Continuous Inkjet Printers / Case Coder
Quality and Durable Coding and Marking Solutions for the Wire and Cable Industry
Labeling essential data such as voltage rating, reel or spool number, wire size and type, safety certifications, and other identifying information on wiring and cables is crucial. This practice informs electricians and other users about the most suitable applications for a specific cable or wire design. Additionally, it ensures that manufacturers remain compliant with industry and regulatory standards.
Coding and marking solutions for wire and cable, such as continuous inkjet printers (CIJ), can become problematic. Excessive clogging, adhesion problems, and smudged printing are some issues that can turn any coder into a hindrance rather than an asset in a production project.
Installation example
To ensure manufacturers in the wire and cable industries continue producing quality and safe products to serve the market, KEYENCE is committed to providing unmatched coding and marking solutions for wire and cable manufacturing. Explore how our CIJ for industrial manufacturing provides quality operations.
Discover more about this product.
Click here to book your demo.
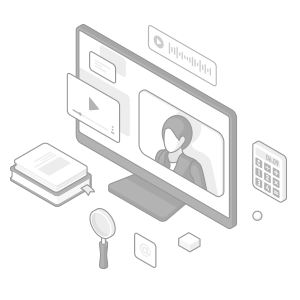
How KEYENCE CIJ Printers/Coders Reduce Downtime and User Intervention in Cable and Wire Manufacturing
Reducing downtime in cable and wire coder equipment to a bare minimum can make all the difference in how fast manufacturers complete projects and deliveries.
Among all the errors caused by expiration date mistakes, 81% were caused by the date being displayed incorrectly. In another 16% of the cases, printed text was missing in whole or in part.
-
1Incorrect date printed
-
2Missing printed text
-
3Other
Smart Dock
KEYENCE continuous inkjet printers like the MK-G Series have assets that enable more uptime. The SMART Dock system provides uniform cleaning without manual cleaning procedures. Over time, the tiny openings that eject ink droplets onto the wiring/cable surface (or nozzles) become dirty. Failure to clean it at the right intervals may lead to print quality issues.
Unlike traditional systems that require manual cleaning to remove ink buildup in the print head, the MK-G Series simplifies the process. Place the print head in the SMART Dock and use the intuitive display to optimize solvent usage. This feature is highly valued, as it reduces the risk of damaging the print head or other components, which is common with manual cleaning in conventional systems.
Using the MK Dock enables self-diagnosis and cleaning to ensure stable startup.
Tool-free part replacement with illustrated instructions
Parts Replacement
Apart from cleaning print heads, replacement parts for wire and cable coding and marking are completely normal and required. However, how fast and easily replacement tasks/projects can be completed is critical to system uptime. The KEYENCE MK-G Series features a no-tool part replacement for easy maintenance. Wear parts have release thumbscrews/knobs for quick disengagement. This reduces downtime and human input compared to conventional coders.
Simply follow the on-screen instructions to solve problems
Maintenance guidance
Even in the event of a sudden error, illustrations that can be used to solve the problem are displayed on the console. Users are interactively guided through each step while checking the machine status, making it possible for inexperienced workers to complete tasks without having to worry about taking too long or making mistakes.
We’re here to provide you with more details.
Reach out today!
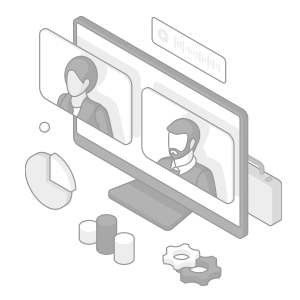
Learn How KEYENCE Coders Improve Print Quality by Reducing Scrap and Rework in the Wire and Cable Manufacturing
KEYENCE MK-G Series has a dedicated camera and character string switch function that reduces print rework and product waste. The dedicated camera reads print data from a sheet or workorder and inputs this content into the printing recipe. This feature helps prevent human input mistakes that could lead to error and rework by ensuring the correct print data for each product.
Character strings can be read with the camera to change print content quickly and accurately.
Correction of Print Details Simply by Scanning Text
INDUSTRY FIRST:
Changing character strings using the camera
Easily change print content simply by reading abarcode or character string on a work order orother location. With no need for input from theconsole, mistakes can be prevented altogether.
Inspection systems are desirable during wire and cable coding and marking to catch errors or defects. While the MK-G Series has functionalities and features that prevent many errors typical to other systems in the market, we took accuracy to the next level by making sure the MK-G Series can be connected to a separate print inspection solution like a vision system so both can work together for high-quality print results.
