Continuous Inkjet Printers / Case Coder
Common Coding and Printing Errors and How to Reduce Them
Many industries rely on inkjet printers to mark and code thousands of products every day, which underscores the importance of print inspection and printer maintenance. Industrial printers work tirelessly, often 24/7 (barring preventive maintenance), so it pays to keep them in excellent working conditions.
Failure to do so often results in coding and printing errors, which not only dramatically delay production but also ramp up downtime costs. However, even with regular preventive maintenance, inkjet printers are susceptible to several potential issues, including dirty print heads, fuzzy print, and nozzle clogs.
While preventive maintenance aids in avoiding the majority of these problems, some issues can appear at random. To help you maintain a high level of production efficiency, KEYENCE—a leading supplier of sensors, measuring systems, laser markers, and industrial printers—has produced a list of common issues associated with inkjet coding and printing and how to fix them.
Self-Diagnosis Followed by Automatic Cleaning When Necessary
INDUSTRY FIRST: Smart startup
To start the MK-G Series, simply press the Smart Startup button. The printer will automatically obtain the device status and select the necessary cleaning method. Cleaning is performed only when required and the minimum amount of solvent is used, significantly reducing running costs.
Using the MK Dock enables self-diagnosis and cleaning to ensure stable startup.
We’re here to provide you with more details.
Reach out today!
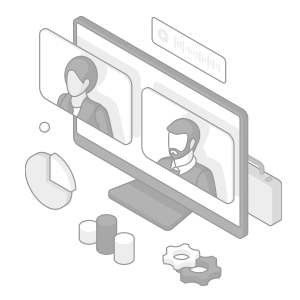
Common Coding and Marking Errors
Continuous inkjet printers, abbreviated as CIJ, found their use across numerous applications in different industries, ranging from perishable goods and industrial electronics to automotive industries. However, just like all industrial equipment, they’re not impervious to printing errors.
Fortunately, most errors are born from the print head getting dirty. This can be caused by a number of things, most notably a clogged nozzle, temperature and environmental fluctuations, static, vibration, viscosity issues, and of course improper handling of the print head. All of these results are the same: downtime or missing prints which will incur additional costs.
View a graph showing the MK-G Series operation status.
Performance analytics
The hourly operation status of the MK-G Series is displayed on a graph. Visualize a wide range of information including error counts, operating hours, temperature, and viscosity as far back as 100 days.
Below is the breakdown of some of the most common coding and marking errors:
1. Operator Errors
Even the best technology systems have a human decision-maker at one point in the production process. The same applies to printing; human operators have to adjust the print code, and it’s thought that a human operative/technician will make one mistake for every 300 coding entries. This is particularly true if the coding entries are input manually.
The risk of error increases with the number of different printing systems and equipment types at different stages of production. Each coding point has its unique settings and operating procedures, and switching between them can lead to confusion, resulting in printing errors.
This occurs often if your operative is working across different systems for the same data entry, which isn’t only inefficient but also increases the risk of common printing errors, especially if different printing systems rely on different code formats.
KEYENCE’s MK-G Series has an optional assist camera that allows operators to scan text or barcodes to update or change programmed print contents instead of manual entry. This significantly reduces the frequency of coding entry mistakes.
Transmission of character string
Preventing printing mistakes
You can switch print data by just reading a barcode or a character string with the dedicated camera, helping prevent mistakes.
Registering product images for reliable switching
The setting change can be confirmed by checking the product name and image.
2. Ink Issues and Nozzle Clogging
Continuous inkjet printers rely on fast-drying ink for operation. This ink is typically mixed with the solvent inside the main tank to maintain ink viscosity. If the ink is too thin, it will splatter or smear more easily.
Stopping and starting continuous inkjet printers opens up an opportunity for ink to clog in the nozzle, pathways, and pump. Nozzle clogs and dirty printheads are by far the most common cause of production slowdowns, causing delayed startups or production interruptions, respectively.
KEYENCE recognizes that nozzle clogs are inevitable with CIJ technology. Instead of making the nozzle less prone to clogs, it has been engineered to be easily replaceable for less money than traditional CIJ nozzles commonly made from lab-grown crystals or stainless steel. These nozzles are embedded in the print head, so replacing them is complex and extremely expensive.
The MK-G Series from KEYENCE employs a patented ceramic nozzle that can be replaced in under one minute by anyone with no tools. It is also much cheaper and recommended to be swapped to maintain production instead of cleaning and flushing like traditional CIJ.
One-touch nozzle replacement
Quick recovery in the rare event of nozzle clogging
The main cause of problems with inkjet printers is clogging in the nozzle. In the event cleaning does not solve the problem, the MK-G Series enables quick replacement without the need for tools. This helps minimize downtime.
3. Misalignment
There are two main misalignments or calibrations that are critical to quality print and uptime with CIJs. First, the ink stream needs to be properly directed and suctioned into the gutter. Failure in this regard will stop production. This is caused by clogged nozzles, discussed above, or mishandling of the print head. The next critical calibration is the dots or break point.
A proper break point is dependent on ink viscosity and needs to be adjusted based on changes in the environment. Improper break point results in inconsistent ink dots that are prone to splatter which will get the printer head dirty, reduce print quality, and cause downtime.
The MK-G Series employs KEYENCE’s sensor expertise to monitor dots and their break points 10 times per second. This active, real-time calibration is compared to traditional CIJ's reactive manual calibration via a jeweler's eye and a skilled technician. The constant adjustments significantly reduce the frequency of print head cleanings, improve quality of print, and avoid down time.
Particle state:
If the optimum ink state is not maintained, the inside of the head may become dirty, and print quality may deteriorate.
