Digital Microscopes
Shot Blasting Observation and Measurement Using Digital Microscopes
Shot blasting is a processing method in which pieces of media (small pieces of sand or small steel or cast iron balls) are sprayed at high speed at a workpiece, shaving down the workpiece’s surface by creating small projections and depressions on it. Polishing results in a smooth surface finish, but shot blasting results in a rough surface. This section provides an overview of shot blasting and introduces examples of its observation and measurement using a digital microscope.
What Is Shot Blasting?
This process is called shot blasting because small steel or cast iron balls (shot) are sprayed at Shot blasting is a process where small steel or cast iron balls (shots) are rapidly sprayed (blasting) using a rotating impeller. These balls are propelled at high speed onto the blade, applying the media through centrifugal force. In comparison, the method in which the media is sprayed by compressed air is called air blasting or sandblasting.
A : Media B : Impeller C : Rotation D : Workpiece
Shot blasting
A motor causes the impeller to rotate, spraying the media by centrifugal force. Because no compressor is necessary, this method has lower energy and cost requirements. However, the processing force is not easy to adjust, making it difficult to obtain highly accurate processing.
A : Compressor B : Compressed air C : Tank
D : Media E : Nozzle F : Compressed air + media G : Workpiece
Air blasting (sandblasting)
The media is sprayed by the compressed air from the compressor. Because the pressure can be adjusted easily, this method provides highly accurate processing.
Get detailed information on our products by downloading our catalog.
View Catalog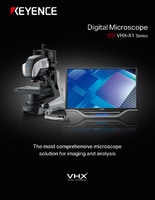
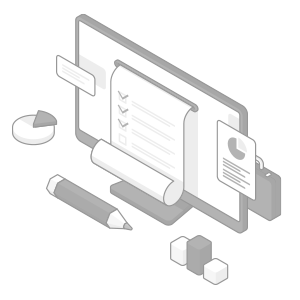
Workpiece and Media Materials
This section introduces the main workpiece and media materials.
- Workpieces
Metal, ceramic, plastic, glass, and rubber - Media
Small steel or cast iron balls (shot), sand, stainless steel, alumina, copper, glass, resin, plastic, and walnut powder
We’re here to provide you with more details.
Reach out today!
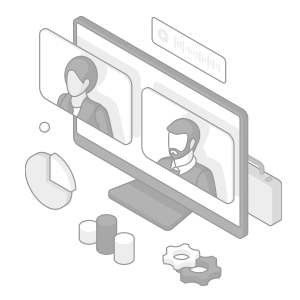
Purposes and Effects of Shot Blasting
- Rust and dirt removal
Rust removal from metal surfaces, sand removal from die cast parts, welding spatter removal, and coating/oil stain removal - Burr removal
Burr removal after pressing or machining - Creating projections and depressions
This process improves the adhesion of coating, plating, bonding, etc.
Satin processing provides reflection prevention as well as improving oil reception, friction force, and heat dissipation. - Shot peening
Compressive residual stress improves the wear resistance, chipping resistance, and fatigue strength.
We’re here to provide you with more details.
Reach out today!
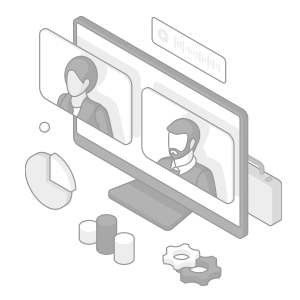
Shot Blasting Observation and Measurement Examples Using a Digital Microscope
These are the latest examples of shot blasting observation and measurement using KEYENCE’s VHX Series 4K Digital Microscope.
Shot observation images
Using the depth composition function allows for observation with images where the entirety of each ball-shaped piece of shot is in focus.
ZS-20, 150×, ring illumination, normal image
ZS-20, 150×, ring illumination, depth composition image
Automatic area measurement of shot blasted surfaces
The surface roughness after shot blasting can be quantified.
ZS-20, 150×, coaxial illumination, before measurement
ZS-20, 150×, coaxial illumination, after measurement
3D profile measurement of shot blasted surfaces
3D profile measurement can be used to compare the roughness in different locations.
VH-Z20, 200×, ring illumination, depth composition image
VH-Z20, 200×, ring illumination, 3D measurement image
Observation of a sieve used in shot blasting
Using the HDR function allows for observation without glare.
ZS-200, 1000×, ring illumination, HDR image
Get detailed information on our products by downloading our catalog.
View Catalog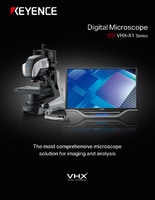
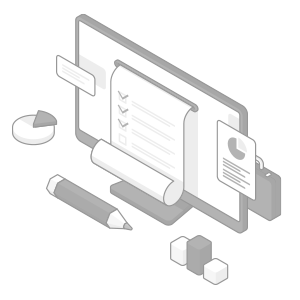