Maximize Overall Equipment Effectiveness (OEE) with UV Laser Coder
Maximizing operational efficiency is essential for thriving in the demanding manufacturing sector. To stay competitive, specific metrics like overall Equipment Effectiveness (OEE) are regularly analyzed.
Improving OEE brings manufacturers many benefits, such as reduced downtime, increased throughput, and enhanced product quality. Marking systems can be easily integrated to enhance overall equipment effectiveness with UV laser coders, improving production efficiency.
-
1UV laser coders can mark more products in the same operating time
-
2Downtime due to ink ribbon replacement and thermal head cleaning
What Is OEE in Production?
No periodic parts replacement required
No periodic maintenance/inspection required
Think of OEE as a valuable tool that helps measure and improve the efficiency of production processes. It considers three major factors that affect equipment performance:
- Availability: The time a machine is actively running compared to the planned production time, accounting for downtime caused by equipment failures, maintenance, or changeovers.
- Performance: Tracks machine speed versus its ideal speed.
- Quality: Assesses the percentage of defect-free products to minimize waste and meet standards.
No line stoppages
No consumables
No faded marking
Simplified remote status monitoring
By computing OEE, manufacturers identify inefficiencies, enabling businesses to proactively enhance operations and raise their OEE rating. According to McKinsey research , increasing overall operational equipment effectiveness significantly impacts output and earnings, especially with cutting-edge manufacturing technologies like digital performance management and real-time data analysis.
Line conditions:
100 operations/minute, 10 hours/day, 25 days/month, 1 ink ribbon replacement/day at 5 minutes/ribbon replacement.
-
1When operated at the same operation time:
150,000 units more per year
* When producing the same production volume: 1,500 minutes (2.5 days) less per year without the need to replace ink ribbons
We’re here to provide you with more details.
Reach out today!
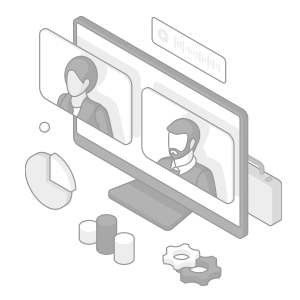
Challenges in Achieving Operational Equipment Effectiveness
Achieving high OEE is challenging, especially in industries where production processes are complex and time-sensitive. One of the key obstacles to maximizing OEE is downtime, which often occurs due to the need to change consumables like ink or ribbon in TTO (thermal transfer overprint) systems. Each time a consumable is replaced, it counts against OEE, reducing overall efficiency.
Studies have shown that downtime accounts for as much as 20-30% of OEE losses in many facilities, with consumables being one of the main contributors. Additionally, traditional marking systems are often difficult to integrate into packaging machines, requiring significant space and causing delays in setup. A lack of seamless integration not only slows production but can also lead to operational bottlenecks, further causing efficiency losses and inefficient production lines, where the time spent on maintenance and setup erodes OEE. Manufacturers are often forced to choose between improving speed, quality, or equipment availability.
Example of expected costs
Emerging technologies like compact laser coders aim to address these challenges, offering smaller footprints and higher adaptability for modern manufacturing environments.
-
1Maintenance and inspection costs
-
2Ink ribbon costs
-
3Thermal head costs
No need for cumbersome ribbon management
Ease of use and installation
Discover more about this product.
Click here to book your demo.
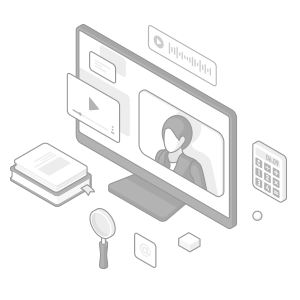
Enhancing OEE Overall Equipment Efficiency with UV Laser Coders
A UV laser coder offers a welcoming solution to these challenges. Without frequent maintenance or setup, UV laser coders ensure smooth production and higher performance. Their compact size simplifies integration into packaging lines, maintaining continuous, high-quality marking without disrupting workflow. Manufacturers using UV laser coders report significant reductions in downtime, leading to higher OEE.
Problems with Conventional Systems Are Eliminated by Using a UV Laser Coder
-
1Line stoppages caused by empty ink ribbons result in stockpiling of unpackaged products.
-
2Having to deal with stockpiling products means fewer workers for other processes.
-
3The time needed to restore operations depends on how skilled maintenance workers are.
Why Operational Equipment Effectiveness Is Key to Competitive Manufacturing
Improving OEE is critical for meeting production targets, maintaining high standards for product quality, and controlling costs. The good news is that manufacturers can maximize resources, cut waste, and speed up product delivery by improving OEE overall equipment efficiency.
Continuous production with no need to stop lines
For industries like food and beverage, where packaging lines often operate at maximum capacity to meet seasonal or promotional demands, minor improvements in OEE can result in substantial savings. For instance, a 5% increase in OEE on a packaging line can translate to thousands of additional units produced weekly, significantly boosting revenue. Besides meeting high demand, manufacturers must also ensure that product quality remains consistent.
High OEE also supports sustainability goals by reducing waste and optimizing equipment usage. Innovation solutions like the FP-1000 Series laser coder help manufacturers meet greener operational standards.
Curious about our pricing?
Click here to find out more.
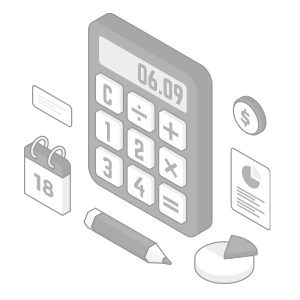
Boost OEE with UV Laser Coders: The Future of Production Efficiency
The future of production efficiency lies in systems that can streamline processes and eliminate bottlenecks. Leading the way in this change is the FP-1000 Series laser coder, which provides fast, high-quality coding with little downtime. Because these coders are simple to integrate into packaging machines and don't require consumables, they offer a scalable solution for companies trying to maximize their OEE scores.
Technologies like laser coding systems will remain essential for raising OEE as manufacturing processes change. By adopting them, businesses can run their production lines more smoothly and stay competitive in the global market. Tools like this will continue to be important in the bright future of productive operations and production.
Contact KEYENCE today to learn how you can improve your manufacturing procedures and overall equipment effectiveness with UV laser coders.