With roughly 150 counts per day, high-resolution images reduce eye strain and increase counting accuracy
Marudai Service Co., Ltd. introduced the BC-1000 High-Accuracy Automated Colony Counter from KEYENCE in order to improve inspection reliability and capture images of the samples they were testing. The company uses this system to inspect high volumes of food that are delivered each day from their affiliate companies. We interviewed Ms. Yumi Hirao, who is in charge of testing, of the Bacteriology and Physical Chemistry Inspection department, to learn more about how they use the BC and why they purchased it.
Marudai Service Co., Ltd.
Marudai Food Co., Ltd., a Tokyo Stock Exchange prime listed company, is a leading manufacturer of processed meat products. Its subsidiary, Marudai Service Co., Ltd., primarily manages real estate and insurance businesses. In 2022, Marudai Service expanded into the inspection sector after acquiring bacteriological and physicochemical testing operations from Marudai Food. Today, Marudai Service plays a critical role in ensuring food safety by conducting comprehensive inspections on a variety of processed products, raw meats, and prepared foods, both at its head office and across partner companies.
Get detailed information on our products by downloading our catalog.
View Catalog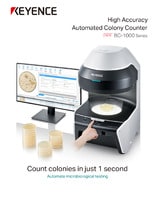
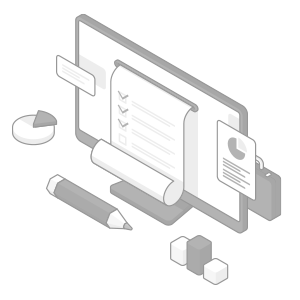
Testing a high volume of samples
How is the BC being utilized?
The Bacteriological and Physical Chemistry Inspection Section at Marudai Service oversees all inspections for the entire Marudai Food Group. Daily test requests and samples are sent from Marudai Food headquarters and affiliate companies. We use the BC for all colony counting tests that involve Petri dishes, with roughly 150 inspections done per day. We handle a wide range of samples and inspect not only processed foods but also raw meat and prepared foods.
How many inspections are conducted, and by how many people?
There are three people performing inspections. At Marudai Service, inspections are divided into three major categories: sampling, culturing, and enumeration. These tasks are performed by three people who take turns being in charge of the work. The shift-based system was implemented to improve efficiency and ensure seamless coverage, allowing team members to support one another during system changes, such as when someone goes on maternity leave.
Performance expectations
How did you find out about the BC?
The first opportunity came when a KEYENCE sales representative visited the Quality Assurance Department at Marudai Food’s head office. They then got in touch with us since we are responsible for inspection practices, and we decided to have a chat. Things moved along smoothly from there, and I remember we quickly decided to go ahead with the system.
Have you compared the product with the competition?
We made a thorough comparison of other companies. There are automatic colony counters from various manufacturers. However, none of the systems we have seen so far have been able to produce results that can reliably replace the human eye. Of all of the tools we looked at, only the BC was able to accurately count our samples, which was the major deciding factor for us. KEYENCE products have a great reputation as well so that also helped.
What did you expect from the BC when you introduced it?
We expected to be able to accurately count the bacterial colonies on our dishes while also capturing a high-resolution image of it to improve our documentation. We’d also like to eventually integrate this with an inspection management system to eliminate the time and potential errors involved with manually inputting data.
Will you be able to integrate it with the management system?
Our current system is pretty outdated and slow, so I’m not planning on trying to integrate the BC with that system. However, we are in the process of building a new management system that should work well with it.
Contact us to learn more about how our advanced technology can help take your business to the next level.
Contact Us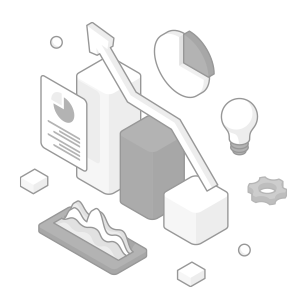
Counting operations, which tended to be performed by a single person, are now standardized by the BC
What are some positive aspects of implementing the BC?
