Data Acquisition (DAQ)
Temperature Measurement for the Metal and Steel Industry
-
Tags:
- Temperature , Metal
Solid metals, regardless of where they sit on the periodic table, are more pliable and easier to form when hot. That’s why the metal and steel industry often uses furnaces to liquify, pour, form, and normalize metals during manufacturing.
KEYENCE sensors provide measurement and inspection solutions for every branch of the metal and steel industry and every manufacturing step, including hot metal rolling, cold metal rolling, forming, etc. Since the metal is too hot for most physical sensors to have physical contact, KEYENCE offers a thermometry solution in the form of an FT Series non-contact infrared temperature sensor, which relies on blackbody radiation to detect temperature. The lack of physical contact between the sensor and the object eliminates the error caused by the temperature and hot surroundings.
We’re here to provide you with more details.
Reach out today!
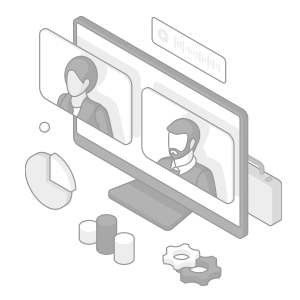
Temperature Measurement Data Loggers for Metal and Steel Manufacturing
The metal and steel industry relies heavily on strictly controlled temperatures. Though the composition of the metal and its chemical bonds won’t degrade, as is the case with plastics, temperature variations can cause melting and pouring issues, along with issues associated with subsequent manufacturing processes.
This is particularly true when manufacturing structural steel or high-performance steel alloys, which undergo a normalization process that necessitates strictly controlled temperatures. The normalization process implies heating the steel to a certain temperature level and maintaining that temperature level for a prolonged period.
Performance steel is even more demanding, as it requires several normalization and heat treatment cycles that increase its hardness. This type of steel is most commonly used in blades, as the treatments help with blade retention.
Temperature measurement in the metal and steel industry can be done using KEYENCE’s NR-X Series, which is the smallest and lightest multi-input data logger in its class. Paired with an NR-TH08P measurement unit and various Infrared thermocouple and RTD sensors, the unit can easily measure and store recorded temperature variance for further inspection.
Understanding Metal and Steel Manufacturing
The metal and steel industry relies heavily on controlled temperature to process metals, from raw materials to the end stock, especially since the temperature plays an important role in the formation of a metal’s crystalline structure, which subsequently affects its mechanical and sometimes even chemical and electromagnetic properties.
Steel is among the most commonly used alloys, and it generally melts at 1,600°C depending on the composition and carbon content. After pouring, the metal is usually forged or rolled. This lengthy process happens at 1,100°C to 1,250°C, depending on the type of steel, and often requires re-heating to maintain the correct temperature.
Once rolled or otherwise formed, the steel often undergoes a normalization cycle at which it’s exposed to temperatures ranging from 830°C to 950°C at prolonged periods to achieve uniform heating. This refines the grain of the steel and improves its mechanical properties.
Integrating Temperature Measurement into Metal and Steel Manufacturing Processes
Integrating temperature measurement into metal and steel manufacturing processes ensures high quality of metal and steel products. Since temperature is an essential factor in determining the mechanical and electromagnetic properties of metals and steels, precise temperature measurement and storage using data loggers is necessary to make sure that the end product also fits the necessary requirements.
If you’re interested in integrating temperature measurement into the metal and steel manufacturing process, KEYENCE offers measuring solutions that extend beyond just temperature. Our sensors can also measure the width, thickness, and outer diameter of metals and steels, even if they’re still white hot.
Contact us today for more information!
Contact us to learn more about how our advanced technology can help take your business to the next level.
Contact Us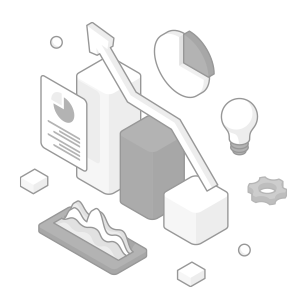