Data Acquisition (DAQ)
Data Logger vs PLC (Programmable Logic Controller)
-
Tags:
- Data Acquisition
Modern industries rely on data-driven manufacturing processes that value speed and precision, underlining the importance of reliable and efficient process control and data acquisition (DAQ). As these needs continue to grow, so do the features of various systems that facilitate their fulfillment, leading to a considerable overlap in functionalities between data loggers vs PLCs.
Despite this, data loggers and programmable logic controllers are very different device types with unique systems and industrial applications. However, they do integrate nicely with one another, so in this guide, we’ll discuss the difference between data loggers vs PLCs and the advantages of each.
Understanding Data Loggers
Data loggers are compact and portable all-in-one devices specifically designed to read the data from a sensor input, condition it, and store it as time-stamped data for subsequent analysis—a process known as logging.
Whatever physical property you’re measuring, you’re likely to find an analog-to-digital converter unit with an accompanying sensor that would “sense” the analog data over time, convert it into digital form, and store it for further analysis.
The internal clock is the primary input determining when to make and store a specific measurement from an input sensor. The type of physical property you’re measuring determines the type of sensor you’ll use—for example, a temperature sensor. Depending on the type of logger you have and the requirements of your specific application, you might use one sensor or an array of sensors.
Also, depending on the type of complexity of your data logger, your device might allow you to measure different physical properties simultaneously and record them as time-stamped data. As such, they’re considered more reactive devices with an emphasis on quality assurance.
However, modern data loggers possess some control elements in their design, which means they can trigger simple control processes upon measuring a predetermined triggered value of the measurement they’re logging.
These devices are most commonly used in environmental monitoring, supply chain logistics, and any other application that demands precise recording of data over time.
We’re here to provide you with more details.
Reach out today!
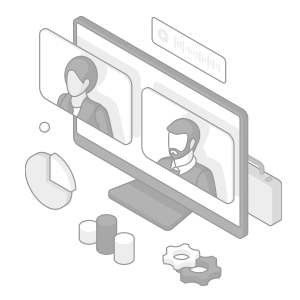
Understanding PLCs (Programmable Logic Controllers)
Unlike data loggers, which record data over time, PLCs, also known as Programmable Logic Controllers, are primarily used for manufacturing process control. These ruggedized computers perform logic operations based on input signals from various sensors or other devices and execute an output, or a series of outputs, based on pre-programmed conditions.
Instead of reading the data of a particular sensor and storing it as a time-stamped data point, PLC data loggers take a sensor input and trigger a corresponding output. As such, PLCs are capable of controlling more complex processes, including real-time control, process adjustment, and simultaneous execution of multiple control strategies and protocols.
This broader functionality also means that PLCs aren’t as user-friendly as data loggers. PLCs rely on programming logic for process control, which involves the use of specialized languages, such as Ladder Logic, Structured Text, or Function Block Diagrams.
However, since they’re used for manufacturing process control, PLC data loggers also come equipped with basic data acquisition capabilities, usually at lower sampling rates. This functionality can be expanded by integrating data logging solutions into process control, allowing PLCs to acquire data from areas that don’t typically require control, only monitoring.
Beyond their process control capabilities, PLCs’ ability to manage data and communicate with other systems makes them extremely useful.
Importance of Data Acquisition and Control Systems in Various Industries
Both data acquisition and control systems are used in almost every conceivable manufacturing industry, including food and beverage industries, medicine, cosmetics, consumer and industrial electronics manufacturing, chemical manufacturing, iron and steel production, petroleum and coal products manufacturing, automobile and auto parts manufacturing, and many others.
Modern manufacturing processes prioritize speed and precision, and DAQ systems are necessary for measuring and recording detailed time-stamped data from various sources—mostly sensors. These systems enable manufacturers to capture specific data over time and subsequently analyze said data to identify different trends, as well as track production line performance.
This data collection enables manufacturers to make informed, data-based decisions that positively affect production. Additionally, modern data loggers and data acquisition systems have integrated control elements that enable them to trigger different control actions, making them suitable for use in quality assurance applications, particularly when dealing with perishable goods.
However, they’re not capable of broader process control, which is where Programmable Logic Controllers come in. These control systems allow for the automation of complex manufacturing and production processes, ensuring their efficiency, reliability, safety, and compliance while also reducing the likelihood of human error.
Ultimately, the differences between data loggers vs PLCs are that they’re fundamentally different devices serving their purposes in the manufacturing and supply chains. Data loggers typically record data and feature limited control elements, while Programmable Logic Controllers control manufacturing processes and feature some limited data capabilities.
Despite their differences, both data acquisition and Programmable Logic Control systems are crucial for manufacturing and production industries, as they ensure more efficient production and quality.
Discover more about this product.
Click here to book your demo.
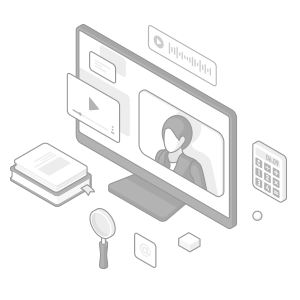
Advantages of Data Loggers vs Programmable Logic Controllers
The advantages of data loggers vs PLCs are application-dependent due to the inherent differences between these devices. Both PLCs and data loggers come in different shapes and sizes, but PLCs are capable of handling more complex processes, which also encompass some data acquisition and storage.
However, PLCs tend to be limited when it comes to collecting vast amounts of time-stamped data over time, making them ill-suited for applications that prioritize data acquisition. One of the primary advantages of data loggers vs PLCs is that they’re specifically designed to capture and store a wide range of data types, sometimes at incredibly fast data rates.
For example, KEYENCE’s NR-X Series multi-input data logger is its class's smallest and lightest data logger. It measures and collects data like temperature, voltage, current, strain, acceleration, pulse, and many other physical properties at a sampling rate of up to 1 MHz or 1,000,000 measurements per second.
Furthermore, data loggers tend to be more cost-effective and more power-efficient in applications that prioritize continuous data acquisition over a prolonged period, as well as subsequent analysis of collected data.
Streamline Operations and Efficiency with Data Loggers
Using data loggers vs PLCs mostly depends on the application requirements. If your application requires continuous time-stamp data capture, data loggers are a more specialized, cost-effective way to read and record time-stamp data suitable for further analysis.
They’re more oriented toward quality assurance rather than process control (as is the case with PLCs), which makes them incredibly useful in streamlining your operations and ensuring the quality of your end product.
If you’re interested in learning more about how data loggers could increase the efficiency of your production, contact KEYENCE and inquire about possible integrations with your preexisting production system.
Contact us to learn more about how our advanced technology can help take your business to the next level.
Contact Us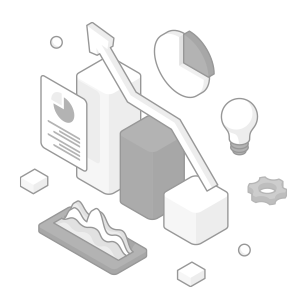