There are three main benefits that we felt after introducing the BC.
- Using Automatic Counting to Eliminate Eye Fatigue
With the BC, bacterial colonies are automatically counted in an instant, eliminating the need for manual counts and reducing eye strain. We’re used to counting colonies and can do so pretty quickly, so the real benefit of this system was more about reducing fatigue in our technicians than it was about speed. - Archiving Results with High-Resolution Photos
Another key advantage of the BC system is the ability to capture and preserve high-resolution images of the Petri dish. Since bacteria can discolor or change over time, having access to photos of their original condition during inspection is incredibly valuable. In fact, we occasionally receive requests from clients asking, "What did the bacteria look like in that test?" Thanks to the BC’s high-quality camera, we can capture detailed images and easily respond to these questions by simply sharing the photos. - Easy to Operate and Use
Our on-site inspectors also found the BC to be very easy to use, especially since they can just push the "Count" or "Save" buttons on the system. This helped us reduce the time and effort needed for each inspection which can be considerable given the number of samples that we needed to test. We also thought the actual application software was very user friendly as well. Once we were able to test it out and learn it, anyone can pretty much walk up and use the equipment with just minimal training.
Now anyone can count colonies
Counting bacterial colonies accurately by visual inspection requires a certain amount of knowledge, experience, and skill. It's a task that tends to be specialized, so to speak, but with the BC anyone can overcome that hurdle. Even beginners can get good results once the initial set up is done. While small adjustments might be needed, depending on the product, bacteria type, and other factors, variations in counts can still happen. But unusual results aren't a problem, as an experienced inspector can always step in to review and verify them later.
Quick and helpful product support
How would you rate KEYENCE’s product support staff?
The support specialists at KEYENCE are courteous and quick to respond, which I greatly appreciate. They are proactive in addressing any issues, and contact me immediately if we need assistance.
When I ask questions—whether they require a quick answer or more in-depth research, such as inquiries about specific functions—they consistently respond promptly, often saying, “We’ll look into it and get back to you.” Their willingness to assist is genuinely helpful.
Additionally, I have shared some suggestions for improving the usability of the BC application. I believe my willingness to provide this feedback stems from their approachable demeanor, which encourages open communication.
Curious about our pricing?
Click here to find out more.
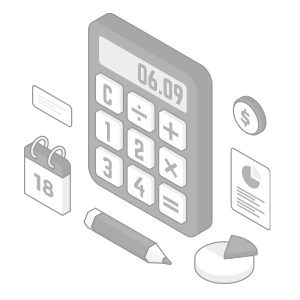
Future BC usage at other inspection sites
What changes do you envision for your other inspection sites in the future?
In the future, we aim to enhance productivity by centralizing inspection systems and better addressing a broader range of needs.
We currently face challenges in centralizing our inspection processes. Our existing management system allows us to create documents that summarize daily inspections and enter and manage data afterward. However, due to the system’s outdated nature, referencing notes and manually entering results is still as time-consuming as visual counting used to be.
We’re excited about the possibility of integrating the BC with the management system we plan to develop in the future. If successful, it would automate data input, reduce labor and transcription errors, and speed up inspections. This is a goal we’re looking forward to accomplishing.
Marudai has such a diverse range of food product offerings, which include everything from meat products to desserts and beverages, so as you can imagine there are numerous food safety standards we need to meet. We aim to pioneer a system that can reliably adapt to these evolving food safety requirements.
We believe the BC can play a crucial role in ensuring this reliability, and I look forward to continuing to utilize this equipment in the future.
We’re here to provide you with more details.
Reach out today!
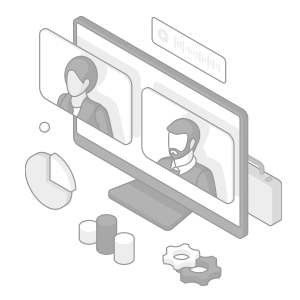