Continuous Inkjet Printers / Case Coder
Improving Product Traceability and Compliance with Date and Lot Coding in Food Packaging
Traceability is one of the top concerns throughout the food industry, primarily due to foodborne illnesses that develop in anaerobic conditions inside the packaging. Foodborne illnesses and other product safety issues threaten consumer health, so businesses throughout the food and beverage industries are often required to put date and lot coding on their packaging.
Date and lot coding on food and beverage products allows companies to quickly identify and trace every step the product has gone through in the supply chain, ranging from its origin as raw materials to the end consumer. The use of continuous inkjet printers (CIJs) is common to help comply with these FDA and food safety regulations.
However, the process of date and lot coding isn’t without its challenges, and it’s not outside the realm of possibility for there to be issues with date and lot coding, such as imperfections, smudges, or fading, which can lead to a myriad of different problems. Let’s discuss why date and lot coding is important, the various challenges associated with food manufacturing date code applications, and how KEYENCE’s equipment helps resolve those issues.
Particle state:
If the optimum ink state is not maintained, the inside of the head may become dirty, and print quality may deteriorate.
KEYENCE Advantages
Automatic ink particle optimization:
The MK-G Series senses the ink particles 10 times per second, which enables automatic adjustment to ensure the best conditions. This allows the device to provide superior printing at all times, regardless of the environment.
Less-than-optimal state of particles
Optimal particle state
Discover more about this product.
Click here to book your demo.
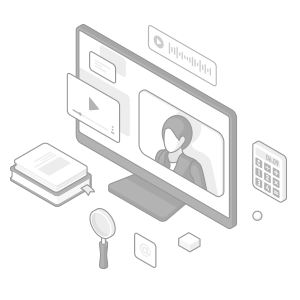
Understanding Manufacturing Codes on Food Packaging
Date and lot coding, often referred to as manufacturing or batch codes, play a crucial role in traceability and quality control in the food industry, as well as retail businesses (as these codes also feature shelf life and best before dates), and ensure consumer safety.
Different types of codes used in food packaging, including date/lot codes, barcodes, and QR codes are used to track and trace the food and beverage products through the supply chain. They enable manufacturers to identify production and distribution details of specific batches, which is essential in case of a product recall, as it allows companies to quickly identify which product batches are affected and need to be withdrawn from the market.
Date / Lot code
Barcode / 2D code
Ensuring Freshness
Besides traceability, date and lot coding convey other production-related information, such as expiration dates on goods that are perishable, which often serve to help consumers determine the freshness of the product.
The use of these food manufacturing date codes is often sanctioned by federal regulations depending on the industry, particularly the food packaging industry, which deals with perishable goods.
Non-contact printing allows for coding on most substrates with high marking permanence while maintaining print quality and increasing uptime in harsh environments.
We’re here to provide you with more details.
Reach out today!
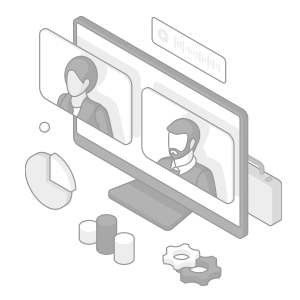
Challenges in Applying Manufacturing Date Codes on Food Packaging
Applying date and lot coding on food packages isn’t without its challenges, especially when it comes to the myriad of different shapes, packages, and materials being used across a variety of manufacturing processes.
Substrate variation creates a major issue with the need for specialized coding solutions like glass and metal to films, foils, wrappers, clamshells, paperboard, cardboard, and plastics such as PET, PP, PE, and many others. For instance, some printers can’t print on glass bottles, which are subsequently cooled and form a condensation layer over the print—it has been known that condensation has the potential to affect the print if inadequate ink is used. Glass is also a non-porous material, which makes ink adhesion even more difficult.
Form-filled packages
Cartons
Plastic bottles
Heat-sealed packages
Cans
Glass containers
Besides offering superb print quality, it’s also important to ensure the printer keeps up with your line speed. This is particularly important because of scaling; if you increase the size and speed of your production, your printer has to be able to keep up.
The production environment is also important because it can affect the print head. Greasy environments eventually lead to build-up around and inside the printhead, which can lead to unnecessary costs due to malfunction-induced downtime.
Another challenge in applying manufacturing date codes on food packaging is downtime and the potential for production stoppages. This can be caused by a variety of factors, such as lack of staffing or heavy maintenance requirements. In order to keep up with high demand and meet tight deadlines, it's important for the coding equipment to be reliable and require minimal upkeep.
Curious about our pricing?
Click here to find out more.
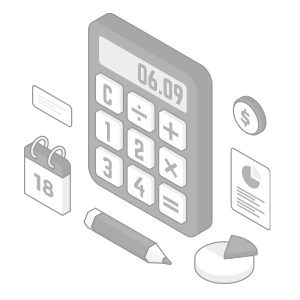
Boosting Compliance through KEYENCE Continuous Inkjet Printer for Food Packaging
Compliance is all about consumer safety, and the main reason why manufacturer coding exists is to ensure that the food is free from contamination and, thus, safe for consumption. Failure to adhere to safety standards imposed by the regulatory bodies leads to serious risks for consumers, which underscores the importance of compliance.
