Overcoming 4 Common Challenges in Extrusion Coding and Marking
Manufacturers of extruded products already have enough responsibilities, including raw material sourcing, keeping up with market trends and consumer demands, and navigating a competitive landscape. Coding and marking challenges are not foreign to extrusion lines, adding to existing issues for manufacturers.
Addressing these challenges will help manufacturers comply with the diverse industry regulatory standards, leading to reduced maintenance costs, downtime, and production efficiency.
In this article, learn about some of the commonly faced issues regarding coding and marking extrusions and how KEYENCE continuous inkjet printers (CIJs) are the ideal solution.
Common Challenges Faced in Coding on Plastic and Metal Extrusions
Coding on plastic and metal extruded materials presents unique challenges due to the nature of the material, production environment, and coding technology.
Installation example
Installation example
1. Maintaining Marking Quality on High-Speed Production Lines
Coding/marking extruded products such as wires and cables is a continuous and fast-moving process that requires maximum production uptime.
Any unplanned downtime can be expensive. It is important to deploy a printer and coder system built to withstand prolonged use in a rigorous operational environment without compromising print quality. However, it is a challenge to get a reliable printer and coder system that can operate 24/7 without issues. Costs and operational requirements are just a few barriers to such systems.
Fortunately, we have the right solutions for coding and marking extrusions. We provide manufacturers with CIJs designed for optimal performance and high-speed efficiency, making them perfect for fast-paced production lines, such as those used in extrusion. In addition to the inherent speed capabilities of CIJ technology, our CIJ industrial printers come with features that ensure high-quality marking and coding and further enhance coding times.
Particle state:
If the optimum ink state is not maintained, the inside of the head may become dirty, and print quality may deteriorate.
The MK-G Series, for instance, features automatic ink particle optimization that helps regulate ink quality levels as the printer experiences changes in the viscosity and surrounding temperature. This ensures consistent quality codes, eliminating costly scrap and rework.
Less-than-optimal state of particles
Optimal particle state
The printer also features a hands-free, automatic shower function that cleans critical print head components for consistent print quality. The auto cleaning eliminates delays associated with manual cleaning jobs, contributing to faster print times.
Conventional head cleaning
Manual cleaning was required to wash residual ink off the inside of the head.
Auto-shower cleaning
In addition to cleaning the ink paths, the key parts of the head are also subject to high-pressure cleaning. This negates the need for manual cleaning.
2. Ensuring Durability of Codes on Various Materials
Code permanence on different types of extruded material is crucial for identification, tracking, and compliance requirements. Coding on plastic and metal extrusions comes with unique challenges due to the material properties and extrusion process settings.
A printer and coder solution should offer fast ink dying times and high adhesion. Both impact the longevity of coded information or data. Prolonged drying times can cause smudged prints and ink bleeding.
With the provision of a wide range of ink options and solvents, we address coding longevity concerns arising from ink drying time and material compatibility. The MK-10 ink model for the MK-G Series is ideal for clear black printing on different extruded materials with a fast drying time of within one second. Yellow and white ink options are also available to ensure clear and legible coding on even dark and colored substrates.
3. Compliance with Industry Standards and Regulations
Coding in the wire and cable industry requires manufacturers to stay current with the numerous industry and regional regulatory standards and their evolving requirements. To adhere to acceptable industry standards, manufacturers producing extruded products must ensure proper coding for every production run.
Accurate coding and marking play a great role in such documentation. With quality coding and printing solutions, manufacturers can avoid the risk of getting sued or fined by clients or regulatory bodies.
A manufacturing business is also at risk of damaging its reputation if it can't manage a product recall situation due to coding errors that slipped by undetected. For these reasons and many more, maintaining strict compliance with quality standards isn’t a mere regulatory requirement but a business necessity.
We offer CIJs for industries where long-lasting and accurate coding on extrusion materials is important to regulatory compliance and clients.
For dependable performance, the MK-G Series features a unit called the MK Dock, which automatically diagnoses the printer for faults and resolves them.
4. Minimizing Downtime and Maintenance Costs
Except for scheduled downtime for preventative maintenance or inspection checks, unplanned downtime due to product printer/coder failure is a challenge for many manufacturers in the extrusion industry.
It's crucial to use a dependable printing and coding system in varying production environments to keep production workflow interruptions to a minimum.
We offer CIJ printers for extrusion product coding built to withstand harsh environmental conditions, including water seepage or intrusion. The MK-G Series features an IP55 rating for the printhead, printer body, and MK Dock. The ingress protection and other robust design features make for its durability in rigorous printing environments. The self-troubleshooting and diagnostic features also reduce the need for experienced technicians and troubleshooting time, which can further minimize maintenance costs.
Furthermore, additions such as a conditioning tank storage in the MK-G Series prevent the ink in the main tank from becoming diluted over time due to cleaning. The solvent collected in the conditioning tank is filtered and recycled back into the main tank. This feature reduces stops for draining a diluted main tank and helps with the conservation of print ink and other consumables that can drive maintenance costs upward.
We’re here to provide you with more details.
Reach out today!
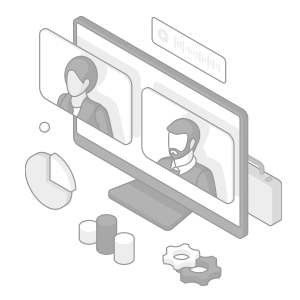
Explore Continuous Inkjet Printers for Extrusion Product Coding Needs
Whether for a plastic extrusion coder or solution that can code on metal extrusions, we offer a range of products, including CIJ for industrial manufacturing. Our print systems are used in different manufacturing lines for their stability and usability.
Continuous inkjet printers are capable of speedy performance and offer durable printing and coding on a wide variety of materials, including porous and nonporous substrates.
Suitable for both plastic and metal extrusion lines, KEYENCE continuous inkjet printing solutions have features designed to meet the many needs of diverse extrusion lines.
Want to learn more about our CIJ offerings? Explore our continuous inkjet printers for coding and marking extrusions, or contact us for more information.
Curious about our pricing?
Click here to find out more.
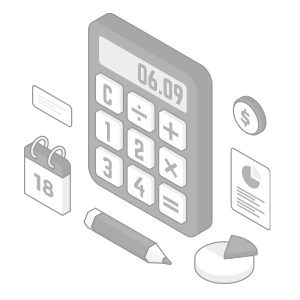
Related Downloads
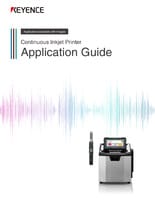
This guide explains continuous inkjet (CIJ) printer applications together with pictures and illustrations. It contains many installation examples in various industries divided into food, medicine, and cosmetics; electrical machinery and electronics; and automotive, metal, and others. These examples show printing on targets specific to each industry.