Challenges in Glass Bottle Coding
Beverage, medicine, cosmetics, spices, and even cleaning products are often stored in glass and plastic bottles for distribution. And what do all of these products have in common? As perishable goods, these products must have an expiration date clearly labeled on the packaging.
Ice cream
Cheese (cup container)
Pasta
Companies that package these goods must adhere to industry standards and federal regulations that mandate certain date codes on the packaging. That typically isn’t the issue when it comes to plastic or even metal containers, but glass can potentially be very challenging to print on, barring adequate equipment and proper ink selection.
In this guide, we’ll discuss the challenges of printing on glass bottles and introduce continuous inkjet printers (CIJ) as viable solutions for businesses that have to print on a large number of glass bottles with great speed.
Curious about our pricing?
Click here to find out more.
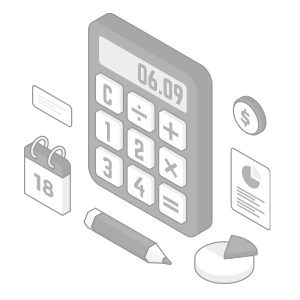
Introduction to Date Coding on Glass Bottles
As stated above, date coding on glass bottles is essential for industries that produce and package perishable goods, as it conveys important information about the product. This information is useful to both the manufacturer, who uses batch numbers for quality control and logistics purposes, and to consumers, as it clearly states the product’s expiration date.
However, as in any mass production, glass bottle coding, or coding on any type of glass container, is all about the volume and the ability to print on as much glass in as little time as possible. It may sound unreal, but it’s not uncommon for bottling companies to date code print on 100,000 bottles every hour. This means that the coding process has to be reliable and fast on top of being legible.
Glass bottle coding isn’t as easy as it sounds due to inherent challenges associated with printing on glass.
We’re here to provide you with more details.
Reach out today!
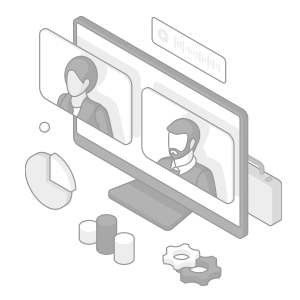
Printing Challenges on Smooth, Curved Surfaces
Printing on glass has its own set of challenges due to the material properties of glass. Many consider glass to be fragile, implying a lack of strength, but that’s far from true. Glass isn’t fragile; it’s brittle and often used for its strength and recyclability.
What makes glass bottle coding so challenging is the fact that glass is a non-absorbent material with a relatively smooth surface and a frequently curved form. This makes the material very hard to print on, as the non-absorbance means that the ink takes longer to dry and cure, the smooth surface might promote smears, and the curved surface area might affect the consistency of the print.
This issue of non-absorbency is mostly solved by using fast-drying inks, while modern printers have their way of dealing with glass bottle curvature, such as using specialized print heads. However, ink selection is also an issue, especially when printing on returnable bottles, which rely on a special, washable ink. The ink has to be durable enough to withstand the rigors of bottling, storage, distribution, transport, and use by the end consumer without being erased in the process.
However, once the bottles are collected and returned to the bottling company for reuse, replacing the glass bottle coding with a new expiration date and lot number is necessary.
Properties of Dye Ink
- No precipitation when mixed with liquid
- Absorbed by print targets
- Short-term fade resistance
-
1Dye ink
-
2Target
-
3Dye ink sinks into targets easily
Discover more about this product.
Click here to book your demo.
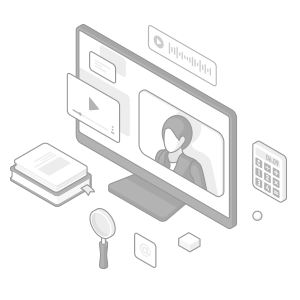
How to Print on Glass Bottles Effectively
Learning how to print on glass bottles involves overcoming the aforementioned challenges associated with glass bottle coding by using specialized equipment application-specific ink and considering environmental factors.
Acquiring a good-quality printer is paramount to producing legible glass bottle coding, and most industries typically rely on several different printer types, including continuous inkjet printers, laser printers, and UV inkjet printers.
Naturally, this affects ink selection. Continuous inkjet printers are the most versatile type, as they print using a wide variety of inks and on several different substrates. Laser printers provide precise and high-quality glass bottle codes and are suitable for environments where ink-based systems aren’t ideal for use. The last is the UV inkjet printers, which rely on inks that cure under UV light—and require specialized ink.
Overall, ink selection is important since it needs to stand out against the background, which is usually the bottle's content, implying the use of pigmented ink, which settles after a period of inactivity within the printer. The ink has to overcome condensation by penetrating and adhering to the bottle surface despite condensation. This also applies to specific inks resistant to condensation that form after printing.
