape.
We’re here to provide you with more details.
Reach out today!
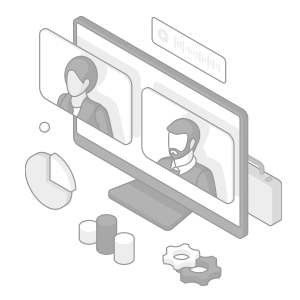
Benefits of Micromachining
Micromachining is a repeatable and reliable process that improves part cost, safety, and lifespan in medical device, electronic, and automotive industries.
Cost Effective
Micromachining uses high-speed, repeatable machines for micro-sized machining. With this machinery, it requires less time, energy, and cost to produce a micro-sized part versus a “normal” sized part. That being said, it’s crucial to note that micromachining produces parts that are often equal in effectiveness to standard-sized parts.
Increased Safety
Micromachining’s micron level tolerances reduce the likelihood of part failure. The tight tolerances fit parts securely together and prevent safety hazards from broken or loose parts.
Increased Lifespan
Micromachining tight tolerances also benefit component lifespan. When parts securely fit together, there’s less friction between them, and thus, less wear and tear, lending to a longer lifespan. Cars are lasting for over 200,000 miles because of tight tolerance practices!
Discover more about this product.
Click here to book your demo.
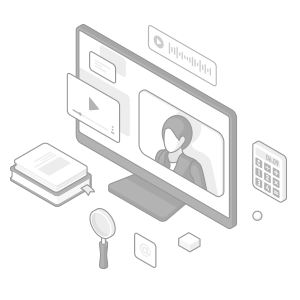
Micromachining Industries & Applications
Micromachining isn’t limited to just one industry. The innovation behind this process, specifically in the electronics industry, overlaps with medical devices and automotive. The overlap stems from the industry’s strict tolerances and desire to increase technology use.
Electronics Industry
Micromachined electronics are called MEMS. MEMS are made up of structures, sensors, actuators, and microelectronics. Put simply, MEMS are tiny, integrated systems combining mechanical and electronic components.
As micromachining grows, so do MEMS’ capabilities. MEMS are now adding photonics (the detection of light) and nanotechnology (nano-level matter manipulation) into the systems. This blend makes MEMS pick up a wider range of information, resulting in smarter and more sensitive MEMS. Despite the small size, these chips can be as intelligent as larger devices.
Medical Device Industry
Micromaching in the medical device industry is enhancing biocompatibility and perfect patient fit. With this technology, providers can develop more effective and personalized medical solutions like hearing aids and implants.
- Hearing Aids
- The microphones on hearing aids are a prime example of MEMS with photonic signals overlapping in another industry. Microphones and the silicon layer are both finely micromachined for perfect fit and sound transmission.
- Dental Implants
- Dental implants are micromachined to have biocompatible microgrooves in the mouth. The micromachined grooves prevent bacteria buildup around the implant and keep blood flowing through the gums. As a result, patients enjoy ease of implantation and avoid infections.
Automotive Industry
Micromachining in the automotive industry contributes to fuel control and efficiency. As the automotive industry looks to make cars lighter with more intelligence, micromachined MEMS and fuel injectors are providing the answer.
- Fuel Injectors
- Vehicle engine efficiency and performance have reaped the benefits of micromachining fuel injectors. Manufacturers micromachine holes on these parts to control fuel flow via opening and closing of fuel valves.
- Automotive Sensors
- The automotive industry is another overlap of MEMS with phononic signals. The addition of phononics to MEMS has widened the scope of automotive sensors. In the past, automotive sensors only measured basics like temperature and pressure. But now, micromachined automotive sensors measure position, speed, air flow, viscosity, torque, and angular rate. Even though vehicles are adding more sensors, the micro size is hardly affecting vehicle weight.
Contact us to learn more about how our advanced technology can help take your business to the next level.
Contact Us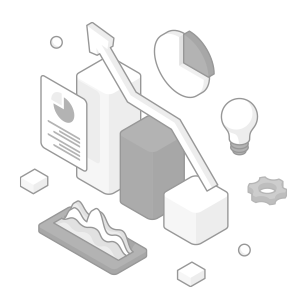
Performing QC Checks on Micromachined Parts
Even with all the benefits of micromachining, like tight tolerances and precise shapes, quality control (QC) checks are still necessary for 100% clarity. Micromachining with a mill, lathe, or EDM has risks of excessive heat, vibration, or problems with feed rate. All of these risks can compromise the final part. Although the parts are small in size, their value should not be ignored. Quality control checks are a best practice method for preventing waste, saving money, and intercepting potential recalls.
However, there are proactive steps you can take. First article, final and in-process inspections are methods that spot deformities and patterns of machine malfunctions. These inspections use multisensor optical measurement devices to measure dimensions and evaluate visual appearance.
We’re here to provide you with more details.
Reach out today!
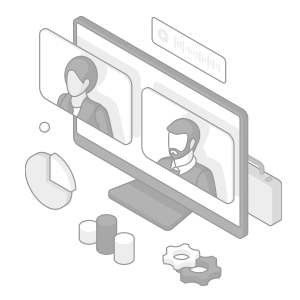
KEYENCE’s Micromachining Inspection Machine
At KEYENCE, we specialize in multisensor measurement systems for inspecting micromachined parts.
Our multisensor measurement system, the LM-X, is a type of optical measurement device that collects inspection from three sensors: vision, probe, and laser. Together, these three sensor types work to inspect hole diameters, surface edges, height changes, curved surfaces, and 3D rotational surfaces to sub-micron level accuracy at the push of a button.
Micromachined parts need intricate inspections for their fine-detailed features, tight dimensional tolerances, and precise features. The multisensor measurement system is the quality control answer. Contact us today for a free demo.
Get detailed information on our products by downloading our catalog.
View Catalog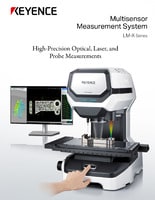
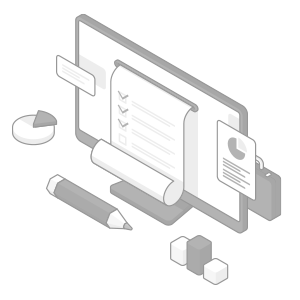
Related Downloads
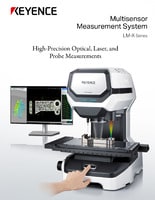
Brochure for the LM-X Series Multisensor Measurement System. Using optics, probes, and a multi-color laser to automatically measure all of your parts features.
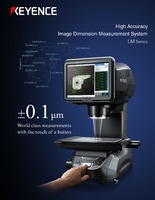
Brochure for the LM-1100 Series High Accuracy Image Dimension Measurement System. Submicron accuracy part inspection with non-contact height measurement.
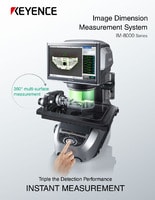
Brochure for the IM-8000 Series Image Dimension Measurement System. Accurately measure parts in seconds at the push of a button.