Digital Microscopes
Observation and Inspection of the Polishing Process Using a Digital Microscope
During polishing, the size of the abrasive is gradually reduced to obtain a smooth surface. This is used as the finishing process after grinding. Surfaces can also be polished to a mirror finish to reduce diffuse reflections. This section provides an overview of the polishing process and introduces examples of its observation and inspection using a digital microscope.
What Is Polishing?
This is a method for using abrasives to gradually trim down a material, resulting in a smooth surface.
It is used to make surfaces glossy like a mirror or smooth and improves the outer appearance and sliding performance of products.
Abrasive and grinding bit glossary
- Grain size
The grain size indicates the size of the abrasive. It is expressed with a number, and, generally, the larger the number, the smaller the particle. - Bond strength
Indicates the hardness of the grinding bit with an alphabet letter. The closer to the start of the alphabet, the lower the hardness. The closer to the end of the alphabet, the higher the hardness. The rule of thumb is to use a soft grinding bit with a hard target and vice-versa. - Structure
Indicates the grain as a percentage of the volume of the structure.
Structure number | 0 | 1 | 2 | 3 | 4 | 5 | 6 | 7 | 8 |
---|---|---|---|---|---|---|---|---|---|
Percentage of grain (%) | 62 | 60 | 58 | 56 | 54 | 52 | 50 | 48 | 46 |
- Binding agent (bond)
The substance that holds together two grinding bits is called the binding agent (bond). Two typical binding agents are as follows.
Resinoid (B): Supports high-speed rotation and is used in rough grinding.
Vitrified (V): Used in finishing grinding and polishing.
Get detailed information on our products by downloading our catalog.
View Catalog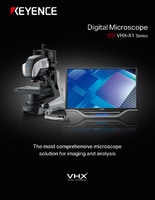
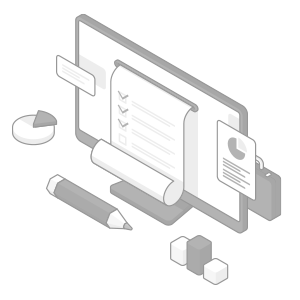
Types of Polishing
Representative types of polishing and their characteristics are as follows.
- Grinding bit polishing
In this polishing method, the product is brought into contact with a grinding bit rotating at high speed. - Buffing
In this polishing method, an abrasive is applied to a soft piece of cloth or felt that rotates. It is the final step in the polishing process and is used to obtain a mirror or polished finish. - Lapping
In this polishing method, the product is secured on a circular, flat surface plate called a lap, which is rotated while pressure is applied. Wet and dry methods are used depending on the abrasive type.
Wet: An abrasive is added and processing is performed at low pressure. Because a large amount of processing is performed, the surface receives a matte finish.
Dry: An abrasive is rubbed into the uneven surface of the plate and processing is performed at high pressure. A small amount of processing is performed, and the surface receives a mirror finish. - Barrel polishing
In this polishing method, an abrasive and the product are inserted into a tank-shaped container, which is then rotated. Although this method is suited to mass production, the polishing is rougher than with buffing or lapping. This method is often used to remove burrs from products. - Electrolytic polishing
In this polishing method, electricity is fed through the product to make its surface smooth. Although this method is expensive, it enables the polishing of small or narrow parts, which are difficult to polish otherwise.
We’re here to provide you with more details.
Reach out today!
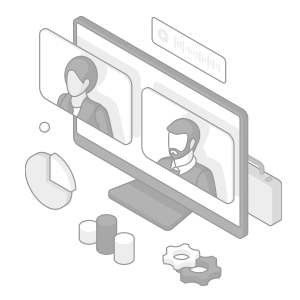
Typical Materials of Abrasives
Various types of abrasives are available. Typical materials of abrasives and their processing targets are as follows.
- Aluminum oxide
Known as alumina, this abrasive is extremely inexpensive, which is why it is used as widely as silicon carbide.
Processing targets: Iron, metals - Carbides
Silicon carbide is the representative abrasive, and it is inexpensive and widely used.
Processing targets: Non-ferrous metals (copper and aluminum), nonmetals - Zirconia
Although not as hard as diamonds, this abrasive is used to polish difficult-to-machine materials.
Processing target: Difficult-to-machine materials - CBN
The acronym of Cubic Boron Nitride, this abrasive has hardness inferior only to diamonds, but is more expensive than them. Its resistance to high temperatures gives it a long service life.
Processing target: Carbide alloys - Diamond
Because it is not resistant to heat, this abrasive is used to polish materials, such as glass and silicon, that have high hardness and low reactivity even at high temperatures.
Processing targets: Glass, silicon
We’re here to provide you with more details.
Reach out today!
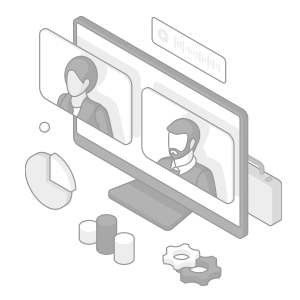
Example Observations and Inspections of the Polishing Process Using a Digital Microscope
This section introduces the latest examples of observation and inspection of the polishing process using KEYENCE’s VHX Series 4K Digital Microscope.
Observation of diamond abrasive
1000x, coaxial illumination
Automatic area measurement image of an abrasive
1000x, coaxial illumination
The automatic area measurement function makes it possible to quantify the size of abrasives.
Observation of mesh clogging
200x, ring illumination
Automatic area measurement image of a mesh
Automatic area measurement makes it possible to easily detect clogging.
Observation of a grinding bit
1000x
Left: coaxial illumination, right: ring illumination
Comparison of 3D images before and after using a grinding bit
100x, ring illumination
A: before use, B: after use
The 3D measurement function makes it possible to measure differences in the shape from before and after using the grinding bit.
Observation of a surface with a mirror finish
80x, ring illumination
Optical Shadow Effect Mode image of a surface with a mirror finish
The Optical Shadow Effect Mode function makes it possible to visualize minute waviness and scratches on the mirror surface.
Observation of a polished ceramic surface
4000x, coaxial partial illumination
Optical Shadow Effect Mode image of a polished ceramic surface
The Optical Shadow Effect Mode function makes it possible to visualize minute irregularities on the polished surface.
Polished surface roughness measurement
500x, coaxial illumination
Get detailed information on our products by downloading our catalog.
View Catalog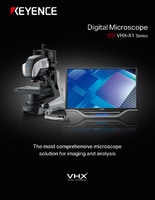
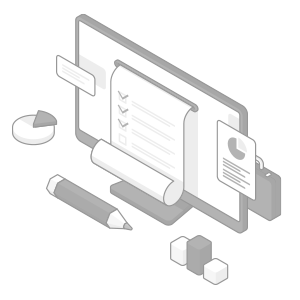