Digital Microscopes
Observation and Analysis of Lithium-ion and Next Generation Batteries
With the growing demand for applications in electrical and electronic equipment, such as smaller and thinner electronic devices, in-vehicle batteries that require large capacities and safety, and residential energy storage systems, lithium-ion batteries have become an important industrial field. The storage capacities and charging speeds of lithium-ion batteries have seen increasing improvements. At the same time, these batteries have risks that cannot be overlooked such as ignition and the generation of heat and smoke. To reduce these risks, it is important to ensure safety in research and development, quality assurance, and quality control.
Due to intense competition and fast product cycle, the observation and analysis of these batteries need to be performed as quickly as possible. This section includes basic knowledge of lithium-ion and next generation batteries, and examples of the latest methods to drastically improve observation and analysis.
Basic Structure, Types, and Materials of Lithium-ion Batteries
Lithium-ion batteries, which are secondary batteries called LiBs for short, are commonly used for smaller and thinner electronic devices including smartphones, tablets, wearable devices, and laptop computers; in-vehicle batteries for electric vehicles (EVs) and hybrid electric vehicles (HEVs); and power storage systems for residential photovoltaics and fuel cells. With the expanded applications, lithium-ion batteries are now manufactured to have various structures and shapes. Read on for explanations of the basic structure, typical shapes, and some other related items of lithium-ion batteries.
Basic structure of lithium-ion batteries
Each part of a lithium-ion battery, including their functions, is explained here with a figure showing a typical example of the basic structure of these batteries.
A) Negative electrode (cathode): Highly conductive carbon-based materials (graphite, lithium titanate, etc.) are coated onto copper foil.
B) Positive electrode (anode): Lithium composite oxides (lithium, manganese, cobalt, nickel and iron phosphate, etc.) are coated onto aluminum foil.
C) Separator: This is a microporous membrane made from a chemical compound called polyolefin (examples of which include polyethylene [PE] and polypropylene [PP]). The membrane has small holes (1 micrometer or less) on the surface. The separator isolates the positive and negative electrodes and prevents fires caused by them coming into contact.
D) Electrolyte: Lithium salt is dissolved in an organic solvent.
E) Charge
F) Discharge
G) Current collector: Plays the roles of an electrical conductor to collect the generated electricity and of a support material. The positive electrode is aluminum foil, and the negative electrode is copper foil.
H) Binder: Used to bond mixed materials on the current collector foil.
I) Active material: Significantly affects the capacity, voltage, and characteristics. There are various materials to use (such as lithium cobalt oxide, lithium manganese oxide, and lithium iron phosphate), mixing ratios, and stirring methods.
Shapes and forms of lithium-ion batteries
Cells of lithium-ion batteries, which have the internal structure introduced above, are covered with cases in various shapes and forms made from different materials. Three representative shapes (forms) of lithium-ion batteries are explained below with figures.
A: Positive electrode terminal B: Negative electrode terminal a: Positive electrode b: Negative electrode c: Separator
Cylinder type
Cylindrical lithium-ion batteries are believed to have the highest capacity density at the lowest cost. However, when multiple cells are combined in a case, gaps are left between the cells, decreasing the density.
a: Positive electrode b: Negative electrode c: Separator
Prismatic type
Aluminum cases are often used for prismatic lithium-ion batteries. The polarity of a prismatic battery changes according to the case material, iron or aluminum. An iron case has the positive terminal on the top while an aluminum case has the negative terminal on the top.
A: Positive electrode terminal B: Negative electrode terminal a: Positive electrode b: Negative electrode c: Separator
Laminated type (lithium polymer battery)
The laminated type is also called a lithium polymer battery. Because using a cell laminated with films can reduce the thickness of the battery, this type is used for devices that need to be thinner, such as smartphones and tablets.
Typical electrolytes used for this type are gels containing polymers such as polyethylene oxide (PEO), polypropylene oxide (PPO), and polyvinylidene difluoride (PVDF).
Types and characteristics of materials used for positive and negative electrodes of lithium-ion batteries
The characteristics, applications, and even costs change according to the materials used for the positive electrode or negative electrode of lithium-ion batteries. Read on for an introduction to some typical types and their characteristics.