Easily link to a print inspection device with just a LAN cable
Users can use a single LAN cable to connect the printer to a CV-X Series vision system or IV4 Series vision sensor, both of which are KEYENCE vision products. The system saves inspection data, which the human operator can subsequently examine to determine the intervention direction.
-
1Continuous Inkjet Printer MK-G Series
-
2Intuitive Vision System CV-X Series
-
3Vision Sensor with Built-in AI IV4 Series
Another capability that users love about this cable and wire coder is the consistent print performance under various environmental conditions. Seasonal changes or fluctuations in ambient temperature in print locations could affect the state of ink particles, leading to dirty print heads or clogged print nozzles. Aside from having other functions that help resist seasonal changes that affect print consistency, the MK-G Series has internal functions that adjust ink viscosity for optimal ink state.
Changes in ink viscosity caused by fluctuations in outside temperature can lead to unstable marking on building material production lines.
Particle state:
If the optimum ink state is not maintained, the inside of the head may become dirty, and print quality may deteriorate.
KEYENCE Advantages
Automatic ink particle optimization
The MK-G Series senses the ink particles 10 times per second, so it can automatically adjust itself to maintain optimum ink particle conditions. Stable printing is ensured by suppressing the impact of temperature fluctuations.
Less-than-optimal state of particles
Optimal particle state
Conditioning tank system
The MK-G Series is equipped with a viscosity sensor and conditioning tank for collectiong solvent after cleaning. This prevents ink dilution due to cleaning operations and wasteful disposal of solvent.
Without Conditioning Tank
When washing is performed, the ink viscosity decreases.
-
1Main tank
-
2Ink tank
-
3Solvent tank
MK-G Series
The conditioning tank is used for temporary storage to prevent dilution of the ink.
-
1Main tank
-
2Viscosity sensor
-
3Conditioning tank
-
4Ink cartridge
-
5Solvent cartridge
Curious about our pricing?
Click here to find out more.
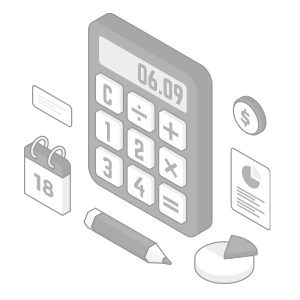
The Key Uses and Benefits of CIJ Coders for Marking and Coding on Wire and Cable Extrusions
Continuous inkjet coders excel as coding and marking solutions for wire and cable; they can mark data on extruded materials consistently due to their versatility and reliability.
The MK-G Series CIJ can print on uneven surfaces without compromising ink adhesion, making it a desired solution for the food and beverage industry. In the context of cable extrusions, CIJ coders can print on rigid or textured wire insulation and similar extrusions. Whether it's thick cables or thin wires, CIJ coders’ versatility enables them to print on various extrusion material sizes.
CIJ coders also provide high-speed printing for high-volume extrusion lines while simultaneously maintaining print accuracy, which is important in avoiding print errors that could lead to non-compliance with required standards.
Products in the KEYENCE MK-G Series line are industrial inkjet printers well-suited to printing on extruded materials. The MK-G Series was designed with various cable materials in mind. Part of what makes the MK-G Series a suitable continuous inkjet printer for wire and cable extrusion is the specialized ink models that adhere well to plastics, rubber, and other insulation materials used in extrusion. Different color inks are also offered.
Whether deployed as a continuous inkjet printer for wire and cable extrusion or just a cable and wire coder that can be relied upon, the KEYENCE MK-G Series comes with features and functions to help enhance print quality while reducing downtime and increasing uptime.
For more information about the product, contact us today.
Printing example
Printing example
Installation example
Discover more about this product.
Click here to book your demo.
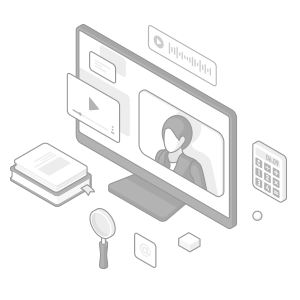
Related Downloads
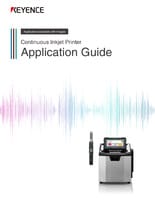
This guide explains continuous inkjet (CIJ) printer applications together with pictures and illustrations. It contains many installation examples in various industries divided into food, medicine, and cosmetics; electrical machinery and electronics; and automotive, metal, and others. These examples show printing on targets specific to each industry.