Eliminate temperature-based printing problems
Automatic ink particle optimization:
The surrounding environment, temperature, and ink viscosity all have an effect on the condition of ink particles and their suitability for printing. The MK-G Series senses the ink particles 10 times per second, which enables automatic adjustment to ensure the best conditions. This allows the device to provide superior printing at all times, regardless of the environment.
Less-than-optimal state of particles
Optimal particle state
Preventing Common Printing Errors of MK-G Series Using Print Verification Feature
An ounce of prevention is worth a pound of cure, and the same applies to printing or any other industrial process. KEYENCE offers a wide variety of industrial printing and print inspection solutions that can help you automate your printing process, from printing to print inspection and maintenance.
KEYENCE’s MK-G Series continuous inkjet printer features LAN cable connectivity for a direct connection to the print inspection device. This allows for an easier transfer of settings, judgment character strings, image capture triggers, and more.
Print inspection devices, such as the IV Series vision sensor
with built-in AI, ensure that products with printing errors or poor printing quality are not released, providing an additional layer of reliability to your printing and production process.
The console screen on the MK-G Series also serves as a print inspection device display for immediate verification of inspection results. It also allows operators to change the inspection device setting from the MK-G Series console screen.
MK-G Series CIJ printer also features USB ports for USB memory storage, enabling the printer to save the images captured by the IV Series vision sensor for further inspection and traceability.
Easy connection to a print inspection device
The MK-G Series can be connected to a print inspection device with a single LAN cable.
This reduces the risk of operation mistakes.
-
1MK-G Series
-
2CV-X Series Vision System
-
3IV Series Vision Sensor
Inspection data can be saved
The image data captured during inspection can be saved. If a problem occurs, the conditions can be checked later.
Troubleshooting and Maintenance Features
MK-G Series CIJ printer is equipped with additional troubleshooting and maintenance features. The printer analyzes, self-diagnoses, maintains, troubleshoots, and then, in the event it requires operator assistance, will walk through the issue with step-by-step instructions and video guides. This makes maintenance a breeze, no matter the experience level of the technician.
The printer has an auto-shower cleaning feature. A specialized sprayer in the print head targets the nozzle and deflector plates, the two critical components in maintaining print quality. The MK-G Series is also equipped with a viscosity sensor for automatic viscosity adjustments and a conditioning tank system for collecting extra solvent used for cleaning and maintenance that would normally dilute the main print tank. This solvent is then used later as needed to keep viscosity in the perfect window.
These systems prevent the ink from becoming too viscous or diluted and ensure print quality.
Conventional head cleaning
Manual cleaning was required to wash residual ink off the inside of the head.
Auto-shower cleaning
In addition to cleaning the ink paths, the key parts of the head are also subject to high-pressure cleaning. This negates the need for manual cleaning.
Conditioning tank system
When ink becomes diluted, print quality deteriorates. The MK-G Series is equipped with a viscosity sensor and a conditioning tank for collecting solvent after cleaning. This prevents ink dilution and ensures print quality remains stable.
3 main advantages
- Powerful cleaning: Thorough washing with no ink dilution
- Dark printed text: Ensures dark and distinct printing
- No draining necessary: Reduced costs by eliminating wasteful drainage
* Included with MK-G1000/MF and MK-G1100 models.
Conventional
When washing is performed, the ink viscosity decreases.
-
1Main tank
-
2Ink tank
-
3Solvent tank
MK-G Series
The conditioning tank is used for temporary storage to prevent dilution of the ink.
-
1Main tank
-
2Viscosity sensor
-
3Conditioning tank
-
4Ink cartridge
-
5Solvent cartridge
Get detailed information on our products by downloading our catalog.
View Catalog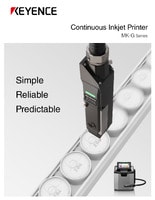
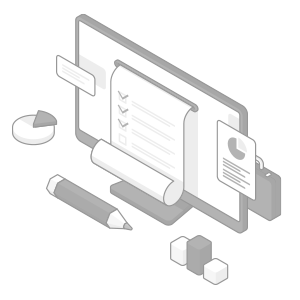
Summary
Printing at high volume is bound to produce printing errors. The key to managing them is to discover printing errors early during production.
KEYENCE offers various industrial printing solutions to enhance your production and effectiveness. If you’re looking to optimize your production printing process, contact us today.
Get the device status anytime, anywhere.
* The MK-G Series does not come equipped with Wi-Fi connectivity.
Check status and perform operations from the Web
Web console:
Connecting the MK-G Series to the Web via Ethernet makes it possible to check the status of the printer from a PC or smartphone. Check remaining ink and solvent levels, or change the print details without ever being on-site.
Information on errors is sent by e-mail, making sure users get the information they need quickly.
Email notifications in the event of problems
E-mail notification function:
Whether just before the ink or solvent runs out, or just after a problem occurs, the MK-G Series is capable of sending out notification emails to a PC or smartphone. These emails ensure users get the on-site information they need in a timely manner, regardless of where they are.
Curious about our pricing?
Click here to find out more.
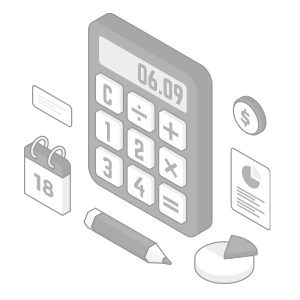
Related Downloads
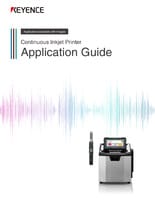
This guide explains continuous inkjet (CIJ) printer applications together with pictures and illustrations. It contains many installation examples in various industries divided into food, medicine, and cosmetics; electrical machinery and electronics; and automotive, metal, and others. These examples show printing on targets specific to each industry.