- Cobalt base
Positive electrode: Lithium cobalt oxide LiCoO2/Negative electrode: Graphite LiC6
The most commonly used lithium-ion batteries, mainly in mobile devices. But cobalt is expensive and there is the risk of thermal runaway, so they present safety concerns for use in vehicles. - Nickel base
Positive electrode: Lithium nickel oxide LiNiO2/Negative electrode: Graphite LiC6
Nickel-based lithium-ion batteries have the largest capacity. There used to be safety concerns regarding this type. However, the NCA base, produced by substituting cobalt for a part of the nickel and adding aluminum, has improved the safety of this type, making it possible to be used in plug-in hybrid electric vehicles. - Manganese base
Positive electrode: Lithium manganese oxide LiMn2O4/Negative electrode: Graphite LiC6
Manganese-based lithium-ion batteries (LMO base) are most commonly used in vehicles because manganese is cheap, approximately a tenth of cobalt, and its rigid crystal structure is very safe because it has high thermal stability. - Iron phosphate base
Positive electrode: Lithium iron phosphate LiFePO4/Negative electrode: Graphite LiC6
Lithium-ion batteries using iron phosphate have a crystal structure that is very safe because it is difficult to break even when heated in batteries. Another advantage is that this type can be manufactured at costs even lower than manganese-based batteries that use iron. A disadvantage of this type is its low energy density. - Three-component base
Positive electrode: Nickel and manganese are substituted for a part of lithium cobalt oxide Li(Ni-Co-Mn)O2/Negative electrode: Graphite LiC6
Three-component lithium-ion batteries, also called NCM-based batteries, use three components—cobalt, nickel, and manganese—to increase safety. As with NCA-based batteries, this type is used in plug-in hybrid electric vehicles. - Titanic acid base
Positive electrode: Lithium manganese oxide LiMn2O4/Negative electrode: Lithium titanate Li4Ti5O12
Titanic acid-based lithium-ion batteries have long service lives that are approximately six times longer than conventional lithium-ion batteries using graphite for the negative electrode and also charge very quickly.However, they have low energy density, which is a disadvantage.
Get detailed information on our products by downloading our catalog.
View Catalog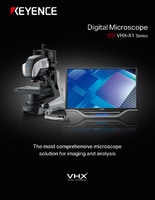
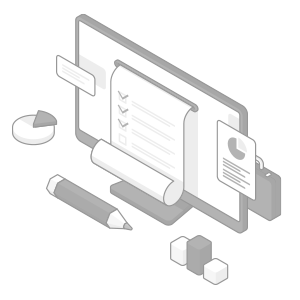
Observation and Analysis of Secondary Batteries
In parallel with modifications and performance improvements of lithium-ion batteries, each manufacturer is promoting the development of the next generation of secondary batteries. Read on for an introduction to the types and characteristics of representative next generation batteries that are expected to become available and popular. A summary of the problems in the observation and analysis in the secondary battery industry where manufacturers are competing fiercely is also provided.
Next generation batteries that are expected to become available and popular
With expanded applications such as usage in electric vehicles (EVs), next generation secondary batteries are expected to be even safer and have even larger capacities. Many companies, regardless of their scale, are working on developing next generation secondary batteries as a way to improve their business future.
- Lithium-air battery
Some studies suggest that capacity density can, in theory, exceed 10,000 Wh/kg. In the tests, this characteristic has been confirmed to reach approximately 600 Wh/kg. However, it is easy for deposits to form on lithium metal, which is used for the negative electrode. As such, the safety of this metal may decrease and its characteristics may deteriorate when it reacts with moisture in the air. - Solid-state battery
A solid-state battery uses a solid electrolyte as the separator instead of the liquid electrolytes used in lithium-ion batteries. This allows solid-state batteries to be manufactured in various shapes and to be free of fluid leakage. The theoretical capacity density is believed to be at least 2000 Wh/kg. This is, however, only a theoretical value. Research and development are currently ongoing with the goal of putting this type of battery into practical use with the target capacity density of 500 Wh/kg or more. This type of battery can charge and discharge at high speeds and is hard to deteriorate even after many charge cycles.
