Thermal Transfer Overprinter vs. UV Laser Coder Comparison
Businesses, especially those in manufacturing industries, often rely on an assortment of different printers in their daily operations. Some industries require high-volume, high-speed printing, while others get by with basic and more cost-effective printing just fine.
The high demand for more adequate and cost-effective printers resulted in different types of industrial printers appearing on the market. The two most commonly used printer categories, at least in industrial settings, are Thermal Transfer Overprinters, also known as TTOs, and Laser Printers.
We’re here to explore the differences between thermal transfer overprinter vs. UV laser coder and help you decide which type best suits your needs.
Understanding Basics of Thermal Transfer Overprinting vs. UV Laser Coding
Understanding the basics of thermal transfer overprinter vs UV laser coder technologies for packaging and labeling helps you see each type’s distinct advantages and limitations. This is crucial when it comes to making an informed purchasing decision, especially if you’re looking to upgrade your print quality across the entire production process.
Thermal printer
UV laser coder
Permanent Marking
One of the most important factors in the discussion of thermal transfer printing vs. UV laser coding is the printing technology. TTOs rely on heat to transfer the print onto the substrate. They’re equipped with thermal heads—which typically consist of small thermal elements—that generate the heat required for printing.
Thermal printers
Unlike direct thermal printers, which cause a chemical reaction in the paper’s coating to produce a print, TTOs transfer the ink from a thermal ribbon onto the substrate. Basically, the thermal elements inside the head press the ribbon into the substrate, transferring the ink.
UV laser coders
KEYENCE’s UV laser coders, such as the FP-1000 Series, rely on a UV laser to cause a chemical reaction within a titanium-dioxide layer that’s beneath the transparent laminate layer of film packaging. This creates a permanent mark on the packaging, which is additionally protected by the laminate layer, but why do companies need this technology?
-
1Laminated surface (transparent)
-
2Marking layer
-
3Other film layers
-
4Sealant layer
Print Quality
When it comes to print quality, UV laser coders have a clear advantage over thermal printers, mostly due to the size limitations associated with thermal elements within the latter’s printhead.
Standard thermal printers have a print resolution in the range between 200 and 400 DPI (dots per inch), while pricier options may feature printheads with up to 600 DPI print resolution. However, these are exceptionally expensive and less common.
UV laser coders, on the other hand, have much higher printing resolutions, usually ranging from 200 DPI to as high as 2,400 DPI. Of course, the higher the DPI, the sharper and finely detailed images the laser can produce. However, it’s important to note that DPI is just one aspect of print quality. Substrate selection and print speed play a crucial role as well. KEYENCE's FP-1000 UV laser coder offers unmatched print quality and can print on a variety of packaging film substrates.
One of the most important factors in mark quality is permanence. TTO ink marks struggle to adhere in dusty or wet environments and then the code is often easily rubbed off or smeared during shipping and handling of the product. The chemical reaction of the UV laser mark is a change to the material that is below the surface and 100% permanent.
Oil
Powder
Alcohol
Heat sterilization
Conventional thermal printer
* Results comparison after rubbing on the marked area of film exposed to powder before marking
UV laser coder
Cost
Thermal transfer printing vs. UV laser coding cost analysis requires we talk about the upfront and the operating costs over time, as there are crucial factors when determining which printer type to purchase.
TTO printers are typically less expensive to purchase, but they require thermal ribbons, which are consumables, to operate. This adds to the operational costs of TTO printers, and having to store new ribbons and dispose of the old ones poses several different questions associated with storage space and adequate and environmentally friendly disposal.
The heating aspect of the thermal print head also causes the print head to burn out and fail. Print heads need to be replaced anywhere from every few months to years. There are countless other mechanical components that can fail inside the print head that will also periodically need to be replaced. These costs add up over the lifetime of the TTO.
UV laser coders sport a heftier price tag upfront due to the complexity of technology. However, they offer significantly lower operating costs over time since they don’t require thermal ribbons. And since they have no mechanical parts and don’t make contact with the substrate, they’re incredibly durable and long-lasting. KEYENCE's FP-1000 also has a user-friendly, intuitive interface that minimizes the need for costly training and maintenance.
