Continuous Inkjet Printers / Case Coder
Best Practices for Implementing Carton Coding Solutions on Production Lines
Carton coding solutions are designed for optimal marking of packaging boxes at different stages of the production process. Carton date and other variable coders include UV lasers, CO2 lasers, thermal printers, and continuous inkjet printers. Carton coding equipment can be installed on a cartoner or conveyor system so cartons are marked as needed before, during, or after the inline production process.
Coding solutions deliver high-speed marking. For example, continuous inkjet printers are used for extreme high speed applications like wire or canning and can more than handle the throughput of cartoners.
Printing example
Installation example
Understanding Carton Coding
Real-time printing of variable data like barcodes and best-before dates is a critical enabler for traceability. Relying on coding by operators or users can result in errors, scrap, and re-work, ultimately leading to costly recalls and regulatory penalties.
Among all the errors caused by expiration date mistakes, 81% were caused by the date being displayed incorrectly. In another 16% of the cases, printed text was missing in whole or in part.
-
1Incorrect date printed
-
2Missing printed text
-
3Other
We’re here to provide you with more details.
Reach out today!
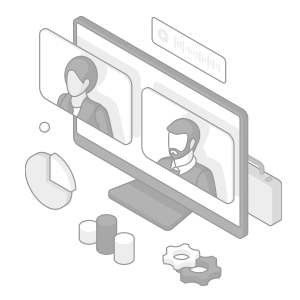
Common Challenges in Carton Date Coding and Traceability
User/Operator Error in Coding
Errors in dates and formats can be caused by human operators. Inaccurate recording of coded information can pose serious challenges down the line.
Lack of Traceability and Product Recalls
Low-quality inline marking of packages can lead to traceability issues. The wrong coding system could lead to smudge markings, which could impact visibility and make it difficult to track products.
Products Are Perishable and Have Limited Shelf Life
Products with limited shelf life require accurate date coding. Inaccurate or missing coding data can result in wasted storage, products, and even health and safety issues for consumers.
Product switching using barcodes
Easy changeover of products is now possible by simply scanning a preregistered barcode. Now one line can support multiple products without having to reprogram the marking unit.
Curious about our pricing?
Click here to find out more.
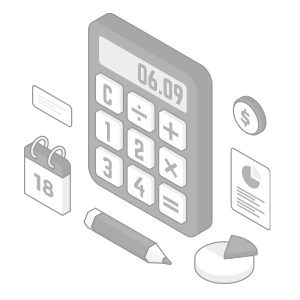
A Flexible Coding Solution Is Needed
Enter the MK-G Series: Its self-troubleshooting capabilities, intuitive interface, and easy integration offer an extremely flexible coding option that adapts to various environments and requirements. This printer can be operated without any specialized knowledge, skills, or training, making it an even more versatile and practical option for businesses.
With automatic maintenance and troubleshooting, it constantly adapts to provide optimal coding solutions. It is increasingly taking over tasks previously done by technicians, offering a single coding solution to simplify processes and boost efficiency.
Using the MK Dock enables self-diagnosis and cleaning to ensure stable startup.
Get detailed information on our products by downloading our catalog.
View Catalog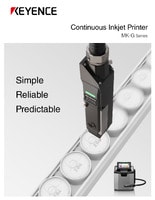
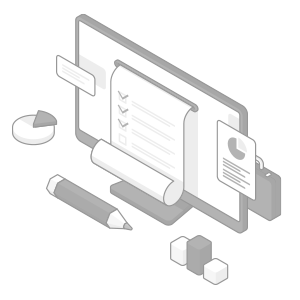
Key Considerations for Selecting Carton Coding Solutions
Production Line Requirements and Speed
Some high-speed cartoners produce over 100 cartons per minute. This means the accompanying inkjet carton printer or other coding solution employed must be able to match such speed.
Type of Packaging Material Used
No packaging material is created alike. It can feature smooth, rough, or glossy finishes. The distinct texture of each type of packaging material can impact its legibility.
Product Information and Coding Requirements
Certain industries have extremely strict coding requirements where coding solutions are employed. They must be able to update complex codes on the fly to print on uneven or curved surfaces with accuracy.
Barcode / 2D code
Cartons
Assessing Current Production Processes and Needs
Coding needs vary by industry. Research internal production needs and suitable coding equipment accordingly.
View a graph showing the MK-G Series operation status.
Performance Analytics
The hourly operation status of the MK-G Series is displayed on a graph. Visualize a wide range of information including error counts, operating hours, temperature, and viscosity as far back as 100 days.
Implementing Quality Control Measures
KEYENCE offers a line of continuous inkjet printers for the food and beverage,
pharmaceutical, and consumer industries. The MK-G Series integrates with existing production lines. Illustrated guides ensure quality control, allowing anyone to use KEYENCE CIJ printers with basic training.
Another key feature is monitoring coding accuracy via performance analysis, identifying errors early for quick resolution and minimal downtime.
Easily link to a print inspection device with just a LAN cable
Additionally, these printers can connect directly with print inspection equipment, further streamlining the quality assurance process. This integration saves time by automatically detecting and rejecting defective products, eliminating the need for manual inspection.
-
1Continuous Inkjet Printer MK-G Series
-
2Intuitive Vision System CV-X Series
-
3Vision Sensor with Built-in AI IV4 Series
Discover more about this product.
Click here to book your demo.
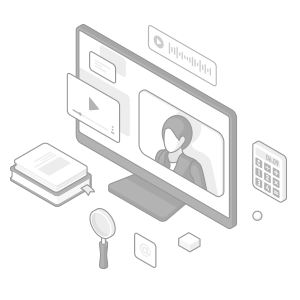
Selecting the Right Carton Coding Technology
To learn more about the KEYENCE line of carton date coding systems and how we help manufacturing lines choose the right coding technology, contact us today.
We’re here to provide you with more details.
Reach out today!
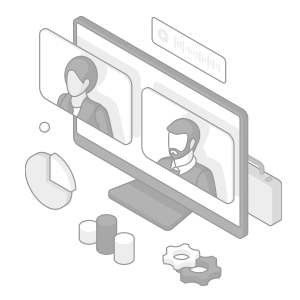