Solid electrolytes are available in two types: sulfur base and oxygen base. The sulfur-based electrolyte has superior characteristics, but poses the risk of generating hydrogen sulfide when ignited or interacting with water. Manufacturing of solid-state batteries has started with small ones for electronic devices. - Next generation lithium-ion battery
Silicon and graphene are used for the negative electrode. This type of battery is being researched and developed to increase the capacity while existing manufacturing processes are used. Researchers are especially interested in this battery due to its capability to increase the charging and discharging speeds when changing to different electrolytes. - Lithium-sulfur battery
Lithium-sulfur batteries can have a capacity density of 2500 Wh/kg in theory, which is higher than solid-state batteries, and use no expensive materials such as cobalt. With these features, large capacities at low costs can be expected. At the same time, lithium-sulfur batteries have low conductivity and low stability and can deteriorate when charged many times. - Sodium-ion battery
Although the capacity density is equal to or slightly less than that of current lithium-ion batteries, sodium-ion batteries can be manufactured at low costs because no rare metal is required and existing manufacturing equipment can be applied. As with existing lithium-ion batteries, sodium-ion batteries have concerns regarding safety, such as high reactivity of sodium deposits, and their characteristics can deteriorate after many charge cycles.
Problems in observation and analysis using conventional microscopes
Manufacturers are competing to develop safer lithium-ion batteries having higher performance and producing superior technologies before their competition which requires quality assurance and control.
Therefore, observation, analysis, quantitative evaluation, and even the speed of these operations are important and are key factors to success for both testing and quality assurance in the development and improvement of secondary batteries.
At the same time, observation and analysis using conventional microscopes have the following problems.
- Focus adjustment and lighting condition determination are difficult for three-dimensional targets or targets having subtle scratches with low contrast. On these targets, the focus position varies from operator to operator, resulting in errors in evaluation results.
- Glare may occur during observation of areas containing a mix of materials having different glossy surfaces. It is difficult to determine the lighting settings appropriate to observe these targets, often causing mistakes in analysis.
- It takes time and effort to align a sample and change the angle.
- To count contaminants and closely observe foreign particles according to applicable industrial standards, setup can be cumbersome, requiring a lot of time and effort. Additionally, a high level of expertise is required to acquire accurate analysis results and quantitative values.
- Measured values and counts are not stored as numeric data, which requires a lot of time and effort for subsequent work such as analysis, evaluation, and report creation.
If you are experiencing the above problems, see below for examples on how KEYENCE's VHX Series digital microscope allows any user to capture fully-focused, high-resolution images and accurate data.
We’re here to provide you with more details.
Reach out today!
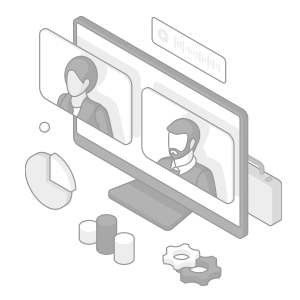
Latest Examples of the Observation and Analysis of Lithium-ion Batteries
With the recent technological progress of digital microscopes, each part of a secondary battery can be observed quickly and clearly even at high magnifications. The latest digital microscopes can dramatically save time when performing dimensional measurement, contamination (foreign particle) analysis, and creating reports with the images and numeric data.
With high-resolution lenses, a 4K CMOS image sensor, and the ability to automatically adjust focus and lighting conditions, KEYENCE’s VHX Series digital microscope can capture fully-focused images and accurate measurements of secondary batteries with higher efficiency compared to conventional systems.
See below for observation and analysis examples of lithium-ion batteries using the VHX Series.
Counting of foreign particles (contamination analysis that complies with ISO standards)
The VHX Series can measure contamination according to the ISO 16232 and VDA 19 cleanliness standards. By utilizing the automatic area measurement/count function, contamination (foreign particles) can be easily and accurately counted and measured, even on targets with surface irregularities.
