Data Acquisition (DAQ)
Multi-Data Collection for Extruders
-
Tags:
- Data Acquisition
Stable production of extruded articles requires process control. This control is based on measured data such as temperature, pressure, flow rate, and motor load. The NR Series multi-input data logger allows you to measure and record not only the temperature, pressure, extrusion rate, and discharge of dies in the extrusion process but also the outputs from dimension measuring instruments after molding. You can collect various pieces of detailed data during and after molding, leading to a more stable extrusion molding line.
Extrusion data collection systems must be able to simultaneously measure and monitor more than one measurement unit to guarantee quality control and process optimization.
Learn more about extrusion process control and the KEYENCE NR Data Acquisition System (DAQ) Series.
Addressing Challenges in the Extrusion Process with Data Collection
Extreme temperature, pressure fluctuations, and speed are the top variables that can cause challenges in extrusion.
Exposure of sensitive materials to high or low temperatures can lead to the material becoming too dense or damaged. Temperature-related issues are not limited to heat transfer in the extruder barrel. They are also a concern in other areas of the extrusion process where the right amount of temperature must be maintained.
Extrusion Process Control
Extrusion process control also becomes challenging in situations of high or low die inlet pressure. Unstable melt flow can result in problems such as dimensional inaccuracies, surface imperfections, and uneven wall thickness.
Insufficient inlet pressure not only affects the material being used in the extrusion process but also can impact equipment. The die could break or the motor could be overloaded due to insufficient pressure.
Speed is important to extrusion lines and is dependent on several factors, such as die design, motor capacity, and material feed.
Addressing these key challenges is important to simplify the work of extruder operators and process engineers, achieve product quality, and achieve overall efficiency.
We’re here to provide you with more details.
Reach out today!
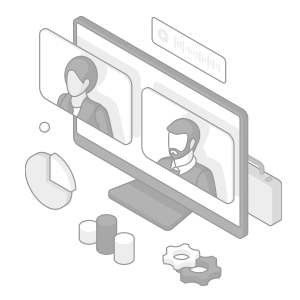
Enhancing Extrusion Process Control with NR Series Multi-Input Data Logger
KEYENCE data acquisition systems provide a reliable solution to address issues related to temperature, pressure, speed, and many more parameters that may stand in the way of quality exclusion process control.
The NR Series multi-input data logger can measure and record the temperature, pressure, extrusion rate, and discharge of dies in the extrusion process and the outputs from dimension-measuring instruments after molding. Operators and engineers being armed with different extrusion data collection systems during and after molding help in achieving a more stable extrusion molding line.
Key Data Metrics for Stable Extrusion Molding
Three important process variables—melt temperature, melt pressure, and motor load—need to be regulated for extruded materials to come out properly.
Abnormal behavior in any or a combination of these three variables will lead to the extruder not functioning correctly.
To guarantee the proper functioning of extruder systems, manufacturers will benefit greatly from using industrial data collection systems like multi-input data loggers to monitor and control necessary variables.
Getting Started with Your Extrusion DAQ System
KEYENCE has made data collection for extruders easier and better. The NR-X multi-input DAQ, for example, supports eight types of measurement units and can handle up to 576 measurement channels. This means line supervisors can continuously and simultaneously record and monitor multiple parameters from different equipment for on-time system adjustments.
The NR-500 is another multi-input data logger solution with all advanced data logger functions for which KEYENCE is known. The NR-500 is portable and lightweight. So, it can be positioned easily where needed. It’s also designed to directly connect with a PC.
To get started with the KEYENCE DAQ system for any extrusion line, contact us today.
Contact us to learn more about how our advanced technology can help take your business to the next level.
Contact Us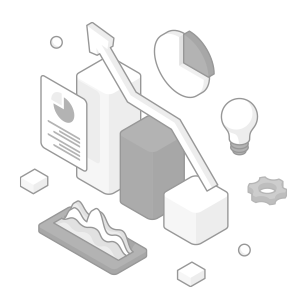