No ink ribbon costs
No head replacement costs
No air-related costs
Downtime and Maintenance
Downtime and maintenance are part of the operating costs of thermal transfer overprinter vs. UV laser coders. They’re critical considerations for any business looking to optimize its production process and maximize productivity.
TTOs rely on physical contact with thermal ribbons and are thus typically subject to frequent maintenance intervals. This includes replacing the ribbons when they run out and cleaning the print head. Don't forget about any unplanned downtime due to a failed print head, mechanical parts breaking, and issues with print quality. These frequent issues accumulate over time and result in a notable increase in running cost over the lifetime of a TTO. Additionally, failing to perform these tasks adequately only leads to more operational downtime.
UV laser coders are great at reducing downtime, as they’re designed to replace TTOs—implying that they’re specifically designed to alleviate all drawbacks associated with thermal transfer overprinters. They have no direct contact with the substrate, and there are no consumables to replace, which makes them perfect for 24/7 operation. Maintenance of UV laser coders is limited to occasional wipe down of the lens depending on environment. This is especially true for the FP-1000 Series, as it eliminates any downtime caused by replacing ink ribbons and thermal heads.
-
1UV laser coders can mark more products in the same operating time
-
2Downtime due to ink ribbon replacement and thermal head cleaning
We’re here to provide you with more details.
Reach out today!
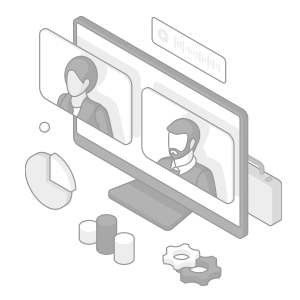
Thermal Transfer Overprinter vs. Laser Coder Applications and Industries
Despite their drawbacks in terms of maintenance and print quality, TTOs are versatile and favored by many industries due to their compatibility with a wide range of substrates. For example, they’re highly favored by the food and beverage industry as well as the pharmaceutical industry due to their capability to print legible information on small packages.
With that said, UV laser coders are generally more favored across various industries, including food, beverage, and pharmaceuticals, particularly due to their ability to produce long-lasting prints that don’t fade as conventional prints do. Unlike inkjet and TTO prints, laser prints can’t be dissolved by oils, alcohol, or heat since the marking isn’t on the substrate surface but beneath a protective laminate layer.
Discover more about this product.
Click here to book your demo.
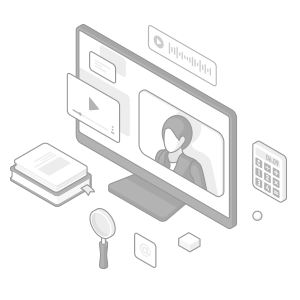
Summary
From a purely technological standpoint, when it comes to thermal transfer overprinter vs. UV laser coders, UV laser coders, such as KEYENCE’s FP-1000 Series, are more advanced, reliable, and cost-effective industrial printing solutions.
This doesn’t mean that TTOs aren’t without their use; smaller-scale manufacturing and production processes might not be able to justify the expense of buying a UV laser coder, which still makes TTOs relevant in modern industrial settings.
However, when comparing to the higher price of conventional UV laser marker on the market, FP-1000 Series is an affordable solution that will allow manufacturers to attain the benefiits of damage-free and permanent laser marking on packaging films.
KEYENCE also offers leasing and financing options on the FP-1000 UV laser coder to assist customers in acquirin an equipment without having to pay the full purchase price upfront.
If you’re considering upgrading to your industrial printing setup, contact KEYENCE; we’ll answer any questions you might have regarding UV laser coders and their integrations into existing production systems.
Curious about our pricing?
Click here to find out more.
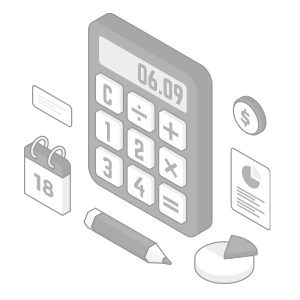