Cosmetics
Glass jar
However, the aforementioned options face inherent challenges. This is where KEYENCE’s strong adhesive inks, like the MK-13, come into play. This specially designed ink is perfect for clear poly plastic films, plastic containers, and smooth glass bottles. It boasts a higher heat tolerance, abrasion resistance, and overall durability due to its stronger proprietary binding mechanism. This means that our ink can ensure clear and long-lasting codes on glass bottles.
Reliable Adhesion to All Materials
Ink doesn't fade from materials that conventional ink does not adhere to. Increased adhesiveness, heat tolerance, durability for rubbing It can stick well to poly films and plastic containers.
Standard Ink
PP material film
Strong Adhesive Ink
PP material film
Curious about our pricing?
Click here to find out more.
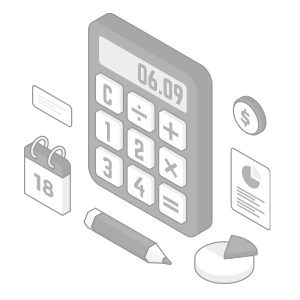
Date Coding Printer for Glass Bottles
Glass bottle coding is typically done at the bottling company at volumes and high production speeds, making continuous inkjet printers one of the most viable options for glass bottle coding due to their versatility and the ability to print at high speeds.
As their name implies, continuous ink printers rely on the continuous flow of ink mixed with a solvent from a reservoir. The ink is pumped from an ink reservoir through a nozzle and is broken up into a large number of ink droplets through high-frequency vibration.
Once the droplets are formed, select droplets are charged by electrodes. The stream of droplets then passes through deflector plates which create an electrostatic field. The charged drops are deflected as they move through the deflector plates, to be ejected from the print head and placed on the product to form the required message.
Droplets that haven’t been electrically charged are recirculated back into the system to be reused. ink travels from a reservoir, passing through a nozzle, and then fragments into numerous tiny droplets by vibration at a high frequency.
There are several benefits provided by CIJ printers for glass bottle coding, including accurate and high-quality print that adheres to the surface and dries fast. Furthermore, the continuous flow of ink prevents the ink from clogging the print head, leading to maintenance reduction costs.
Circulation path
- Solvent tank: Supplies solvent to control viscosity when the ink in the main tank becomes too thick.
- Ink tank: Supplies ink to the main tank when it is empty or when the ink is too thin.
Circulation Principle
-
1Main tank: Stores the ink used in printing. Ink recovered from the gutter is also returned here.
-
2Pump: Pressurizes and feeds the ink from the main tank to the print head.
-
3Pressure-reducing valve: Adjusts the ink pressure.
-
4Piezoelectric element: Oscillates the ink stream discharged from the nozzle to separate into ink particles.
-
5Nozzle: Discharges the ink.
-
6Electrostatic electrode plates: Applies a negative electric charge to the ink particles created from the ink stream.
-
7Electrostatic sensor: Monitors whether the ink particles have the proper electrostatic charge in them.
-
8Deflecting electrode plates: Generates a magnetic field between the electrode plates to deflect ink particles according to their charge. This directs ink particles onto the print target.
-
9Gutter: Collects the ink particles that are not used in printing.
-
10Pump: Retrieves the ink particles from the gutter and feeds them to the main tank.
We’re here to provide you with more details.
Reach out today!
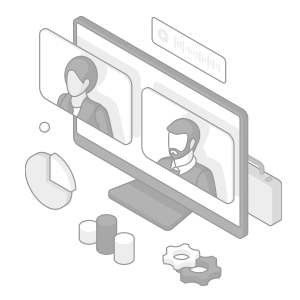
Summary
If you’re interested in glass bottle coding and are in the market for glass bottle coding printer equipment, don’t hesitate to contact KEYENCE and inquire about our line of continuous inkjet printers.
Discover more about this product.
Click here to book your demo.
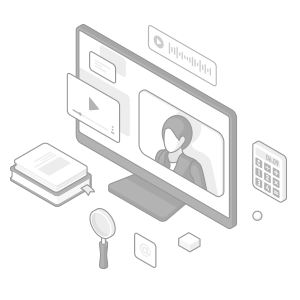
Related Downloads
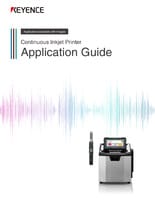
This guide explains continuous inkjet (CIJ) printer applications together with pictures and illustrations. It contains many installation examples in various industries divided into food, medicine, and cosmetics; electrical machinery and electronics; and automotive, metal, and others. These examples show printing on targets specific to each industry.