Using the advanced functions of the VHX Series, users can select a specific contaminant and the stage will automatically move to that location, allowing the selected contaminant to be closely observed at high magnifications in the same image. As a result, foreign particles can be easily identified in a shorter time compared to when using conventional microscopes. Additionally, by combining the depth composition and 3D height measurement functions, users can easily observe and quantify measurements even on targets having surface irregularities.
Foreign particle counting using the VHX Series 4K digital microscope
Before counting: Ring illumination (50x)
After counting: Ring illumination (50x)
Observation of scratches on separators
The VHX Series fully-integrated (FI) head can automatically switch between lenses and seamlessly adjust magnification from 20x to 6000x. Our built-in lighting unit allows the VHX Series to clearly observe any target using brightfield, darkfield, polarized light, and differential interference contrast (DIC).
For example, subtle scratches on separator surfaces, which are difficult to observe using conventional microscopes, can be visualized easily and quickly in a high-resolution image captured using DIC.
Differential interference contrast (DIC) image (400x)
Observation of scratches on a separator using the VHX Series 4K digital microscope
Observation of peeled negative electrode materials
The VHX Series digital microscope has a large depth of field and advanced observation methods, enabling high-resolution, fully-focused imaging throughout the entire observation field even if the target has a glossy surface.
Additionally, with the Multi-lighting function, image data is automatically captured with omnidirectional lighting at the press of a button. The image with optimal lighting can be acquired by selecting the most suitable from the captured images. Because images other than the one selected are also stored, users can easily pull up the other images captured under different lighting conditions at any time. Additionally, the conditions used to capture a past image can be automatically reproduced and used for observing a different sample of the same type, which reduces human errors in observation and evaluation.
Observation using the built-in coaxial illumination (2500x)
Observation of peeled negative electrode materials using the VHX Series 4K digital microscope
Observation of welded sections on battery cases
The quality of welding used to seal the lid or cover on square cases is very important to ensure the safety of lithium-ion batteries.
Using Optical Shadow Effect Mode on the VHX Series, allows users to easily visualize subtle surface irregularities by analyzing displacement (contrast) in an image captured with omnidirectional lighting.
Color information can be overlaid on the Optical Shadow Effect Mode image to visualize the surface irregularity information in an easy-to-understand manner, by representing the surface irregularity information with different colors (color mapping).
Not only are you able to accurately measure the surface irregularities on the selected image, but you are also able to use the stored images taken of the same sample which saves time, as you no longer would need to recapture the images like with conventional systems.
Since Excel can be installed on the VHX Series, all the images and measurement data can be automatically output to a report which significantly reduces the amount of time spent on creating reports.
Observation of welded sections on a battery case using the VHX Series 4K digital microscope
Optical Shadow Effect Mode image (20x)
Color map image (20x)
We’re here to provide you with more details.
Reach out today!
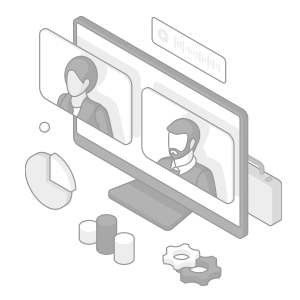
A Microscope That Revolutionizes Research and Development and Quality Assurance/Control of Lithium-ion and Next Generation Batteries
The VHX Series digital microscope is a powerful tool that can improve inspection processes using high-resolution images and quantitative numeric data. This tool allows even novice users to quickly capture 4K images, accurate measurement data, and perform contamination/counting analysis of foreign particles at the push of a button.
With the secondary battery market being fiercely competitive, it's essential that companies are able to utilize the VHX Series digital microscope to quickly observe, analyze, and create reports of their findings.
For additional info or inquiries about the VHX Series, click the buttons below.
Get detailed information on our products by downloading our catalog.
View Catalog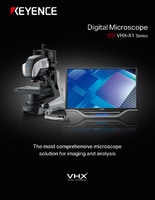
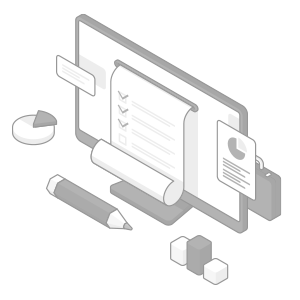