Coding in Pharmaceutical and Medical Product Packaging with UV Laser Technology
Coding on pharmaceutical and medical product packaging with a UV laser coder seamlessly replaces conventional thermal transfer overprinters (TTO) without requiring changes to machinery or packaging materials.
No ink transfer after marking
Permanent, precise codes eliminate waste, consumable costs, and maintenance associated with ribbons and other consumables without damaging the material.
Conventional thermal printer
UV laser coder
* Results comparison after rubbing on the marked area of film exposed to powder before marking
UV Laser Coding and Marking in Pharmaceutical and Medical Product Packaging
The FP-1000 Series laser coder easily marks multi-layer films, foils, paper-based wraps, and laminated packaging. It is a powerful solution for pharmaceutical and medical product packaging, including:
- Medicine blister packs and vial labels
- Medical device wraps
- Sterilization pouches
- Toothpaste
- Bandage and wound care packaging
- Pill containers
- Surgical tool wraps
Granule package
Retort food pouch
Toothpaste tube
Alcohol container
We’re here to provide you with more details.
Reach out today!
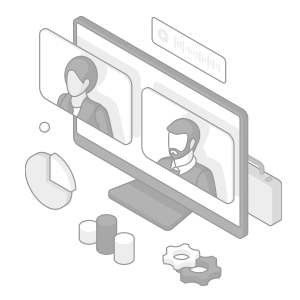
Pharmaceutical and Medical Product Packaging-Specific Challenges Solved by FP-1000 Series Technology
Mark Durability
Medical packaging requires clear, permanent marks for traceability. The FP-1000 Series delivers high-contrast codes that endure storage, transport, and other handling challenges.
Ink marking
Marking is affected by surface conditions because the ink is transferred onto the film surface.
UV laser coder
The marking dose not fade because the color of the marked layer of the film is changed.
-
1Laminated surface (transparent)
-
2Marking layer
-
3Other film layers
-
4Sealant layer
No periodic parts replacement required
No periodic maintenance/inspection required
Downtime & Interruptions
Frequent maintenance on TTO systems causes production delays. The FP-1000 Series’ non-contact, maintenance-free design ensures continuous operations without part replacement interruptions, optimizing production downtime.
-
1UV laser coders can mark more products in the same operating time
-
2Downtime due to ink ribbon replacement and thermal head cleaning
High Consumable Costs
Traditional methods like thermal transfer overprinting (TTO) rely on ribbons and print heads, increasing costs and waste. A UV laser coder eliminates consumables and uses light-based marking.
Cost reduction example:
With film costs of 0.04 dollars/sheet, 350 sheets of film wasted/day at a product unit price of 1 dollar/item and with product waste of 10 items/day, operating for 25 days a month.
No ink ribbon costs
No head replacement costs
Sustainability
An eco-friendly solution, the FP-1000 Series reduces waste and energy consumption, supporting sustainable practices for UV laser coding in the pharmaceutical and medical products industry.
Disposal loss simulation:
For a facility that replaces four ink ribbons per day, operating at 25 days per month will lead to disposal of 1,200 ink ribbons per year. At 500 grams 17.65 oz per ink ribbon, 1,200 ink ribbons would equal 600 kilograms 1322.76 lb, or about 1.2 tons of CO2 emissions upon disposal. UV laser coders, however, do not use ink ribbons, so the CO2 emissions can be reduced to zero.
Why Choose the FP-1000 Series for Pharmaceutical and Medical Product Packaging Marking Needs?
One leading, innovative method for packaging pharmaceutical and medical products is the FP-1000 Series UV laser marking system. It produces excellent, permanent markings quickly and precisely without the use of ink or ribbons. Its smooth integration and low maintenance needs guarantee effective operation and significantly less downtime. Contact us for help with meeting strict medical industry standards and to improve your coding on pharmaceutical and medical product packaging processes.
Contact us to learn more about how our advanced technology can help take your business to the next level.
Contact Us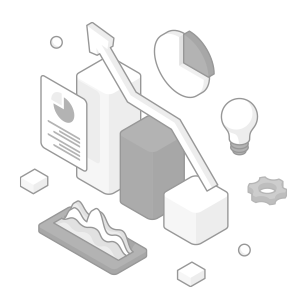
FAQs About UV Laser Technology in Pharmaceutical and Medical Product Packaging
Why Do Pharmaceutical and Medical Manufacturers Choose the FP-1000 Series for Their UV Laser Coding Needs?
Because of its accuracy, robustness, and environmentally friendly coding, manufacturers rely on the FP-1000 Series to ensure regulatory compliance and effective, consumable-free operations.
What Health and Safety Advantages Do UV Laser Coders Have Over Traditional Ink/Ribbon-Based Printers in the Pharmaceutical and Medical Product Packaging Industry?
UV laser coders provide clean, non-toxic, and permanent markings that are necessary for pharmaceutical and medical industry package coding and marking needs. UV technology helps avoid dangerous inks and ribbons, lowering hazardous material exposure and contamination risks.
Can UV Laser Markers Code on Diverse Materials Used in Pharmaceutical and Medical Product Packaging?
Yes, UV laser coding and marking on pharmaceutical and medical product packaging handles materials like plastics and films, ensuring clear, permanent marks on a wide range of substrates.
How Does the FP-1000 Series UV Laser Coder Ensure High-Speed Coding on Pharmaceutical and Medical Product Packaging?
Accurate, fast marks without making contact are possible with the FP-1000 Series due to the high-absorption rate of UV laser wavelength, allowing it to quickly produce high-contrast marks across various materials without sacrificing quality.
Can UV Laser Markers Be Easily Installed on Existing Packaging Machines in the Pharmaceutical and Medical Products Industry?
Yes, compact heads easily replace existing thermal printers and attach seamlessly to various packaging machines, including horizontal, vertical, bag-feeding, and stick packaging types.
We’re here to provide you with more details.
Reach out today!
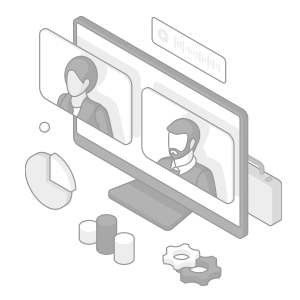