Of course, the lack of food manufacturing date codes leads to compliance issues, which is particularly troublesome if the product leaves the company with missing or unreadable lot/date code. A problem in the coding process on a manufacturing line can lead to significant downtime or worse yet, compliance issues that result in recalls, rework, or scrap, costing money.
The KEYENCE Solution
Food production is a fast-paced environment, with hundreds of products coming off the conveyor belt each minute, each of which needs to be coded. Fortunately, KEYENCE has a solution. Our continuous inkjet printers for food packaging are great for date coding in the food industry due to their key features.
One of the most revolutionary technologies in the market today is KEYENCE's MK-G Series printer. This continuous inkjet printer for food packaging boasts several industry-first features that make it stand out from traditional continuous inkjet printers.
Simple Integration
The compact size, intuitive interface, and simple integration of the printer make it suitable for any production line, even in tight spaces.
One-Touch Nozzle Replacement
Minimize downtime of the inevitable nozzle clog by replacing our patented ceramic nozzle in under one minute. There is no faster way to recover a CIJ.
Smart Dock
The industry-first smart startup analyses and then executes the best maintenance and troubleshooting actions for the printer at the push of a button. This eliminates the need for skilled labor while ensuring optimal uptime and performance.
Using the MK Dock enables self-diagnosis and cleaning to ensure stable startup.
MIL Standard-Compliant Impact-Resistant Structure
MIL and IP-rated print head touch screen and controller structure to handle impacts in any environment.
In the event of a momentary power failure, printing continues for 2 seconds. In the event that the power outage lasts longer than 2 seconds, the head is cleaned and the shutdown process is performed.
Backup Power Module
Another industry-first feature that ensures uninterrupted operation during power blips or an emergency shut down during power outages. Preventing bad codes and significant clogs and damage during outages.
Automation
KEYENCE is the only full-service factory automation company offering CIJ printers.
Easy Integration with Inspection Equipment
Guarantee code compliance with code detection from the IV Series or full blown code OCR and quality inspection with KEYENCE's industry leading vision system CV-X Series.
Networking
Interactive web console to remotely view, remotely control, and receive email alerts from your fleet of MK-Gs. This feature is built into all MK-G Series printers with no subscription required.
KEYENCE’s CIJ printers excel at handling variable data printing, which implies printing product manufacturing and serial numbers at great speeds without any interference from the operating staff. CIJ printers are specifically designed to deliver high-resolution printing with crisp, clear, and well-detailed text, which is very important in industrial applications that demand legibility and clarity.
However, the biggest advantage of CIJ printers—apart from high-quality printing—is their low maintenance requirements. KEYENCE’s MK-G Series CIJ printer is the world’s first self-troubleshooting continuous inkjet printer that’s exceptionally easy to maintain.
The printer performs self-check and diagnostics every time it starts up and performs the necessary cleaning and maintenance processes to ensure proper operation. However, if a major error occurs, the printer will self-inspect, perform troubleshooting, and notify the staff of corrective maintenance it requires, which further optimizes the production process and minimizes downtime.
Get detailed information on our products by downloading our catalog.
View Catalog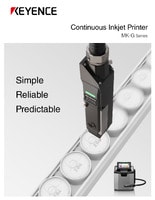
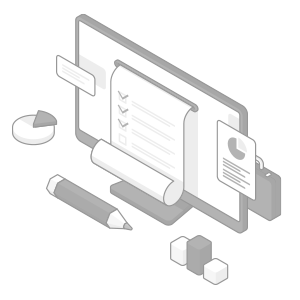
Why Choose KEYENCE?
KEYENCE is the world’s leading supplier of precision measurement technologies and industrial solutions, including CIJ printers. If you’re interested in date and lot coding printers that produce reliable, accurate, and efficient date and lot coding on food packaging materials, contact KEYENCE and take a look at their MK-G Series printer.
Discover more about this product.
Click here to book your demo.
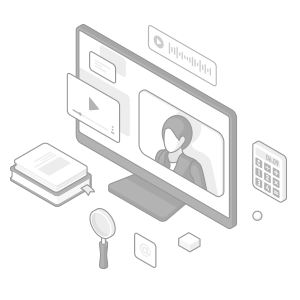
Related Downloads
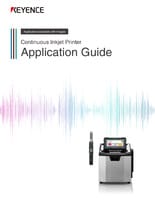
This guide explains continuous inkjet (CIJ) printer applications together with pictures and illustrations. It contains many installation examples in various industries divided into food, medicine, and cosmetics; electrical machinery and electronics; and automotive, metal, and others. These examples show printing on targets specific to each industry.